
Sign In
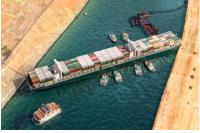
When the mega-sized container ship the Even Givshutterstock_1945572919en became stuck in the Suez Canal back in March 2021, one of the world’s most important commercial arteries began to clog. The effect on the global economy was dramatic and, it seems, a shock to many. What does it mean for the future of supply chain management that we remain so unthinkingly reliant on a narrow, watery gap between continents?
The Suez Canal - a global, commercial artery
The Suez Canal connects the Mediterranean and the Red Sea, providing the shortest sea link between Asia and Europe. It is 93 kms long, 43 meters deep, and at its narrowest point is just 300 meters wide.
The canal slashes journey time for goods moving both East and West. It avoids the treacherous seas around the Southern tip of Africa, cutting the potential for delays, shipwrecks and loss of cargo. It has revolutionised trading routes and made new commercial relationships between continents possible. And it still does.
In 2019 the Suez canal carried goods to the value of $149 billion between Europe and Asia. That's 15% of the world's shipped goods passing through every day.
The effect on supply chains
Even so, at the beginning of the Ever Given drama most people barely understood the huge range of goods that used this narrow passage every year.
Here's a random list of just some of the goods which are transported via the canal on a daily basis:
Animals
Barbecues
Bathroom suites
Bi-fold patio doors
Cars
Electronic components
Medical supplies
Oil
Sand (imported from Denmark to Dubai)
Semiconductors
Toy animals
And the list of vital and (not so vital) goods that pass through this commercial crossroads goes on and on. It's a huge range of materials, components and finished products that countless companies depend upon, while sometimes unaware that they are reliant on the Suez canal at all.
But as shipping backed up and the days of the blockage multiplied, the cost to companies and the world economy became evident. Companies saw supply chains seize up and consumers began to notice delays on orders and gaps in shelves. Meanwhile, industry and government began anxiously totting up the cost. In the end, Lloyds reported losses from the 6 days of the crisis to the tune of:
$9.6 billion in global trade
Which amounted to
$6.7 million of trade lost for every minute the canal was out of action
Since then, electronics manufacturers have seen daily bulletins pour in across April and May, reporting the continued consequences of the blockage for commerce across the world:
Carriers announcing void/blank sailings to/from Asia
Carriers imposing new surcharges or increasing current ones
Equipment shortages in late May as the impacted vessels coming in from Asia are delayed getting back out to Asia
Heavy port congestion in USA, particularly the West Coast is impacting equipment availability back in Asia
USA Westbound suffering capacity shortage.
A short history of container shipping
Container ships have long been the silent lifeblood of a globalised economy, but it took the blockage of a commercial artery to demonstrate their singular commercial weakness.
The world's first container ship was built and launched in 1956. It carried just 58 rectangular, metal storage boxes, but it sparked a revolution.
“The remarkable thing about the story of the shipping container is that it is such a simple idea that almost anyone could have had it – anyone who has ever tidied up children’s toys, for instance. The idea is that stuff is more manageable if you shove it into a box. That’s it.” John Lanchester, LRB
Containers are an extraordinary innovation. They send vast quantities of diverse goods around the world with incredible efficiency. They can be stacked, stored and moved around like children’s building blocks, shifted rapidly from lorry to ship, and ship to lorry through amazing feats of logistics and algorithmic automation.
Container shipping shapes the world economy
The simple innovation of container transport has delivered mind-boggling economies of scale. In fact, some argue it's all but removed the cost of shipping from the manufacturing equation.
Now, as Mark Levinson points out in his book 'The Box', the vast capacity of container ships, the reliability of their movements (together with the minimum human labour they take to load and unload), has 'abolished geography and location as a consideration for much of the manufacturing industry.'
'Megaships' have increased container capacity by 400x
Indeed, the latest megaships have capacities far exceeding anything ever seen before. These beasts can carry as many 24,000 containers in one voyage with each one big enough to contain two cars, or two aisles of groceries in a typical supermarket.
This may be improving efficiency for shipping magnets, but for some, this is practically the definition of putting all your eggs in one basket.
The drawbacks of the megaship solution
One false move and havoc ensues. One misjudgment in navigation on the narrowest part of the Suez Canal, and the whole world economy has felt the consequences.
Our reliance on particular regions for vital components, as well as fewer and larger vessels to get us the right goods at the right price has made us uniquely vulnerable to shocks to the system like the Suez blockage and Covid-19.
JIT strategies which often rely on predictable timetables of import and export over vast distances have been heavily challenged by recent freak conditions. But these freak conditions may well become 'the new normal'. International pandemics are likely to become more frequent and intense in the future, while shipping accidents may increase as the size of the ships themselves becomes more unmanageable.
Taken together, Covid and the Suez blockage have been a perfect storm of pressures on many supply chains. They have blown up already present component shortages, pushing up prices further and slowing down production in countless industries. Together they have scuppered business models reliant on the predicatable costs and availability of goods.
What can we do?
Coming out of the Ever Given crisis, the advice is to manage supply chain risk more effectively.
Map supply chains - understand risks and vulnerabilities. Work with your suppliers to ensure you know where everything is sourced so that there can be no nasty surprises in the future.
Create contingency plans - developing plans based on different scenarios, both optimistic and ‘worst case’.
Boost supplier flexibility - working with existing suppliers to create a continuity plan and identifying alternative suppliers to diversify and protect against shortages
Manage demand volatility - creating inventory reserves and prioritising high-value products
Explore technology to ensure better visibility - more agility and even more predictive modelling to alert us to issues and change plans on the fly. Real-time, fully integrated and digitised supply chains are needed to reduce the impact of disruptive events as they occur. With AI they can improve our chances of preventing them from happening in the first place.
Value Engineering for long-term sustainability?
But are there more radical solutions that can protect OEMs from risk in an increasingly volatile world?
Can we localise our supply chains?
Can we create more durable designs to beat component obsolescence and disposability culture?
Can we shift to more servitisation in our business models?
Are these the sustainable cost and risk reduction strategies that could yet offset reliance on volatile international markets and supply chains?
Re-engineering products to take into account these potential innovations is a daunting challenge. But with formal techniques like value engineering encouraging multi-discipline end-to-end analysis of design, sourcing, manufacture, and distribution there are ways we can make this kind of creative thinking a routine part of the way we do things in the future.
Global container shipping and maritime innovation like the Suez Canal continue to add incredible value to the world economy. Clearly, our reliance on them is not set to end any time soon, if ever. But better risk management is definitely required if we don't want a repeat of the Ever Given drama. And the routine exploration of more sustainable and value-driven solutions for our customers could well mitigate our long-term reliance on a narrow, watery gap between continents.
For more information on The Ever Given & the future of supply chain management talk to ESCATEC Mechatronics Ltd
Enquire Now
More Blogs
List your company on FindTheNeedle.