
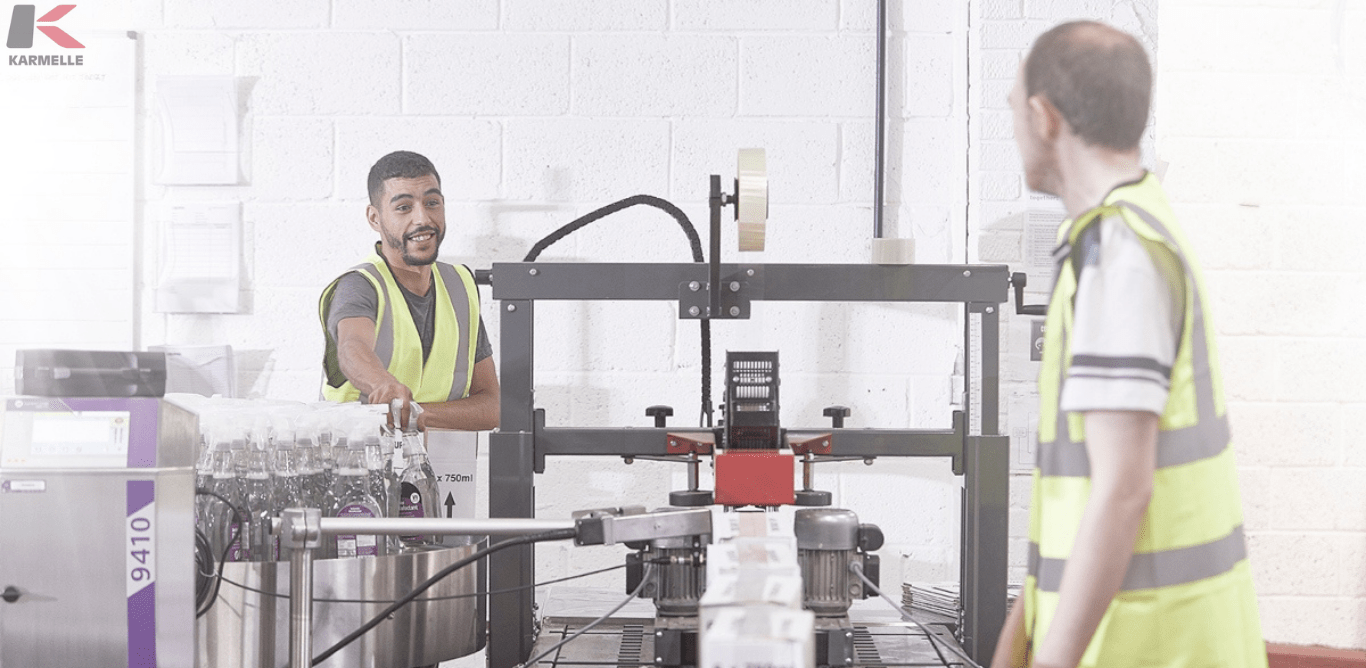
Filling machines are a vital component of many manufacturing and packaging operations, designed to accurately and efficiently fill containers with a range of products. However, these machines can pose significant health and safety risks if not operated correctly. Insufficient training and infrequent refresher training can result in accidents, injuries, and equipment damage, leading to costly downtime and reduced productivity. At Karmelle, we have been exploring the importance of regular training on filling line machinery, focusing on the risks of inadequate training and the advantages of receiving instruction from qualified personnel.
Filling, capping, and labelling machines can be complex, requiring specific procedures for safe and efficient operation. Without proper training, operators may be unaware of the machine’s capabilities, limitations, and potential hazards. This lack of knowledge can lead to various health and safety risks, such as:
- Accidents and injuries from improper machine operation or maintenance
- Equipment damage and expensive repairs
- Product contamination and spoilage
- Exposure to hazardous materials or chemicals
Additionally, inadequate training can result in non-compliance with regulatory standards, potentially leading to fines and reputational harm. At Karmelle, we recommend that all training on our machines be delivered by our skilled engineers or staff previously trained by our team.
Regular refresher training is essential to ensure operators maintain competence and confidence when using filling machines. As machines and processes evolve, new technologies and procedures are introduced, and staff may forget or become complacent with established practices. Refresher training helps to:
- Reinforce existing knowledge and skills
- Update operators on new procedures and technologies
- Identify and correct any bad habits or practices
- Ensure continued compliance with regulatory requirements
Refresher training should be conducted at regular intervals, such as:
- Every 6–12 months, or as recommended by the machine manufacturer
- When new team members join or there are changes in the production process
- After extended machine downtime or maintenance
- When new technologies or procedures are implemented
Allowing only trained staff to operate filling machines is crucial for both the machine’s longevity and the safety of operators and others in the workplace. Trained personnel are more likely to:
- Operate the machine correctly, reducing the risk of accidents and equipment damage
- Identify and report any issues or malfunctions with the machine
- Carry out routine maintenance and troubleshooting effectively
- Optimise the machine’s performance and efficiency
To ensure all operatives are adequately trained, consider the following best practices:
- Develop a comprehensive training programme that covers machine operation, maintenance, and troubleshooting
- Use a combination of theoretical and practical training methods
- Provide regular refresher training to reinforce existing skills and knowledge
- Keep training records and certificates up to date
- Encourage operators to ask questions and report concerns or issues
In conclusion, at Karmelle we believe that training and refresher training on filling, capping, and labelling machines is critical for ensuring safety, efficiency, and productivity. By providing regular training, you can minimise the risks associated with inadequate instruction, optimise machine performance, and ensure regulatory compliance. Always ensure that only trained staff operate filling machines, and provide refresher training at regular intervals to maintain knowledge and skills.
Each Karmelle machine is delivered with its own user manual. We strongly advise keeping a hard copy accessible for machine operators. Additional manuals can be purchased from our service team.
For more information on The Importance of Training: Ensuring Safety and Efficiency for Your Filling Line talk to Karmelle Ltd