
Sign In
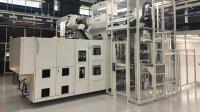
What did the client need?
Promolding BV approached us to provide an intelligent cleanroom solution to protect a medical device manufacturing contract that is due to run until 2032. Effective contamination control is critical, as Promolding is producing optical manifolds for an eye surgery machine. Designed to keep pressure on an eye during surgery when the eye lens is removed, these precision parts feature intricate veins and diaphragms.
How did the client benefit?
Over 9 months, we collaboratively developed a reliable and intelligent cleanroom solution, which works in harmony with Promolding’s ENGEL machines and robots. Each moulding machine has one fixed and one actuated, HEPA filtered, overhead canopy. The automated, sliding HEPA-lite™ canopies provide overhead access for tool changes. They are driven by an actuator with two linear guides, one master and one slave. These drive the filter system to an open or closed position.
How did we help the client?
The canopies feature effective safety mechanisms, sending infra-red signals across the actuators. If the signals are interrupted, for instance by the robot or by operative’s hands, the canopy will deactivate movement, preventing any accidents. The canopies feed into the main cleanroom area, which houses assembly, the plastic welder and packaging.
For more information on Industry 4.0 Injection Moulding Cleanroom talk to Connect 2 Cleanrooms Ltd
Enquire Now
More related to Industry 4.0 Injection Moulding Cleanroom
List your company on FindTheNeedle.