
Sign In
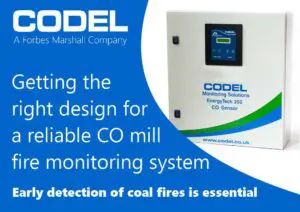
For more information on Getting the design right for a reliable CO mill fire monitoring system talk to Codel International Ltd
Enquire Now
More News
List your company on FindTheNeedle.