
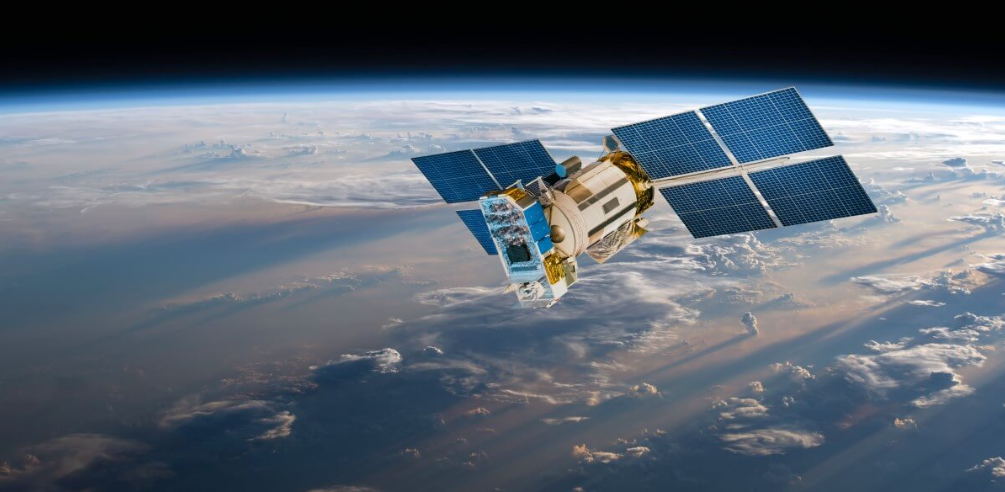
Optical sensors are used in a range of hardware from weather satellites and military drones, to cars and farm machinery. They are increasingly responsible for capturing images that are turned into vital life-saving and commercial data. How can OEMs ensure that their sensor tech retains its pinpoint accuracy even in the harshest conditions?
Where is sensor technology expected to perform?
Optical sensors are called to action in some of the most challenging environments imaginable. In the frozen void of space they are capturing images to track the health of crops and soil hundreds of miles below. Closer to earth, they are mounted on military drones, navigating dangerous skies to gather intelligence with deadly precision.
In the automotive world, they contribute to safety systems, like adaptive cruise control and lane-keeping assist in the daily welter of traffic jams. Meanwhile, in agriculture, sensors mounted on farm machinery must withstand dirt, dust, and vibration to provide the data necessary for precision farming.
Sensors can even find themselves submerged, operating hundreds of meters underwater supporting aquaculture, enduring intense pressure and the corrosive effects of seawater.
7 tips for ensuring the durability of optical sensors in the manufacturing process
Ensuring sensor technology functions reliably in extreme conditions requires a comprehensive approach to manufacturing. It involves precision engineering, rigorous testing, and the considered use of durable materials.
Here are key manufacturing processes and considerations vital for producing sensors at scale so that they can withstand the harshest of conditions:
1. Precision engineering and design
- Microfabrication and nanofabrication: These processes allow for the creation of microscale and nanoscale components essential for the miniaturisation of sensors. Precision at this level ensures high performance and reliability in extreme conditions.
- 3D printing: Also known as additive manufacturing, it enables the creation of complex geometries that are often impossible with traditional manufacturing methods. This is crucial for customising sensor housings or components that need to fit into unique spaces or require specific shapes to function correctly.
2. Material selection and treatment
- High-performance materials: Utilising titanium, stainless steel, ceramics, and polymers like PEEK that withstand extreme environmental stressors.
- Protective coatings: Hydrophobic and conformal coatings shield against moisture, corrosion, and UV damage, extending sensor longevity and reliability. These coatings are critical for sensors operating in humid or submerged conditions, providing an additional layer of protection against environmental challenges.
3. Assembly and Integration
- Cleanroom assembly: Sensors, especially those used in optical and semiconductor applications, require assembly in cleanroom conditions to prevent contamination that can impair sensor functionality.
- Hermetic sealing: This process is used to protect sensitive components from moisture and contaminants. It is essential for sensors used in underwater applications or environments with high humidity.
4. Active alignment technologies
The incorporation of active alignment during assembly is critical for achieving the highest accuracy and performance in optical components. This process corrects any manufacturing variances, ensuring that each sensor operates at its optimal precision level.
The gains in performance offered through active alignment assembly include:
- Superior image quality: In the world of imaging sensors, clarity and precision are paramount. Active alignment ensures that lenses are positioned in the most optimal manner, reducing aberrations and enhancing image sharpness. This precision is crucial for applications with complex imaging tasks ahead of them from high-definition satellite photography to critical medical imaging techniques.
- Enhanced measurement accuracy: For sensors that measure distances or perform 3D mapping, such as those used in autonomous vehicles or augmented reality systems, the accuracy of optical alignment directly affects their reliability. Active alignment minimizes errors, ensuring precise and consistent measurements.
- Optimizsed sensitivity: In analytical applications, including spectroscopy, the precise interaction of light with samples is essential for detecting specific wavelengths. Active alignment ensures that optical paths are precisely configured, maximising the sensor's sensitivity and specificity.
- Efficiency and energy savings: Proper alignment maximises the efficiency of light capture and transmission, reducing the need for additional energy consumption. This not only improves the sensor's performance but also contributes to longer battery life and reduced operational costs. Apparently marginal gains in sensor performance like these can even make a huge difference to the required size and weight of a finished device.
5. Environmental and durability testing
- Thermal cycling and shock testing: Exposing sensors to extreme temperatures and sudden thermal changes tests their resilience and ensures they can operate in extreme climates.
- Vibration and shock testing: Simulating conditions of transport and operation helps in assessing the sensor's durability and its ability to maintain functionality after exposure to physical stress.
- Pressure testing: Essential for sensors that will be used at significant depths underwater or in space, where pressure conditions vary greatly from the surface.
- Humidity and corrosion testing: Ensuring sensors can withstand high humidity and corrosive environments without degradation of performance.
6. Quality control and calibration
- Precision calibration: Each sensor must be calibrated with high precision to ensure accuracy. This process is especially critical for sensors used in applications where data precision is paramount.
- Continuous monitoring of production quality: Implementing statistical process control (SPC) and other quality monitoring techniques ensures that manufacturing processes remain within specified tolerances, and any deviations are quickly corrected.
7. Customisation for specific applications
- Application-specific design adjustments: Customising sensors to meet the unique demands of their intended use is often essential, whether it be for high-speed aerospace applications, deep-sea use, or extreme weather monitoring.
It's through these processes that optical sensor technology can be tailored and manufactured to meet and exceed the performance requirements required for operation in the most challenging conditions.
Businesses who are looking to scale up production of their sensor-led devices should always be looking to the skills and experience of their EMS partners for new insight around materiality, manufacturing and testing.
Focusing on techniques like active alignment, DfM and value engineering could bring new gains in durability, performance and cost reduction to your product. They may help open up new markets and applications for your innovations that previously may have been beyond your grasp.
For more information on How to ensure manufacturing precision in optical sensor technology talk to ESCATEC Mechatronics Ltd