
Sign In
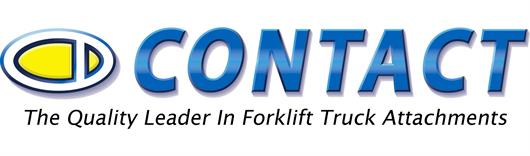
There is a wide range of forklift attachments available to suit every requirement, from tipping skips and safety cages to pallet rotators and crane jibs. Whichever attachments you use, it’s likely that they’re fulfilling an important role in helping you to carry out your operations effectively, and safely. And so, it’s essential that they’re looked after and maintained to ensure they continue to do the job you need them to do.
So, how do you go about maintaining your forklift attachments?
The first step is to carry out a regular risk assessment to identify any potential issues that may impact their safe and effective use. This may involve assessing the wider workplace environment to ascertain any potential hazards, as well as looking at any vulnerabilities from the operator perspective – identifying who and/or what may be at risk and the level of risk, and implementing appropriate control measures.
It's also vital that regular checks are undertaken to ensure the attachment is functioning as it should be. The most suitable person to do this is the operator him/herself as they will be the one with the greatest understanding and insight into how the attachment works on a daily basis and will be best placed to identify any reductions in effectiveness or output.
It may be that your team requires formal training in how to operate equipment safely and to ensure optimum functionality. Every one of our attachments comes with a full set of instructions, but you could need more in-depth, ‘hands-on’ support. Our highly qualified and experienced team can offer this to you on-site, and our training covers both attachments manufactured by us as well as those manufactured elsewhere.
From a legal perspective, under the Lifting Operations and Lifting Equipment Regulations (LOLER) 1998, all your lifting equipment and associated attachments must be examined on a regular basis. In some cases, you may be required to have your equipment examined before using it for the first time (unless you have an EC Declaration of Conformity less than 12 months old and it wasn’t assembled on site), and then subsequently every 12 months – or every six months if the equipment is used to lift personnel. Again, our expert team can undertake this for you should you need us to.
In line with all of the above, of course, is the need to ensure you safely store all operating instructions for each of your attachments which will outline their specific maintenance requirements.
If you have any questions about the maintenance of your forklift attachments or would like to know more about our training offer, do get in touch with our team
For more information on Maintaining your forklift attachments to ensure optimum effectivness talk to Contact Attachments
Enquire Now
More related to Maintaining your forklift attachments to ensure optimum effectivness
List your company on FindTheNeedle.