
ENSURING SAFETY AND EFFICIENCY: 5 WHEEL INSTALLATION PITFALLS TO DODGE IN COMMERCIAL VEHICLES
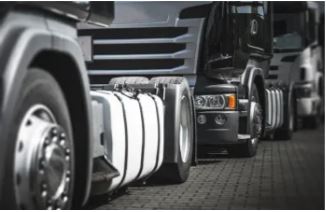
In the bustling realm of commercial fleets, where efficiency and safety intertwine, every detail matters, right down to the wheels beneath the vehicles. As fleet administrators, ensuring proper wheel installation isn’t just a routine task; it’s a pivotal aspect of maintaining operational integrity and safeguarding against potential hazards on the road. However, even the most experienced administrators can stumble upon common mistakes that compromise this crucial process. Let’s delve into these pitfalls and unveil the strategies to evade them seamlessly.
1. Incorrect Torque Application
Torque — the force that rotates an object around an axis — is the cornerstone of wheel installation. Yet, the temptation to tighten bolts or nuts beyond the recommended torque specifications is a prevalent oversight. Over-torquing can lead to stretched bolts, damaged threads, or even wheel misalignment, jeopardizing vehicle stability and compromising safety.
Solution: Embrace precision with torque wrenches calibrated to the manufacturer’s specifications. Opt for advanced torque equipment, such as HYTORC’s range of tools, engineered to deliver accurate torque application without the guesswork, ensuring optimal performance and longevity of the wheel components.
2. Not Following the Proper Torquing Sequence
Wheel nuts or bolts should be tightened in a specific sequence to distribute the load evenly across the wheel mounting surface. Disregarding this sequence can result in uneven pressure distribution, leading to wheel imbalance and potential loosening of fasteners over time.
Solution: Prioritize adherence to the recommended torquing sequence outlined by the vehicle manufacturer. Employ digital torque tools equipped with intelligent sequencing features, like those using HYTORC’s Connect App, to streamline the process and eliminate the guesswork, bolstering efficiency and accuracy in wheel installation.
3. Using Worn or Damaged Tools
In the fast-paced environment of fleet maintenance, tools endure considerable wear and tear over time. Using worn or damaged torque tools can compromise the accuracy of torque application, leading to inconsistencies in wheel tightening and increasing the risk of mechanical failures.
Solution: Invest in high-quality, durable torque equipment designed to withstand the rigors of commercial fleet maintenance. HYTORC’s robust lineup of tools, engineered with precision and durability in mind, ensures reliable performance, minimizing downtime, and optimizing operational efficiency.
4. Ignoring the Importance of Clean and Inspected Threads
Clean, well-maintained threads are essential for secure wheel fastening. Neglecting to clean and inspect the threads before installation can result in debris accumulation, thread damage, or improper engagement, compromising the integrity of the connection and posing safety hazards on the road.
Solution: Prioritize thread cleanliness and integrity as non-negotiable prerequisites for wheel installation. Employ thread cleaning tools and inspection procedures to ensure pristine thread surfaces, facilitating seamless fastener engagement and maximizing the reliability of the connection.
5. Neglecting Re-torque Procedures
Wheel fasteners can experience settling or relaxation shortly after initial installation, necessitating re-torque procedures to maintain optimal torque levels. Neglecting these procedures can lead to gradual loosening of fasteners, compromising wheel stability, and increasing the risk of accidents or mechanical failures.
Solution: Implement a systematic re-torque schedule in alignment with manufacturer recommendations and industry best practices. Leverage innovative torque verification technologies, such as HYTORC’s electric torque wrenches, to streamline re-torque procedures and ensure consistent torque levels, fortifying the integrity of wheel installations over time.
In Conclusion
When it comes to commercial fleet maintenance, meticulous attention to detail is paramount, especially when it comes to wheel installation. By steering clear of common pitfalls such as incorrect torque application, neglecting torquing sequences, using worn tools, overlooking thread cleanliness, and neglecting re-torque procedures, fleet administrators can uphold safety standards, enhance operational efficiency, and prolong the lifespan of wheel components.
For those seeking unparalleled precision, reliability, and efficiency in torque solutions, HYTORC stands as an industry leader, offering a comprehensive range of advanced torque tools and equipment tailored to the unique needs of commercial fleet maintenance. With HYTORC by your side, you can navigate the road to seamless wheel installations with confidence, ensuring the safety and reliability of your fleet operations for miles to come.
For more information on ENSURING SAFETY AND EFFICIENCY: 5 WHEEL INSTALLATION PITFALLS TO DODGE IN COMMERCIAL VEHICLES talk to HYTORC United Kingdom