
Sign In
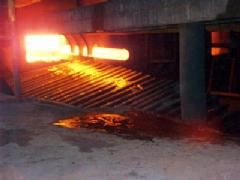
Flexibility and installation cost savings are hard to beat at
Steel Mill upgrade.
When Mittal Steel upgraded their Newcastle Works in South Africa, they chose a Maxiflex solution from Omniflex to provide the plant I/O and data acquisition to
optimise the monitoring and control of energy utilities on the plant.
Mittal Steel is the largest steelmaker in the world, with
annual shipments of 42.1 million tons and revenues of over $22 billion in 2004. Mittal Steel South Africa Limited is the dominant steel producer on the African continent, producing 7,1 million tonnes of liquid steel per annum.
Mittals Newcastle plant, is the countrys foremost supplier of steel profile products. This highly efficient and low cost operation was rated among the lowest billet cash-cost producer's in the world.
The plant employs 3400 staff. and produces 1.5 million tonnes of final product of which 57% is exported.
When Mittal Newcastle looked to invest in extensive upgrades to their plant wide utilities management information system, a major cost would be the cost of
specialised cabling, potential plant downtime during installation, and additional remote I/O. Consideration
also needed to be given to the harsh environment.
After reviewing a number of proposals, Mittal chose Omniflex to provide the complete Data Acquisition including the interface to the Bailey DCS.
The solution was based upon the Maxiflex Remote I/O system. This system consists of 1 Master Station and 13 Out Stations located around the entire plant many kilometres distant.
The Master Station consists of a Maxiflex gateway connected directly to a Bailey DCS communications port. This gateway interfaces to 13 separate Conet networks through network interface modules. Conet is the worlds most rugged LAN, allowing reliable industrial strength communications on existing plant wiring to 10km in a
full peer-to-peer configuration.
Capabilities for report by exception, dual redundancy and
multiple network segments to suit the plant topology are features of the Conet network. Each of the 13 Outstations
comprises of Analogue and Digital Input and Output Modules to read energy usage and regulate and
control consumption of utilities at each location under the
supervision of the Bailey DCS.
Andre de Jager, Senior Engineer Scada and DCS for the plant had this to say:
“Sizeable capital expenditure has been invested for the extensive refurbishment of the plant and to
introduce sophisticated information systems. This has
optimised operations and sustained global competitiveness at all levels. The Maxiflex solution
has been an integral part of the provisioning of data from the various mills and facilities around the plant.
We chose the Maxiflex solution because of its track record in acquiring data from around the plant and its effectiveness on existing plant cabling.
The system has proven itself in this harsh environment and the Maxiflex system provides a cost effectiveness that is hard to beat through its flexibility.”
For more information on Mittal Steel chooses Omniflex for DCS Front End talk to Omniflex UK Limited
Enquire Now
List your company on FindTheNeedle.