
Sign In
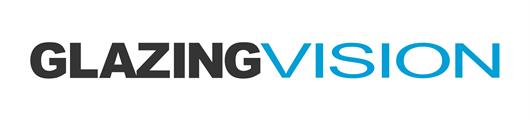
Spontaneous glass breakage is known to occur in toughened glass, due to the stabilising of nickel sulphide (NiS) present in the material. The risk of breakage is relatively low, but unpredictable – it could occur within weeks or years of manufacture, if at all. Heat soaking filters out about 95% of potential problem units. Toughened glass is heated to 290°C and held at that temperature, accelerating the process of any nickel sulphide inclusions reverting to their ‘beta state’ and causing failure.
UNDERSTANDING HEAT SOAK TESTING
Inevitably, heat soaking adds cost but improves product quality and consistency, reducing the use of potentially faulty glass in the manufacture of rooflight products.
The use of heat soak testing is not regulated, but reputable manufacturers are more likely to undertake it than not – especially for large structural rooflights or in walk-on applications. Glazing Vision, for example, heat soak test all of the toughened glass they produce as standard, to make sure customers get a reliable and trustworthy solution for their project.
Heat soak testing is not a guarantee that glass will remain failure-free. The reality is that whilst a Nickel Sulphide inclusion is a possible cause, it is the most unlikely one. In particular if the glass has been heat soak tested.
NICKEL SULPHIDE MAY NOT BE TO BLAME FOR UNEXPECTED GLASS FAILURE
There is a problem in the industry with any unexplained glass breakage being too readily blamed on Nickel Sulphide inclusions. Nickel Sulphide has had a bad press over the years and it is very easy to blame this as the cause of an otherwise undiagnosed glass failure.
The risk of a spontaneous breakage in thermally toughened glass that has been heat soak tested in accordance with BS EN 14179-1 is 1 in 400 tonnes of glass.
Based on a typical size pane of glass in a double-glazed unit this equates to a risk of 0.015% or approximately 1 in 7,000 sealed units or 1 in 14,000 panes of glass.
Other much more likely causes of glass failure are impact, other inclusions such as particles of refractory brick, undissolved silica or the chemical element silicone, surface scratches or damage from such as weld spatter or grinding dust. The surface damage can occur at any time during transport, site handling, storage or after installation.
Only Nickel Sulphide inclusions can cause spontaneous failure without any other influence. When the inclusion is not Nickel Sulphide or there has been surface damage to the glass, the toughened glass is weakened and therefore may fail when additional factors come into play to over stress the glass. This could be because the pane is oversize for the thickness of glass supplied or it has been overloaded by wind, snow or maintenance loads, over and above the design loads or it could be additional stress induced in the glass through having insufficient support by the framing system or structure or through poor installation or handling.
LOOK OUT FOR A BUTTERFLY PATTERN
All toughened glass, when broken, will display a typical ‘butterfly’ pattern at the source of the break regardless of the cause, including impact. So, looking for the butterfly pattern in the broken glass is useful to identify the location of the cause, it does not tell us the root cause. The only way to do that is to preserve the pieces of glass around this area and have them analysed under an electron microscope where surface damage or inclusions will be able to be identified.
For more information about reducing the risk of spontaneous breakage, download our guide to specifying glass in rooflights whitepaper.
For more information on Reducing the risk of spontaneous glass breakage talk to Glazing Vision Ltd
Enquire Now
List your company on FindTheNeedle.