
Sign In
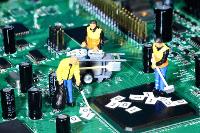
The IPC, which was founded in 1957 as the Institute for Printed Circuits, is the trade association responsible for standardising the assembly and production requirements of electronic equipment and assemblies.
Although the IPC suggests clear guidelines, agreeing on the cleanliness (or otherwise) of a PCB assembly can often be a subjective, and even contentious, subject within the electronics manufacturing industry.
So if you’ve chosen to outsource your assemblies, how do you decide what to specify to your EMS partner?
Defining 'clean' in PCB assembly
Firstly, it's probably worth defining what 'clean' actually means. I think we’re on safe ground to assume that lumps of unwanted debris - or "particulate matter" - mysterious white residues or corrosion of any kind are obviously not allowed.
Such things not only make the assembly look untidy, but can also damage the functionality or long term reliability of the product. So, most of the time, when we’re talking about "cleanliness", we're referring to flux residues.
It is possible, to an extent, to measure cleanliness. For example, once an assembly has been cleaned, you can measure the residues in the cleaning process cycles to ensure the desired maximum has been achieved. However, for many - perhaps most - electronics applications, it’s often more about the cosmetic finish or other process considerations.
As you might imagine, when we start to talk about solders, fluxes and cleaning agents there is quite a bit of chemistry going on. But for now, let's focus on the practical issues surrounding whether an assembly should be cleaned or not.
To clean or not to clean?
So, why clean in the first place?
Obviously, there are cosmetic considerations to keep in mind. If a "no clean" flux is used during the SMT process the assembly should look perfectly fine, as most of the flux gets burned off during the process.
However, if there is through-hole soldering afterwards - particularly hand soldering - it can show small areas of flux that make it all look a bit untidy, due to the extra flux that is typically applied and the reduction in both heat and time associated with hand soldering, compared to SMT ovens.
Perhaps most importantly, any residues mustn’t interfere with visual inspection. If there is anything left that is obscuring solder joints, for example, then it must be cleaned off, either by hand or by using one of the automated cleaning machines available.
If the product is to be tested using test probes, for example in-circuit test or flying probe, then flux can cause unreliability if the probes can’t access their test points on the PCB. This is usually fine if a pin-testable flux is used, but any excesses may need to be cleaned off.
Get the "Design guidelines for in-circuit testability" technical paper
If the assembly is to have a conformal coating, then all flux residues must be removed before application, so the PCBA will have to go through a cleaning process.
So are there any situations where you might choose not to clean?
Well, yes - as some fluxes are designed to be cleaned off, and some aren’t. Again, neatly side-stepping the chemistry here, if the flux is designed to stay on the PCB then trying to clean it off generally isn’t a good idea.
There is also an argument that the flux can provide a harmless protective layer over the solder joints and that removing it can expose the PCB finish to problems later.
Naturally too, there are cost implications. Cleaning is an additional process, so it’s going to have a value attached to it. And there is also the impact on the environment with additional water or chemical supplies needed, which then need to be disposed of correctly.
It’s also worth bearing in mind that certain types of components just simply can’t be cleaned, due to the risk of the cleaning agent getting inside the body of the device and causing damage.
If cleaning is required, it can also overly complicate the build process - for example, having to fit components after the main clean, then individually cleaning those components, or by adding extra drying stages.
Again, any extra processes are going to mean additional cost.
Which cleaning method is best?
So what are your options when it comes to cleaning?
Localised cleaning - which can be achieved with a brush and cleaning agent such as IPA. However, care must be taken to ensure the residue is cleaned off and not simply spread thinly across the assembly.
Automated solutions - there are some that use water (very similar to a dishwasher) or other cleaning agents, depending on the flux used. These cleaners tend to be relatively small in terms of physical footprint and the waste can usually be disposed of down existing on-site drains.
Ultrasonic cleaners - these tend to be larger in size, cost more and, due to the chemicals used, will require specialist handling of the waste that is produced to ensure it is disposed of safely. There are, however, certain components that can’t be cleaned using this equipment.
Many electronics manufacturing services (EMS) providers now standardise on a "no clean" process. If you are unsure, or you are weighing up the the pros and cons, then it's always best to take advice from your EMS partner.
They know what your requirements are - and they'll have the experience, equipment, skills and processes in place to meet your demands.
For more information on Is digitalisation the key to the future of electronics manufacturing? talk to ESCATEC Mechatronics Ltd
Enquire Now
More Blogs
List your company on FindTheNeedle.