
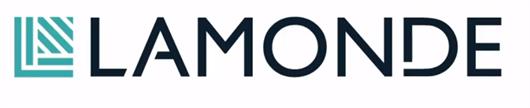
“We are very happy with the service from Lamonde and would recommend using this method of moving data. “ Welland Medical’s Story: We were looking for a method to move data from various production lines into our MySQL server. This would feed a front-end program and provide live OEE type data on large screens on the shop floor, but our machines have many different brands of PLCs fitted. We explored our options and received some quite expensive quotes. Duncan at Lamonde advised that we use Weintek’s cMT-SVR-100. We found this easy to use and can extract data from the majority of makes of PLCs for a very small cost. Duncan wrote the program for this and provided training on-site for our engineers. A front end was programmed by an external SQL server expert. The few problems we did suffer were very quickly resolved by Lamonde. The system is simple, inexpensive and is now up and running. We are very happy with the service from Lamonde and would recommend using this method of moving data. James Jeffery Senior Projects Engineer Welland Medical Limited Welland Medical is a British manufacturing company established in 1988. They are an innovator in stoma care, specialising in the design, development and manufacture of stoma care appliances and accessories, using the highest quality materials. Welland Medical have been a client of Lamonde Automation for nearly 20 years. “our machines have many different brands of PLCs fitted.” The Brief and Challenge: Since their recent move into new premises and upgrades to their network architecture and server, Welland Medical’s existing machine data capture system no longer functioned and the quote that they had obtained for a replacement/upgrade of this was prohibitively expensive. They needed a data capture system for their factory production machines to monitor and record their production KPIs (key performance indicators) and synchronise this to a database that could be queried to produce live data and historical operational and management reporting. Welland Medical’s installed factory production machines have a variety of brands of PLCs (programmable logic controllers) at their heart, all of which reside on their automation network, along with various HMI (human-machine interface) and other devices. It can be a challenge to gather meaningful production data from multiple brand devices. The Lamonde Automation Solution: Our solution was to install a Weintek cMT Server (cMT-SVR-100), a faceless HMI. The cost of the unit was a small, one-off hardware cost, plus installation and configuration by Lamonde, but no ongoing costs as no licence is required. Weintek cMT-SVR-100 Compared to a traditional approach to this kind of problem, which would require multiple OPC server licences to communicate with the installed PLCs and devices, the Weintek cMT Server was a cost-effective solution, costing a small percentage of the price for a single OPC server. The specific unit we recommended and installed was Weintek’s cMT-SVR-100. This provides all the interface and datalogging capability you’d reasonably expect of an HMI, but without taking up precious panel real-estate or providing an unnecessary expensive touch screen. Whilst primarily the cMT is acting as a data-concentrator/communication gateway, the HMI application has been developed to make it a useful shop-floor diagnostic tool accessible by Android/IOS devices using Wi-Fi, as well as via a PC running the Weintek cMT Viewer app. Using bit-triggered data sampling, each PLC presents a snapshot of the production data: product code, an ASCII string, and four 32bit registers providing current, real-time parts per hour, batch count and a downtime reason code, and a spare register for future use. “the Weintek cMT Server was a cost-effective solution” Captured data is written to an SD card installed in the cMT-SVR-100 in real-time on a rolling 31-day FiFo (first in first out) cycle and periodically synchronised to a MySQL Database residing on the Welland Medical server. Resilience is provided by the 31 days of storage on the SD card so, should there be a temporary issue with the server, the data will be available to resync once the server issue is resolved. Further integrity is provided by the front-end, developed by a third party. By synchronising the captured database with a second database, a further layer of data integrity is provided so any erroneous writes or table dropping calamity (it happens!) affects only a mirror of the real machine data. Business Benefits: All the data is displayed on monitors at the end of the production line and in the staff canteen, providing highly visible business-rich information, far more than Welland Medical used to have on their old system. Welland’s Data dashboard using captured machine data Future Developments for Welland Medical As with any control system, further development is likely to be organic. The first enhancements already in the pipeline include: Logging data from more machinesEmail alarm alerts MQTT (message queue telemetry transport) publishing alarm topics, as the cMT-SVR-100 has a built-in MQTT broker. MQTT is a lightweight machine-to-machine (M2M) “Industrial Internet of Things” (IIoT) protocol and is a de facto industry 4.0 protocol. Other potential applications of this solution: Any automated process, including a production line or conveyor beltPackaging and baling machinesWater treatmentOil refineryWind/water turbine generationBrewingFood productionPharmaceuticalsAutomotive manufacturing And the list goes on! Please get in touch if you would like to learn more about our cMT HMI solutions.
For more information on Case study: Welland Medical Machine Data Capture talk to Lamonde Automation Ltd