
Sign In
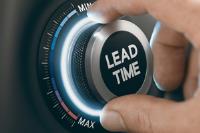
As we enter the second quarter of 2021, we’re edging ever closer to the highly anticipated ‘new normal’.
But the electronics manufacturing industry, like so many other industries, is still riding the wave of the coronavirus pandemic.
Here is the latest quarterly roundup of key developments in the global electronics component market. What does the rest of 2021 have in store for our industry?
Main highlights
On 25th March 2020, the UK Government passed the Coronavirus Act 2020. Just over 12 months later and the UK looks to be heading out of lockdown with the vaccine rollout in full swing and restrictions slowly beginning to lift. The same, however, cannot be said for global supply chains that manufacturing companies are currently managing.
Although the UK is now seeing some positive recovery from the pandemic, Europe are amidst their third wave of the virus, with continued and extended lockdowns and curfews in place in France, Italy, Belgium, Spain and Czech Republic.
In news away from COVID-19, the Ultra Large Container Vessel (ULCV) ‘Ever Given’ became beached in the Suez Canal on 21st March 2021 with rescue attempts finally freeing the ship and successfully re-floating it on 29th March. Having been stuck for six days, it was reported to have held up over $57b of the world’s global trade.
Capacity and lead-time issues
There are still significant supply disruptions to electronics and electro-mechanical supply chains, as well as packaging, metal, and raw materials. Lead-times are continuing to extend with most products affected and prices are continuing to rise.
A large fire broke out at a Renesas plant in Hitachinaka, northeast of Tokyo in Japan, causing significant damage to plant equipment, loss of WIP and contamination of clean rooms. Two thirds of the chips damaged were 300mm semiconductors destined for the automotive market which is currently at a peak of demand.
Taiwan are currently suffering the worst drought the country has seen in over 50 years. Taiwan Semiconductor Manufacturing Corporation (TSMC) are a foundry manufacturing product for a number of semiconductor manufacturers who are ‘fabless’, but also support manufacturers who have their own fabs. When manufacturing wafers for semiconductors, between 2 and 4 billion gallons of ultra-pure water is required per day.
Micron are working through DRAM (DDR3 specifically) backlogs in their Taiwan fab, however there is now a real danger of further issues due to the drought which has the potential to cause allocation on memory lines fairly soon.
Distributors, driven my manufacturer behaviours, are increasingly refusing to allow buffer stocks to be held on behalf of the customer and are instead favouring scheduled orders. As the message has been now for several months – forward orders are crucial to mitigating some of today’s supply chain issues and are critical in securing product for the second half of 2021.
Austin Texas is home to many semiconductor manufacturing plants including NPX, Infineon and Samsung. America suffered some exceptional weather in February 2021, caused by ice storms and tornadoes. To conserve power, semiconductor plants in Austin were made to halt production. Factories were shut down in a controlled way with both Samsung and Infineon back online within a week, whereas NXP took around 4 weeks to get back fully online.
Supply constraints are now across all manufacturers, all products, and all sectors. This is no longer limited to the automotive sector, semiconductors or specific manufacturers such as Microchip. It is critical for supply chains to have full visibility of customer demand to allow orders to be placed to secure stock for the remainder of 2021, and in some instances 2022.
Manufacturer Mergers/Acquisitions
Renesas Electronics are set to acquire Apple chipmaker Dialogue Semiconductor for a reported $4.9b - strengthening Renesas’ global footprint across IOT, industrial and automotive sectors.
Hitachi acquires GlobalLogic in a $9.6b deal. Approval is set to be given by the end of July 2021.
NCAB have acquired PreventPCB in Italy
PCB Technology
Lead-times for both onshore and offshore manufacturing are extending. The Chinese economy is still recovering from the damage of COVID-19 and demand is outstripping available capacity in the Far East, pushing more builds into Europe and the UK.
Shortages of copper-clad laminate continue which is pushing prices up globally and extending lead-times for material.
Two explosions at epoxy resin plants in China have had a significant impact on resin supply and availability in China.
As well as laminate availability and pricing, PCB manufacturing is also reliant upon copper, silver, gold, aluminium, lead, tin and nickel and these raw material prices are increasing globally.
Pricing Uncertainty
Raw material shortages and exponential price increases are still being heavily re-aligned to corrugated cardboard. Raw material is on back order for several distributors who have confirmed pricing is by application only. This is fuelling existing paper/cardboard shortages with paper mills increasing prices and many only supporting existing demand to try to keep up with capacity for longstanding customer.
Manufacturer price increases are frequent and often multiple increases are being observed over a number of weeks. This is a global issue, affecting all products, commodities, manufactures and supply chains.
Common polymer material Polypropylene has increased by 30%, whereas styrene has increased by 60%-70% . The polymer constraints are expected to continue throughout this quarter but could ease in Q3. Oil price increases, as well as strong Asian demand, power outages in the USA and weather disruptions have all fuelled this situation.
Global Economy
Oil pricing has continued to climb over the last quarter with a barrel now costing $63.71 - a $12 increase from 1st January 2021.
Gold pricing has fallen since the start of January and is £1,224.06 per ounce at time of writing, just £10 higher than the 3-month low seen mid-March.
Silver as usual is relatively stable, with pricing today at £17.51 per ounce. The 3-month high was £21.19, with a brief spike seen early February.
Copper is continuing to increase sharply in price. Copper fell slightly with news of the Ever Given vessel becoming stuck in the Suez Canal, however generally it is on an upward trend. It has increased by $870 per tonne since the start of the year, and by $2379 per tonne since 1st October 2020. At time of writing, pricing is $8778.50 per tonne on the LME
Steel rebar is now $632 per tonne, a $2 increase since my last post – however, steel rebar has been fluctuating over the last quarter.
The UK electronics manufacturing industry is in the midst of extraordinary times. But though there may be some way to go before the market stabilises, there is light at the end of the tunnel. In the meantime, forward orders will be critical for securing product for the rest of 2021 and into 2022.
For more information on Electronic component market review April 2021 talk to ESCATEC Mechatronics Ltd
Enquire Now
More Blogs
List your company on FindTheNeedle.