
Sign In
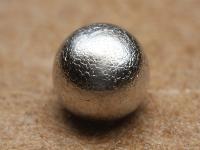
As part of your initial research into potential electronics manufacturing services (EMS) partners, it’s likely you will have been looking into capabilities and equipment lists.
However, with most EMS partners opting for different brands of equipment - particularly when it comes to surface mount assembly (SMT) equipment - carrying out a comparison can become a daunting task.
So, following on from our previous post looking at the differences between flying probe and ICT, we thought it would be useful to look into convection and vapour phase reflow, which often feature on EMS companies' equipment lists.
What is a convection reflow oven?
Convection reflow ovens, such as those supplied by BTU International, contain multiple heating zones (6, 8, 10 and now 12 in some of the latest models), followed by a cooling element which can be individually controlled for temperature. Following the SMT assembly process, the populated printed circuit board (PCB) travels along a conveyor belt located within the oven and is exposed to a controlled time-temperature profile.
As this equipment is situated "in-line" with the SMT assembly equipment, convection reflow allows for a relatively high throughput, without introducing additional handling and "down time". However, a reflow profile is required for each product, which has to be created in advance of production by the engineering team.
While it is possible to control the temperature within each heating zone, it is not possible to do so at component level, which can be a challenge with densely populated circuit boards. Fairly large in terms of footprint, convection reflow ovens can consume a large amount of factory floor space, which may present an issue if space is at a premium.
What is a vapour phase reflow oven?
Vapour phase, or condensation soldering as it is also known, is a very different process and requires the boiling of an inert heat transfer liquid, perfluoropolyether, to create a layer of vapour.
Unlike convection, where the PCB travels through heating zones on a conveyor belt, vapour phase ovens are smaller in footprint and the PCB remains fixed in place.The physical height of the PCB is then adjusted so that it sits within, as well as above or just on the surface of, the vapour layer which completes the reflow process.
During the process very little temperature difference occurs between components of different thermal mass (for example: a large metal heat sink, compared to 0603 chip resistors), which makes it very good for densely populated PCBs. In addition to achieving good wetting and having a smaller physical footprint, the process also provides a high heat transfer which uses less power.
While it is possible to add PCB handling equipment, vapour phase is still a "batch" process and is therefore suited more towards lower volume PCB assembly production, due to extended cycle times. In comparison with convection, they can be relatively expensive to run due to cost of the materials (the main brand of perfluoropolyether being Galden®) and the potential for vapour loss.
So is one better than the other and how do you go about comparing EMS providers that have different equipment?
Unfortunately, it’s not that straight forward and, as this blog post demonstrates, there are pros and cons of each. Vapour phase suits high mix, low volume boards well and eliminates the need for unique reflow profiles to be created for each product, which can take time.
However, it could be argued that some of these savings are then lost due to the reduced throughput and the on-going expense of the materials needed to operate the machine.
When conducting your initial research it’s important to determine what equipment and capabilities your electronic or electromechanical products really need and what would be nice to have. If you’re still unsure then, once you are down to your shortlist of potential suppliers, I’d recommend a visit to each site.
This will give you the chance to talk through your questions and concerns with the production and engineering teams and challenge them on how they overcome some of the issues you have read about.
While the equipment list is an important part of your initial research which helps to paint a picture, walking through the doors of the EMS provider and meeting the teams responsible for the production of your goods face-to-face tells the complete story.
For more information on Convection vs vapour phase reflow within PCB assembly talk to ESCATEC Mechatronics Ltd
Enquire Now
More Blogs
List your company on FindTheNeedle.