
Sign In
New Case Study - CitizenM Hotel
05-09-2019
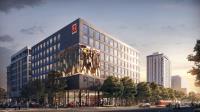
Location: South Lake Union, Seattle, Washington, USA
Product: Hollo-Bolt® by Lindapter®
Quantity: 10,600
Project Value: £44.6 million
Project Team: Mortenson Construction, Gensler, Arup and Polcom
Project Background
Modular buildings, which are manufactured off-site in sections before being assembled on-site, are gaining popularity as an affordable and sustainable solution. This design and delivery method has been adopted by Netherlands-based hotel operator citizenM, who have brought their steel-framed modular hotels to New York and Los Angeles.
Client Requirement
Polcom Group, specialist off-site modular manufacturers, were appointed to build 228 modular units for the hotel. They identified that they would need to modify their normal production and assembly process to meet US building practices and standards.
Due to time constraints the traditional method of connecting units together on-site by drilling and bolting was not chosen, whilst hot welding risked damaging the critical waterproof membrane that protects each module.
Design Solution
Special steel structural shear plates were designed and added to the steel enclosures of the modules during production so that they could be connected to each other with Lindapter Hollo-Bolts during on-site assembly.
Hollo-Bolt was specified for its high strength capacity and ability to be installed from one side of the Structural Hollow Section (SHS). To meet the required standards, manufacturing took place under the supervision of inspectors, including inspectors from the City of Seattle.
Each module was then wrapped in a protective air and water barrier, pressurised to keep windows in place and shipped on a private vessel from Europe, unloading at the Port of Everett in Seattle ready to be assembled.
Installation
Mortenson Construction were the appointed main contractor for the construction of this seven-storey, 264-room hotel. Each 18,144kg modular unit was lifted by crane and carefully stacked on top of each other.
Hexagonal head and countersunk Hollo-Bolts were then used to connect through the structural shear plates to the SHS of each module.
Installation was quick and easy. Each bolt was inserted into pre-drilled holes and tightened with a calibrated torque wrench to the recommended tightening torque to provide the necessary clamping force.
Result
Hollo-Bolts provided a weld free connection that was quick and easy to install without damaging the waterproof membranes. This allowed the client to improve their modular construction method which provided many advantages over traditional methods, including shorter constructions schedules, consistent quality control and reduced disruption on-site.
"It’s about 4 months faster to do modular versus conventional, what would typically take about 17 months on a more traditional hotel, can be done in about 13 months when building modular."
Mortenson Construction Project Manager Lauren Boedeker
Hollo-Bolt Benefits
- Fast and convenient installation from one side
- No specialist equipment required to install
- No hot work permits or area closures required
- Unique high clamping force design
For more information on New Case Study - CitizenM Hotel talk to Lindapter International
Enquire Now
List your company on FindTheNeedle.