
Sign In
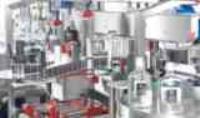
At Karmelle Ltd, we’re proud of our Yorkshire roots – and, over the years, we’ve been lucky enough to partner with some of the region’s top artisan producers. Today, our filling, capping and labelling equipment bottles everything from rapeseed oil to kefir.
Our latest award-winning Yorkshire partner is Raisthorpe Manor, for whom we recently designed, manufactured and installed a Monoblock gin filling system.
Raisthorpe Manor’s award-winning gin
North Yorkshire country estate Raisthorpe began producing homemade spirits in 2008, after an old family recipe for raspberry gin proved hugely popular with visitors to its hunting lodge.
Estate owners David and Julia Medford originally produced the liqueurs in their farmhouse kitchen – but, as demand grew, they realised that it was time to invest in packaging equipment.
The couple needed filling, capping and labelling machinery, capable of handling a range of bottle sizes (from 5cl to 35cl) and label-types. Production-space was limited, and they were keen to source a versatile system with a small footprint.
The solution:
Karmelle had just the machine; a Mini Monoblock, comprising integrated filling, capping and labelling equipment. Uniquely compact, it was ideal for Raisthorpe’s production environment, and would enable them to automate their packaging process without wasting valuable space. It would also, crucially, be able to handle a range of bottle, cap and label-types.
Raisthorpe’s Monoblock filling, capping and labelling system
The process:
Empty bottles are placed on a feed table, before being singled-out and automatically carried onto the filling line.
Bottles enter the volumetric rotary filler, where they are filled with spirits.
After filling, the bottles are indexed round to a vacuum suck-back station, where any excess liquid is drawn out. This ensures that levels are consistent.
Bottles then pass through to the R.O.P.P capping station, where they are capped.
Filled and capped bottles are carried to the labelling station, and front-and-back or partial-wrap labels applied.
Finally, filled, capped and labelled bottles are automatically transported to a packing station.
The Monoblock system was designed and manufactured in Karmelle’s West Yorkshire workshop, with the Raisthorpe team visiting for Factory Acceptance Trials ahead of installation.
The monoblock’s in-built filling station
The results:
Installed and commissioned in March 2019, Raisthorpe’s Mini Monoblock is currently running at speeds of up to 20 bottles per-minute (5cl bottles).
Julia Medford commented: “Before we invested in packaging machinery, we were bottling by hand. The Monoblock system has completely transformed the process, enabling us to improve efficiency and accuracy, up production rates and meet the growing demand for our products.”
Read more about Raisthorpe Manor and its products here.
For more information on Karmelle Case Study talk to Karmelle Ltd
Enquire Now
List your company on FindTheNeedle.