
Sign In
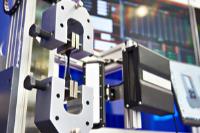
From space satellites and signal boxes to pacemakers and elevator controls, electro-mechanics lies at the heart of a vast array of vital technological systems and devices.
Steering all the elements of a complex electro-mechanical system from design to reality relies on a broad range of skills - from the reading of drawings and other design documents, to expertise in specialist wire and cable interconnectivity and understanding the critical engineering tolerances that can arise when multiple parts are required to work together.
In this blog post we outline five key challenges of electro-mechanical assembly - and the techniques you can use to streamline, optimise and debug your build.
1. Identifying errors and defects
If you’re ordering bespoke items, then it is especially important to inspect those items on delivery to check for any errors or defects.
Having a designated inspection room - and equipping it with the right equipment (measuring instruments, high magnification microscopes, digital calipers etc) - will ensure you're able to monitor items as they come in and identify any obvious issues.
Many common problems will be easy to spot at first glance.
Missing cut-outs to metalwork, inaccurate dimensions or incorrect finishes for example can all be quickly identified and that information then fed back to the relevant supplier team for correction.
But other issues may not become apparent until the physical build is well underway. While individual parts may have passed initial quality and goods receipt checks there is still the question of how they will perform as part of a complete assembly.
2. Minimising product recalls
The addition of moving parts within an electro-mechanical assembly can add an extra layer of complexity to your build, so having an effective test strategy will be crucial.
What’s important is that each individual item is able to operate at high and low tolerances and that it can also work seamlessly in conjunction with the other parts around it - whether it’s checking that two gears smoothly engage, that cables and wires aren’t at risk of becoming entangled, or that a roller can spin freely when it’s connected to a back plate.
The costs associated with product recalls can be substantial, so taking a firm hold of test as early in the manufacturing process as possible will be key to the success of your finished product.
To get the very best results you may find it best to take a holistic approach by using a variety of complementary techniques depending on the nature of the assembly.
3. Reducing waste
For manufacturers looking to increase their quality and manufacturing capacity, it's vital to find ways to reduce waste, keep a handle on lead times and minimise the risk of reworking.
By adopting a lean manufacturing approach - using interactive technical documentation and variant management controls - you can manage your product lines more efficiently, enhance interdepartmental communication and ensure every aspect is accounted for throughout the assembly process.
4. Combating tolerance issues
The use of computer aided design (CAD) modelling software can play a huge role in enhancing the quality, efficiency and precision of your finished product.
CAD helps not only in the design phase but also in giving you the ability to fully analyse any strengths and weaknesses prior to manufacture.
By creating computer-based simulations, you can test how your product will function in the real world and more easily identify and troubleshoot any potential tolerance issues before you set to work.
5. Avoiding purchasing issues
Taking a strategic approach to your materials procurement will be a key factor in ensuring that you have consistent and reliable access to the high-quality parts that you need.
A common challenge in procurement is supplier management - from identifying the right supplier to monitoring their performance and ensuring a stable supply of products.
One option is to assign each team member responsibility for a specific commodity, be it sheet metal, machined parts etc. By focusing their attention on one area, they can hone their market knowledge and become more adept at predicting fluctuations in pricing and availability.
When the need arises to source new suppliers, your purchasing team will also be much better placed to act quickly and responsively in identifying suitable prospects and drawing up a shortlist of candidates.
Electro-mechanical assembly is arguably one of the most complex types of build within electronics manufacturing and it's one that is reliant on an exacting combination of skills, resources and manufacturing expertise.
With so many aspects to take into consideration, it’s not surprising that many OEMs are calling on the experience of contract electronics manufacturers to manage the entire process.
If you would like to discover more about how collaboration with an EMS partner can help you to improve the quality, consistency and delivery of your electro-mechanical assembly please download your free copy of the eBook below.
For more information on How to overcome 5 key challenges of electro-mechanical assembly talk to ESCATEC Mechatronics Ltd
Enquire Now
More Blogs
List your company on FindTheNeedle.