
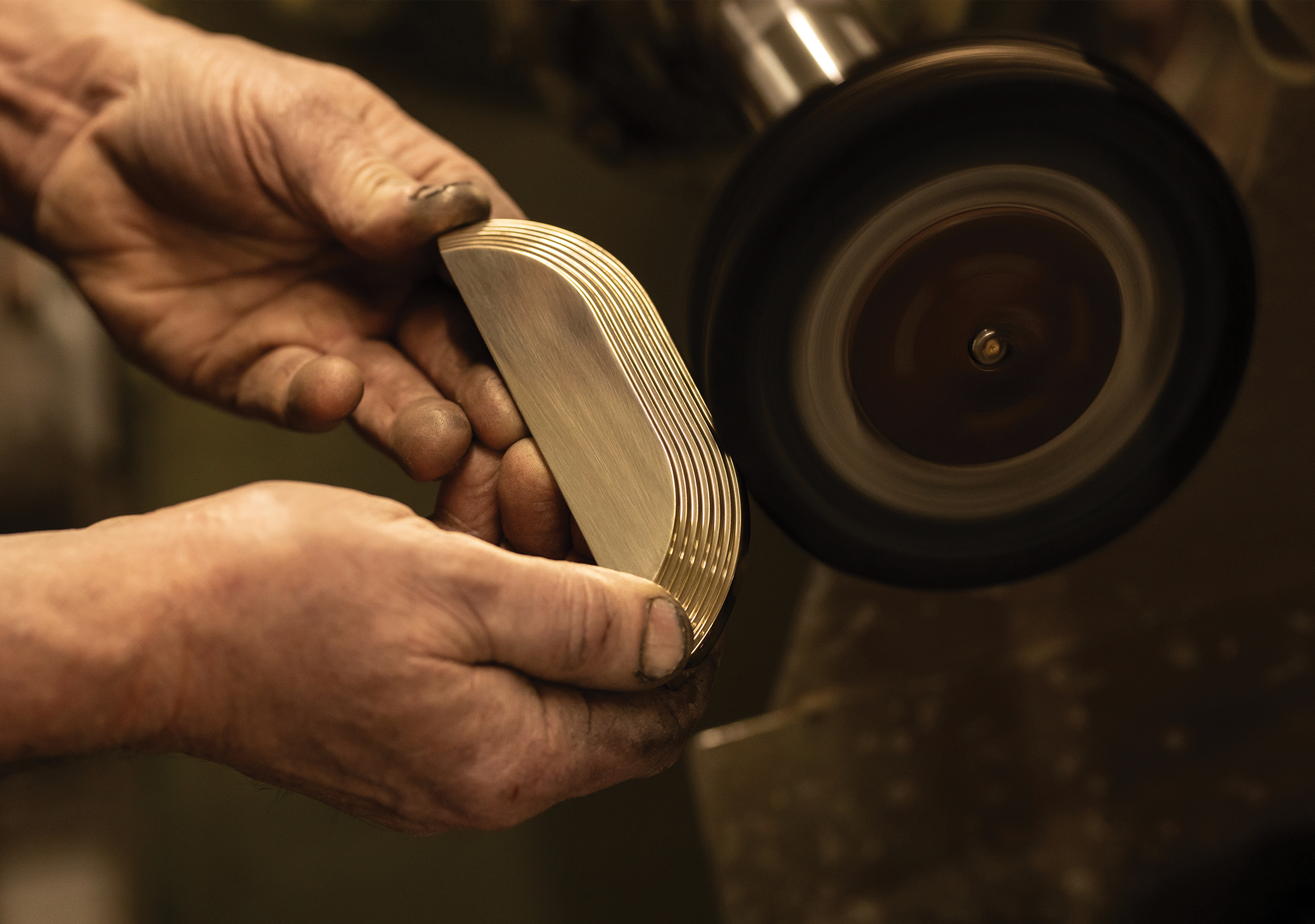
Company Background:
Since 1929, Armac Martin has been a pioneer in crafting design-led luxury brass hardware and accessories. Founded by Harold McGrail as a local brass foundry, the company has evolved into a fourth-generation family business, renowned globally for its commitment to exceptional design and craftsmanship. With a portfolio spanning brass hardware, shelf brackets, mirrors, and more, Armac Martin is celebrated for its heritage, innovation, and dedication to using the finest materials.
Challenges:
Armac Martin heavily relies on compressed air for CNC machining, but their existing system operated at full capacity constantly, leading to unnecessary energy expenditure.
Solution:
Collaborating with FPS Compressors and Compressed Air Systems UK - Birmingham, Armac Martin opted for a new system capable of variable compressed air supply, identified through data logging and energy audit exercises. This approach aligned with their sustainability goals by reducing power consumption.
Implementation:
The transition to the new compressed air system was seamless, with comprehensive training ensuring proficiency in operation.
Results:
Post-installation, Armac Martin achieved significant improvements in energy efficiency without disrupting manufacturing operations. Key highlights include:
- Reduced manufacturing energy consumption.
- Smooth operation without downtime.
- Compressed Air Systems UK - Birmingham are experts in first class compressed air installations.
CASE STUDY
Armac Martin's Sustainable
Manufacturing Transformation
The need for change.
Armac Martin has been driving to make their manufacturing operations more sustainable for a number of years as part of their sustainability strategy to achieve net zero by 2041, and after completing some energy monitoring, realized their compressed air supply was a significant energy drain.
Ambitious targets and objectives.
Armac Martin’s main objective is to reduce manufacturing energy consumption whilst utilizing a solution that will give them the capability to expand their compressed air usage on new equipment in the future when needed.
Focus on the things that matter most.
Reducing energy consumption was their primary driver and the solution recommended and adopted allows for variable compressed air. Armac Martin’s previous compressed air system ran at full capacity all of the time, whereas the solution they have can reduce the power needed by only supplying what is required.
Compressed air - a vital utility.
Compressed air is critical to their manufacturing operations. In particular high-quality air is an absolute must for modern CNC machining centres.
Identifying solutions by consulting the experts.
The system was monitored using state of the art instruments and analysed over the working weeks. The data logging itself was incredibly easy, and the data and recommended solution were very clearly explained to them.
Working with good partners.
Armac Martin’s experience with FPS Compressors and with their long-established distributor Compressed Air Systems UK in Birmingham was excellent; everyone spoken to was incredibly knowledgeable and recommended a great solution. The install was straightforward, and the training was great.
The proof is in the results.
Armac Martin's successful implementation of a sustainable compressed air solution not only underscores its commitment to environmental stewardship and operational excellence but also positions the company as a leader in sustainable manufacturing within the luxury interiors industry. By partnering with industry experts and embracing innovative technologies, Armac Martin has significantly reduced its carbon footprint. The transition to a variable compressed air supply system yielded a remarkable 46% reduction in compressor energy consumption, translating to an impressive £23,637.00 in annual savings. With a seamless installation process and comprehensive training, Armac Martin experienced uninterrupted operations. Remarkably, the ROI for this sustainable initiative was achieved in just 14 months, highlighting the tangible benefits of their dedication to environmental responsibility and operational efficiency.
For more information on FPS Case Study - Armac Martin's Sustainable Manufacturing Transformation talk to FPS Air Compressors Ltd