
Sign In
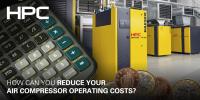
As energy costs continue to rise, it’s time to act, to mitigate the economic impact on your business. The compressed air system is an essential utility to many companies, and can be one of the most expensive. So, here are six steps your business can take to reduce your compressed air operating costs, now.
1. Check your compressed air usage
Potential savings can be identified by simply observing how and where compressed air is currently being used. Is it being used inappropriately or unnecessarily? For example, is a nozzle or gun being used to clean a workshop? Determine whether your compressed air supply is being used for tasks which could be performed more cost-effectively without compressed air.
Also review the existing and future demand for compressed air. Any changes to shift and production patterns will impact the demand for compressed air. By measuring your system’s load profile, it is possible to identify the compressed air system performance and where efficiencies can be made.
2. Identify and measure the compressed air distribution
Leaks can occur, whether it is in a high-tech compressed air system with the most advanced piping, or an ageing compressed air system. And when they do, they are expensive. Did you know, for example, that on average, 25% of the compressed air produced by a typical compressed air system can be lost to leaks? Based on a compressor running 24/7 and an electricity cost of 30 pence/kW/ hr, just one 2 mm hole could cost £4,052 per annum. The accumulative cost of multiple small leaks across your operation will quickly add up, particularly if the energy prices rise even further this winter.
Identifying, repairing and managing air leaks is one area where significant and long-term energy efficiencies and cost savings could be realised. Talk to an HPC Compressors expert about sustainable leak detection and management.
3. Review your compressed air storage
As part of reviewing existing and future demands for compressed air in your business, it is recommended to also consider the capacity of the compressed air storage, or the compressed air receiver(s). Changes in production and even the number of tools associated with a compressed air system, will change the efficiency of an existing compressed air receiver.
For instance, if production and the number of tools that are powered with a compressed air system both increase, the overall compressed air supply required will also increase, and the existing compressed air receiver many be too small to meet these requirements. The associated compressor will be running for longer than needed, increasing the associated energy costs, and wear and tear to the compressor. These both push up your overall operating costs
4. Consider the type of compressed air treatment used
Reviewing the type of compressed air treatment equipment being used in your operation, may highlight where energy efficiency and operating cost savings could be made. A number of different compressed air treatment technologies are available, and each possesses dramatically different energy efficiencies.
5. Review how the equipment is being maintained
Are you following the air compressor’s recommended maintenance schedule? Are you using Genuine parts and consumables? Are you choosing Certified Service Engineers to service and maintain your equipment?
Choosing to follow the prescribed maintenance schedule for a compressed air system will impact its overall efficiency and operating costs. This includes following the recommended maintenance schedule for the compressor itself, as well as the compressed air treatment equipment.
6. Consider the age and the efficiency of your equipment
As equipment ages and newer models become available, advancements in technology mean that significant efficiency gains may be possible by upgrading your equipment. Before making this investment, a comprehensive analysis of your existing compressed air system, taking current and future requirements into consideration, is essential.
What next?
Book a compressed air audit, with a qualified compressed air specialist. Ask for a comprehensive analysis of your compressed air system and operation, to optimise your compressed air system efficiency and reduce your compressed air associated operating costs.
A compressed air specialist will gather information about your compressed air system such as: production parameters, existing components, installation location and plans for the future.
The compressed air system is data logged over a fixed period of time and the data is downloaded and analysed, to generate precise consumption profiles. This highlights the real compressed air demand and identifies potential weak points in a compressed air system, as well as the all-important energy savings potential. This all lays the groundwork for an optimum compressed air station.
Based on the resulting air consumption profiles, by using a proprietary tool such as the KAESER Energy Saving System (KESS), a compressed air specialist can then help determine the best system solution for your individual air application.
How HPC Compressors can help
By assessing your compressed air system and implementing a range of no- and low-cost improvements, it is possible to reduce the associated energy costs. However, significant reductions in energy costs are often realised as a result of plant optimisation performed by first undergoing a comprehensive air audit. That is where a reduction of up to 30% or more in your energy costs is possible.
Speak to an HPC Authorised Distributor or contact HPC directly and we will show you how to increase cost savings and turn your operation greener. Go Yellow, Be Green, Save Money.
For more information on Six Steps To Reducing Your Compressed Air Operating Costs talk to HPC Compressed Air Systems
Enquire Now
More News
List your company on FindTheNeedle.