
Maximising test load capacity
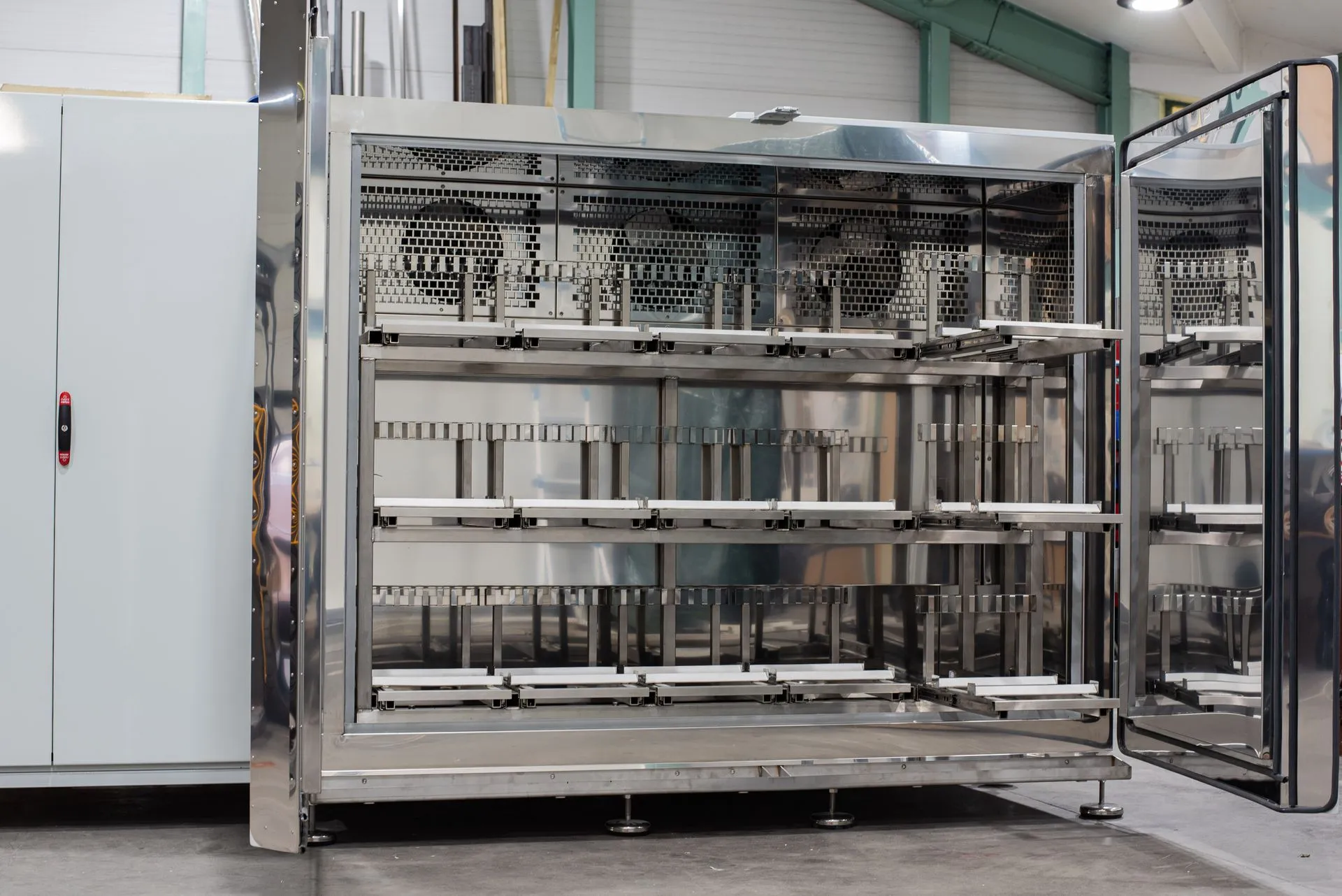
An issue faced by many customers is how to achieve the most test capacity without impacting on chamber performance. Putting the maximum test load in and still achieving even distribution and stability is a challenge when building bespoke equipment.
Airflow is key and having a good understanding of how a customer will load their product ensures the best results are achieved.
For one JTS customer who’s test cycle lasts several months, incorporating steady slow ramps and long dwells, humidity distribution is critical. For them the distribution accuracy is so paramount the chamber is regularly calibrated using the 9 point mapping system. One probe is placed in each corner just away for the chamber wall and one in the centre, the allowable tolerance in this scenario is 2% rh. During tests if the humidity fluctuates out of specification in any area of the chamber, the test is aborted.
Bespoke racking can help resolve distribution issues and the rack on this recent project was built to ensure good even air flow and ensure stability.
With a temperature range of -20°C to +80°C and a humidity range of 20 to 98% the chamber spends a lot of time testing at high temperature and high humidity, over 95%. These conditions are harsh, so the test frame was built of stainless steel and to enable easy product loading, sliding compartments were incorporated in the design.
Fully loaded this racking weighs around 600kg, so a reinforced chamber floor was essential.
Reliability of chambers that do long term testing is essential, down time causes testing backlogs and unwanted stress. Time spent understanding what is required of a chamber and how it is going to be used, ensures JTS get the design and build correct.
This in turn enables us to keep to our mission, to design and build robust, innovative solutions for our customers - something to rely on.
For more information on Maximising test load capacity talk to JTS Ltd (James Technical Services Ltd)