
Sign In
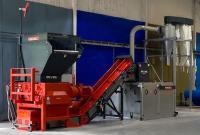
Plastipack Limited, a UK manufacturer of cover materials for swimming pools and water storage systems, first contacted Fercell looking to upgrade and expand the capacity of their existing granulating system. Their objective was to improve the efficiency and pace at which they were able to repurpose manufacturing waste into plastic granules for reuse within the production process.
To determine the correct solution, initial discussions focused on the specific type of materials to be processed, the volumes and the production output the client was looking for.
With test facilities onsite, Fercell were able to process a sample of the waste plastic material. Highlighting the different stages of the recycling process, the material was initially shredded. The shredded output was then transported via conveyor to a granulator, where the material was processed into <6mm granules.
The System
The two-stage shredding recycling system consists of a WEIMA ZMK40 four-shaft shredder, outfeed conveyor, WEIMA WNZ 310-800 granulator and fully demountable acoustic box. For the air-handling solution the system included a high-pressure transport fan, heavy-duty transport ducting and filtered cyclonic separation, above a bulk-bag loading system.
Shredding & Granulating
The WEIMA ZMK40 four-shaft industrial shredder is designed to shred bulky materials, making it ideal for plastic pool covers.
When it comes to choosing a shredder, it is important to consider a number of factors including; material being processed, volumes of material and processed outcome of material.
Ideal for a two-stage shredding system, the ZMK40 shreds the plastic, the WNZ granulator then creates granules as small as 6 mm.
With a rotational speed of around 25rpm the noise level is restricted to approximately 76dB. Plastic scraps are fed into the four-shaft cutting chamber from the hopper, where it is trapped by the high-torque teeth of the cutting discs and shredded.
The design of the hopper can be modified, to suit the customer, with a safety cage, special infeed rollers and convex viewing mirror. The shredder also features a quick change screen mechanism. The quick change screen will benefit Plastipack Limited with a way to swiftly and easily clean the system, allowing the type of material processed through the system to be changed in a timely manner.
Shredded output is fed onto a conveyor to travel along to the WNZ granulator. The permanent drum magnet will ensure any tramp metal is removed from the processed output stream.
The WNZ granulator can granulate the material at a throughput of up to 2,500 kg per hour. The plastic granules are collected in a bulk-bag station.
Following the connection of the services, one of Fercell’s factory trained engineers returned to site where they completed the cold/hot testing, plant commissioning and operator training.
The recycling system installed will allow Plastipack Limited to turn bulky plastic scrap and spoils into plastic granules that can be used again for manufacturing.
Contact FERCELL to see how we can help you realise improved profitability through optimised processes with the latest technology in size-reduction and separation systems.
For more information on Got It Covered! talk to Fercell Engineering Ltd
Enquire Now
More related to Got It Covered!
List your company on FindTheNeedle.