
Sign In
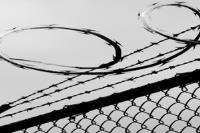
When things go wrong ‘poor communication’ is often cited as the reason. And quite often, justifiably so. Unfortunately, in a fast paced electronics manufacturing environment, the opportunity for things to go wrong is ever present and the results can be catastrophic for both the Original Equipment Manufacturer (OEM) and their Electronics Manufacturing Services (EMS) provider.
A common area for confusion, particularly during the early stages of an outsourcing partnership, relates to ‘boundaries', and agreeing who is responsible for what. If clear lines are not discussed and agreed between you and your EMS provider it can be easy to fall into an assumption trap and we all know what happens then!
In this blog post we look at 4 areas where communication can often fall down leading to confusion, frustration and worst case an assembled product which no longer meets the needs of your market.
Some of the common areas an OEM may ask for support from their EMS partner include:
Design
Supply chain management
Assembly
Test
Let’s now dig a little deeper into each one and look at where some of the communication issues occur and what can be done to overcome these.
Design
Historically, ‘front end’ product design has been left to the OEM to manage and control. Put simply, the OEM took responsibility for the design of the product and agreeing the specification of components listed on the Bill of Materials (BoM). The EMS provider would then procure material against this BoM, assemble the unit to the drawings provided by the OEM and if required, test the product against a defined set of instructions. In an attempt to offer increased value to their customers, a number of EMS companies now offer product design as a service. There are pros and cons to outsourcing the design of your product and much of course depends on your strategy.
Download the 'Outsourcing Product Design' eBook to understand which strategy is best for you
So, the first thing to agree is who is actually responsible for the design (and material specification) of your product? If, as an OEM, you don’t plan to relinquish control in this area then you remain responsible for maintaining your BoM, approved vendors list (AVL), drawings and test specifications. Your EMS provider will continue to work to your BoM but will need you to formally approve any component changes they may suggest due to obsolescence or extended lead-time issues for example. As the design authority, you understand the product inside out and the tolerances it is expected to work at whereas your EMS provider may not be privy to such information.
Very crudely (and oversimplifying the entire process greatly), the EMS provider is responsible for buying the electronic components you specify, fitting these to the correct locations on the printed circuit board (PCB) and then assembling the unit to the instructions or drawings you have provided. During the New Product Introduction (NPI) process the assembly partner may provide Design for Manufacturing (DfM) support or advice but again, it’s down to you as the design authority to verify and formally approve any suggestions they make.
If you have decided to outsource the design of your product then some of this responsibility will naturally shift back to the EMS Company. In this scenario it’s important you are clear on how the design process will be managed by the assembly provider. Some EMS providers have their own in-house team of design experts whereas others will work with a third party design house or even subcontract the design work out to an independent contractor. All of these approaches can of course achieve the desired result but it’s worthwhile probing your supplier on exactly who will be taking ownership for design so you aren’t left assuming the work is being carried out internally by them when in fact it’s being managed by a third party you are not familiar with.
Supply chain management
Typically the material element of any product makes up the majority of the unit cost and with lead-times ever changing, this area can be notoriously difficult to manage. Having a robust supply chain in place is therefore critical to any outsourcing partnership. But how much control are you planning to hand over to your assembly partner? As an OEM you might prefer to free issue material to your chosen partner or manage key suppliers, providing of course they are happy with this arrangement. Alternatively you might be keen to let the EMS provider manage the whole supply chain on your behalf so you are free to focus on core activities within the business.
Whichever route you chose to go down you need to agree upfront where responsibility lies. If there are any areas that ‘overlap’ these should be documented early on as to how they will be managed. For example, let’s say you have decided to relinquish full control of the supply chain to your EMS provider. This makes a great deal of sense and many OEMs choose to go this way. But, if you have developed strong relationships with key suppliers over many years you might find it difficult to take a step back. This can be particularly tough if the supplier starts to under perform when the EMS company takes over and it can be tempting to jump in and get in touch with your previous contact, demanding to know why a price has gone up or a lead-time has gone out etc.
But you shouldn’t be doing that anymore.
It’s not your responsibility.
You handed it over.
Of course, you need to understand what the assembly provider is doing about the issue but undermining them by jumping back in or going direct to the supplier to negotiate pricing for example after you have handed over responsibility can lead to unnecessary confusion, frustration and delays for everyone involved.
If you plan to free issue material to your EMS partner then you will of course still need to continue to develop the supplier relationship, negotiate pricing, manage lead-time fluctuations and deal with any quality issues that may arise. The EMS provider will schedule the build of your product around the free issue material dates you provide and any change to these dates could lead to a production slot being missed or pushed out. You therefore have a responsibility to the EMS company to keep them regularly updated on when the material you are procuring is arriving and if there are delays or issues you need to notify them straight away so they can amend their production schedule.
Assembly
When it comes to the physical assembly of your product the boundaries are usually very clear – responsibility sits with the EMS provider. Issues can occur during the build process however if changes to the design are requested. Although never ideal, design changes relating to products going through work in progress are a fact of life. Providing you communicate these changes formally, replacement parts are readily available, and the EMS provider has the capability, there should be no reason why they can’t manage these changes for you.
But, you will need to tell them.
This may sound obvious but it’s an area that is often overlooked. Last minute changes to BoMs, drawings and test specifications can all take place while a product is in build but unfortunately they don’t always get sent over to the EMS provider in time. The result? Assembled units that have been built ‘correctly’ but can’t be sold into the market without costly rework and further delays.
As well as communicating any design changes you need making during a build you will also need to agree who is responsible for updating the build documentation. The EMS provider will update their own internal copies and should have a robust Engineering Change Notice (ECN) process in place. But they are not responsible for amending and controlling your own drawings and system, unless of course there has been a commercial arrangement to do so.
Test
Confusion can occur quickly if the OEM and EMS provider do not agree upfront on what test strategy is the most appropriate for the product. A discussion around the cost of carrying out this work and how any potential test failures should be managed is also needed. As mentioned before, unless agreed upfront an EMS provider is typically responsible for fitting the right parts in the right place and eliminating manufacturing defects. Whether or not the product then operates correctly out in the field is another matter. If it doesn’t, your customer is going to be the first to find out which could be bad news for your reputation. So, it makes sense to have your EMS provider carry out some form of test to give you peace of mind but how far your test strategy goes will depend on a variety of factors including the end application, complexity, how much you’re prepared to invest in a test strategy and the expectations of your market.
Once you have worked with your partner to determine the most appropriate strategy you will then need to agree how potential test failures are managed. Clarity of who is responsible for what here is vital. If ambiguous, or left to assumption you could find yourself left with a pile of PCBAs or finished units that don’t pass test and are shipped back to you to fault find. You need to be realistic with the time spent trying to investigate and repair test failures. Depending on the complexity of the product it can be a time consuming task so how long is reasonable for the EMS provider to spend investigating failures? When does the unit become beyond economical repair? These questions and more need thinking through.
There’s a lot to think about when outsourcing to an EMS provider for the very first time. And even if you have outsourced before but are now working with a new supplier, you will be embarking on a new relationship with new ways of thinking and communicating.
As with any strong relationship being open, honest and transparent with your assembly partner will help to avoid unnecessary confusion. And setting clear boundaries and agreeing the areas of responsibility between you early on makes all the difference between a long term rewarding partnership and one that is filled with regret and frustration.
For more information on Setting clear boundaries with your EMS provider talk to ESCATEC Mechatronics Ltd
Enquire Now
More Blogs
List your company on FindTheNeedle.