
Sign In
A Chat with Dover Fueling Solutions
21-03-2023
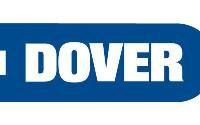
Flowstore has been working with Dover Fueling Solutions for 8 years, in the majority supplying raw stock so they can self-design and build storage solutions onsite.
When the decision came to streamline multiple production lines into one main production line, Flowstore was asked to help with the bulk manufacture. This was due to scale – there were 279 racks required, time constraints and the capacity available at the new Flowstore factory in Uxbridge.
The project was phased into 3 sections of priority to meet the required go live date of the new production line, this allowed us to focus our attention on where and when, which solutions were required first.
Regular communication between both companies throughout the project was the key to hitting the required dates and making this project a success.
We asked the Dover FS team for some feedback, and this is what they said.
Who are you and what do you?
We are Dover Fueling Solutions and we are market leaders in the manufacture of vehicle fuel dispensers for forecourts.
What was the challenge you were facing?
The challenge was to improve our material flow, material presentation across our assembly lines and ultimately increase efficiencies.
What was the problem you wanted to solve?
It wasn’t necessarily a problem, but an opportunity to make a step change in the capability and efficiency of our assembly processes.
What prompted you to consider this product?
Past experience of using Flowstore products and the flexibility it gives you to make changes or alterations to the application, whether that’s a fixed structure, a moving piece or a storage solution.
Did you find the process of working with Flowstore on designs straightforward?
Yes, Flowstore provided expertise on what could and could not be done, and also provided ideas about how to achieve the desired result via different design concepts.
Why did you decide to use our product?
It fitted with our application of requirement.
How easy was it to work with the Flowstore team
Yes, extremely easy. Site visits and conference video calls were routinely set up to provide any support as requested. Updates on orders and delivery dates were kept up-to-date and communicated.
What features do you like most?
The aesthetics of being able to have material storage, delivery methods and stillages all being consistent makes a professional working environment.
Can you name three other benefits?
The varied design of fixed assets, trollies being able to be moved in 360° axes, and material being able to be presented using roller tracks or roller tables, or guidance systems are all attractive qualities.
What results have you seen since the implementation?
Has aided the factory’s efficiencies and provided a consistent professional look to the shop floor.
What is customer service like? / What are the people like to work with?
No negatives here. Response times were quick and the offer of help and support always given.
Would you recommend the product? If so, why?
Yes, its design allows for flexibility and the quality of the product is very high.
For more information on A Chat with Dover Fueling Solutions talk to Flowstore Systems Ltd
Enquire Now
List your company on FindTheNeedle.