
Sign In
Automation
11-04-2013
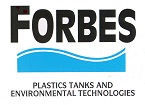
Automation of composite GRP tank production was introduced in the early 80’s with automatic hoop chop winding processes imported from the America. This process has been further developed by the company over the past twenty five years, this enabling Forbes to produce a number of large tank shells in a day. “The main limiting factor on output of large diameter tanks is the fitting out. This latest development will solve this problem” stated Kevin Johnston, Director in charge the Kelso factories. “This will allow our five winding mandrels to produce tanks simultaneously” Standard winding mandrels from 2 metres diameter to 4.1 metres in diameter, permits a large range of tank & tower shells to be produced within hours.
Managing Director, Melvyn Jupp, who is based at Head Office in Norfolk, stated “Over the past few years we have seen a huge growth in the demand for our quality products. Despite our highly competitive prices, where we were unable to win orders due to delivery times. Our sales team has been frustrated at times with our price being the most competitive but unable to meet the delivery requirements of the customer. This new facility has alleviated this delivery problem ”. There is a new metal fabrication shop, handling steel, stainless steel and aluminium. This “in house” facility has been a vital element within Forbes production since the 70’s. Forbes developed this ancillary facility to ensure only quality metal parts, such as access ladders, walkways, tank supporting structures and pipelines are fitted to their products when required.
For more information on Automation talk to Forbes Technologies Ltd
Enquire Now
List your company on FindTheNeedle.