
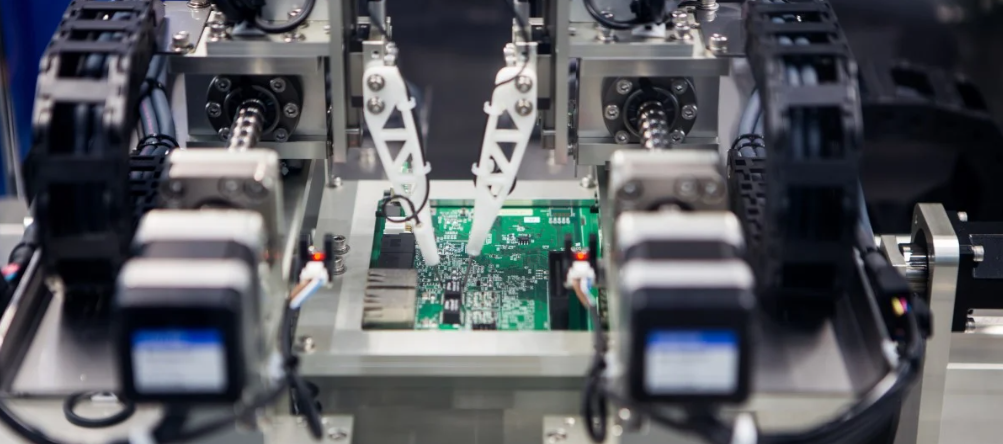
As PCB designs become smaller and more detailed, the more challenging they become to assemble. Jet-based PCB solder printing can help increase the speed and precision of complex PCB assemblies. But there’s still a place for stencil printing in electronics manufacturing. This blog post explores where each approach is best deployed and how they can be combined to maximise efficiency.
Stencil printing and jet-based PCB (Printed Circuit Board) printing are two methods used to apply solder paste or other materials to a PCB to ensure the consistent adhesion of components and their future effective performance.
Here’s a comparison of the two methods and when they can be used to best effect:
Stencil Printing vs Jet Based Printing - What's the Difference?
Stencil printing is a long established and reliable part of the PCB assembly process. It involves using a stencil, typically made of metal or polymer, with precisely shaped apertures aligned with the PCB pad to apply solder, ensuring components can be affixed consistently.
Jet paste printing, sometimes called stencil-free printing, is an additive manufacturing technique that utilises single solder dots to deposit the perfect quantity of solder in the specific spot needed for each component on a PCBA.
This method, often referred to as "jetting," dispenses the solder through a nozzle that travels across the PCB. Jet printers have the capacity to reach remarkable speeds, with the potential to place as many as 1 million dots in an hour.
Discover our Guide to Reducing Electronics Manufacturing Waste
Stencil printing - the pros and cons
Advantages
Precision and control
Stencils can provide a high degree of control over solder paste deposit, resulting in consistent and largely accurate application of solder volumes. For simple assemblies, it ensures clean, reliable connections between components and pads.
Easy to automate and scale production
It’s highly cost-effective for mass production of standard PCBAs.
Disadvantages
Stencil production costs:
Each PCBA project requires a custom stencil. Different types of stencils include standard laser-cut, nano-coated laser-cut, E-formed, and stepped stencils. Unless you have the in-house skills, specifying, ordering and delivery of stencils can take a number of days and mistakes will cost time and money. This can prove an expensive way to prototype.
Not great for intricate designs:
Stencil PCB printing is not effective for very small components, fine-pitch designs, different geometries and different kinds of surfaces.
Size of apertures
The stencil apertures may be relatively large compared to the component pads, making it difficult to achieve the desired accuracy.
Solder waste:
There is always wastage of solder as excess is cleaned away. These incremental costs can add up.
When’s the right time to start a value engineering process? Read our expert advice.
Solder jet printing - the pros and cons
Advantages
Precision and flexibility:
Solder jet printing excels in precision, making it suitable for small components, fine-pitch designs, unusual geometries and complex pad patterns.
Minimises solder waste:
Unlike stencil printing, solder jet printing minimises material waste as solder is directly jetted onto the pads. This helps optimise material usage and cost-effectiveness.
Reduced Setup and Turnaround Times
Eliminates alignment requirements. Solder jet printing offers faster setup time, allowing quick programming and re-programming for different board designs.
Easy to modify designs:
With jet printing - modifications and adjustments can be made quickly even with ‘in-process’ projects.
Print on any surface:
Jet printing can handle a wide range of solder paste types and can deposit solder paste on non-planar surfaces, offering enhanced capability compared to stencil printing.
Supports variable dot sizes:
The ability to vary dot sizes allows for better adaptation to different pad sizes and shapes, improving solder joint quality.
Improved quality control
Jet printing offers improved quality control through the monitoring of solder paste volume and placement
Ideal for prototyping and low-volume production
Its precision, flexibility and ease of set-up makes it ideal for handling complex designs - in cost effective, shorter manufacturing runs.
Disadvantages
Cost
A solder jet printer is an expensive piece of kit. The Capex investment required may not be possible for every business who could benefit from it.
Maintenance
Requires regular maintenance and cleaning to ensure the jetting mechanism functions properly.
Configuration and calibration
You'll need specialist skills and knowledge to configure and calibrate the machinery.
Conclusion
For certain kinds of predictable, unchanging, high-volume PCB assembly needs - stencil printing remains the most cost-effective option. But, if you're developing more complex, crowded and sophisticated PCB designs, accessing the power of solder jet printing is increasingly essential to ensure accuracy and performance. But, as mentioned above, it is expensive to get started.
For OEMs who need access to these specialist services, using EMS providers with the right kit is proving the most sensible and cost-effective way to proceed.
EMS providers like ESCATEC are able to maintain both pieces of equipment in their facilities to allow full process flexibility. Their jet printer is currently installed directly in their SMT line after a stencil printer and before a 3D solder paste inspection station. As I explained in a previous interview:
"We can use pure stencil printing for standard mass production, pure jet printing for NPI (new product introduction) and low volumes, and a combination of stencil and jet printing for mass production applications requiring topping-up with additional paste in critical areas"
You can read our latest post for more information about ESCATECs addition of the Mycronic MY700 jet printer to our SMT production line.
Conclusion
With increased demand for miniaturised, multifunctional PCBs, more and more businesses will need access to this equipment. Using third-party production facilities could help them access the tech they need to meet growing customer demand - in a way that makes the most strategic sense.
For more information on The pros and cons of PCB stencil printing vs jet based solder printing talk to ESCATEC Mechatronics Ltd