
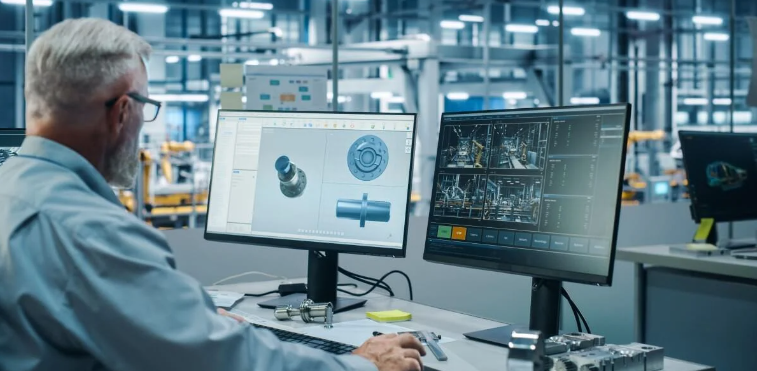
If you are considering outsourcing elements of your manufacturing operation, or already working with a Contract Electronics Manufacturer (CEM), it’s important you keep control of one crucial element – your documentation.
Without a strong revision control process governing your manufacturing data pack (also known as the technical data package), managing production transfers can result in major quality issues.
Mechatronics manufacturing packs require robust governance
In mechatronic production, mismatched revisions between mechanical and electronic specifications can lead to assembly errors, production delays, or excessive rework.
At best, your manufacturing partners may waste time and resources correcting mistakes before they start a build. At worst, they risk producing the wrong version altogether, resulting in parts incompatibility, equipment damage, or failure to meet new standards and regulations.
And all this - because the latest revision number or letter was missing from the manufacturing data pack sent to your assembly partner.
Why revision control really matters in systems integration
Revision control is particularly important if printed circuit board assemblies (PCBA) are being manufactured as stand-alone products, especially if you are looking for a CEM to integrate these PCBAs into a full system or box build assembly. Without accurate information about the exact revision and configuration of each PCBA it’s hard for the CEM to ensure compatibility with other components in the system (e.g., mechanical housings, power systems and interconnects).
OEMs should focus on governance in the production transfer process
Whilst a good Electronic Manufacturing Service (EMS) provider should have systems in place to cross-check all this information, there is also an onus on you as the OEM to ensure that the information is complete and accurate prior to sending it across.
5 tips for strengthening your revision level controls
So, what is best practice when it comes to revision control of your manufacturing data, and when does it make sense to communicate this to your EMS partner?
1. Assign revision levels to each piece of relevant build data
Ideally any build pack for an electronic or electro-mechanical assembly should include the following:
- A Bill of Material (BOM) or parts list
- PCB Gerber files
- CAD data
- Drill drawings
- Assembly drawings
- Schematic drawings
- Drawings for each bespoke or “made to print” item, such as front panels, metal cases, machined parts, brackets, plastic enclosures, identification plates etc.
It’s not uncommon for some OEMs to offer their customers the option of buying an older revision product from them. You may find that service contracts you have in place dictate that the same revision product is supplied to your customers throughout the entire agreement - a common practice for those supplying into military or aerospace sectors.
It is imperative therefore that each of your build documents is assigned its own revision or issue level. In so doing you will be able to keep a record of any changes you make to the product, which ensures that your EMS partner delivers the right product, at the right revision.
2. Be clear on which revision level controls the finished product
Many OEMs use the BOM revision, or the assembly drawing revision, to determine this. Either one is fine to use, however, it is important that you, your engineering team and your assembly partner are consistent in which revision level is used when referring to the top level product. In addition, if your company has more than one design engineer, it’s clearly recommended that they all adopt the same revision level structuring format.
Whilst this may seem obvious, when you start to break down even a relatively simple box build assembly for example, it’s not unusual to find over a dozen different revision or issue numbers/letters forming part of the build pack! It’s important to clarify this from the outset as you don’t want to leave the EMS provider making assumptions on the reference they believe is assigned to the top level product.
A good EMS partner will clarify this with you at the Request for Quote (RFQ) stage but, to save yourself time and any potential paperwork issues further down the line if things fail, it’s far better to communicate this in advance.
3. Determine when top level revision control is required
If you need to make a design change to a sub-level assembly, or any element affecting one of the data documents outlined above, best practice advice is to up-issue the final assembly level also. It’s important to do so as this revision level is going to be the one that you will use when placing orders with your CEM partner.
If you continue to order the same revision top level item, but make design or electrical changes to the sub-levels within, you stand a chance of receiving product back which does not meet your revised specification. If however the changes relate to electronic components, for example, whereby the fit, form and function (FFF) remain the same, these can be controlled via an Engineering Change Order (ECO) or Concession Note which would not necessarily result in a top level revision change.
4. Clearly communicate the changes that you make
There are a number of different methods to communicate such changes, however from experience, I would recommend that you re-issue the entire build pack with each up-revision. Whilst this may feel like overkill, it’s a good way of cross-checking your own documentation and it also ensures that the suppliers do the same. If you only issue details of the specific change, you could be overlooking the impact this has on other parts of the assembly and/or omitted to up-issue other levels, thus causing possible confusion.
You may still want to issue an Engineering Change Note (ECN) with the up-issue to explain the changes. This doesn’t have to be too wordy e.g. “drawing 123-B now 123-C, extra fitting hole added to Part YY”.
Finally, it is recommended that old drawing revisions are marked up as “do not use” or “up-issued”. If you are still concerned, you could always put a note on all drawings stating that the supplier should check the latest revision level before using and/or destroy any older versions they may have. You may also want to consider asking for some form of confirmation from your suppliers to “check for understanding”. After placing an order you’d expect an order acknowledgment, so why not ask for an ECN confirmation after communicating a design change?
5. Replace manual processes with dedicated software
Of course, there are now numerous manufacturing software solutions and dedicated document management systems that are available to streamline version control and ensure the secure transfer of accurate manufacturing data to your partners.
These tools can automate change control processes, making it easier to manage updates and revisions in line with best practice. When approved manufacturing packs are reissued, the software will automatically notify all relevant stakeholders, reducing the risk of errors and ensuring everyone in the chain is aligned with the latest specifications. They can also water-mark obsolete versions and ensure only the latest approved issues of manufacturing packs can be accessed by your partners. If you are still struggling with manual design transfer these solutions can automate and derisk the way you work.
How the right EMS partner can help
The time and resources required to keep tight control of your manufacturing data should not be underestimated. If your products are regularly upgraded or enhanced in order to meet ongoing customer demands, then it’s imperative that such changes are effectively communicated, both internally and to your external supply partner.
If you haven’t yet selected a CEM partner, make sure you focus on this during any site visits or audits you conduct as part of your initial research.
The right EMS providers should have their own sophisticated document control systems and procedures in place to manage every aspect of your build data.
They will be able to demonstrate how customer data is stored and fully backed up within their systems. You should ask the EMS provider to explain the process on how future changes will be managed and also how they control changes to work-in-progress out on the production line as this is a common ‘opportunity’ for errors to occur.
And finally, the EMS Company should be able to provide you with the reassurance that any old, or incorrect build data cannot be accessed by their production teams by mistake. Whilst hard copy documents and filing cabinets have been historically used to control such data, spotting these on any modern manufacturing shop floor should ring immediate alarm bells in your head.
Editors note: This post was originally published in October 2014 and republished in October 2024 for relevance and accuracy.
For more information on Why revision level controls are vital in mechatronic manufacturing data packs talk to ESCATEC Mechatronics Ltd