
Sign In
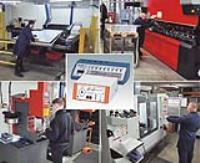
Metal electronic enclosures specialist METCASE has invested a six-figure sum in new hi-tech equipment to further enhance quality, accelerate production and drive innovation.
Three new state-of-the-art CNC punching, forming and milling machines are helping METCASE to create the next generation of standard and customised 19” rack cases, 19” mini-racks, desktop and portable instrument enclosures.
METCASE’s new high-performance Wiedemann punching machine features a built-in tapping tool that can punch holes and tap threads simultaneously. It is much faster than its predecessor and can handle much higher volumes – thanks to its large table which can accommodate 2.5m-long aluminium and steel sheets. It has 44 tool stations so it can punch complex enclosure parts faster and more efficiently.
The new Amada forming machine is the latest evolution in hydraulic-drive press brakes. Its multi-touchscreen interface controls the production of high-quality batches at low energy costs – with unrivalled process stability. Again, it is much faster than the machine it replaces, enabling METCASE to deliver larger orders more quickly.
METCASE’s new Haas milling machine features a 10-station automatic tool changer that enables faster production of enclosures with complex cut-outs. It is ideal for customising extrusion profiles and diecast parts, and for machining panel cut-outs such as recessed pockets or counterbores.
METCASE Marketing Director Robert Cox said: “This significant investment in new technology ensures we remain at the forefront in the design and manufacture of leading-edge metal enclosures for advanced electronics.
“Our customers can now order even higher quality metal enclosures, customised faster than ever – fully finished and ready for the installation of components.”
The new machines will enable METCASE to produce superior customised versions of its most complex models, such as its TECHNOMET instrument enclosures and TECHNOMET 19” mini-racks. Their modern, cohesive design and fine-tolerance engineering have redefined the genre – creating an elegant, contoured aesthetic traditionally associated more with moulded plastic enclosures.
All METCASE enclosures can be specified fully customised. Dealing with a single-source supplier “ensures quality, full accountability, faster delivery and reduced administration”. Services include bespoke sizes, custom front panels, CNC machining, fixings and inserts, painting/finishing and photo-quality digital printing of graphics, legends and logos.
For more information on METCASE’s New Production Technology Creates Superior Metal Electronic Enclosures talk to Metcase Enclosures
Enquire Now
More News
List your company on FindTheNeedle.