
Sign In
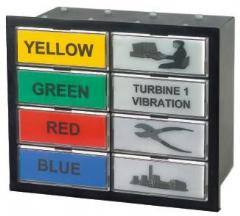
In the main control room of a multibillion rand petrochemical plant pulses the heart of a process with an explosive mixture of gases and liquids which, in the wrong conditions, has all the makings of an incredibly large bomb.
The operators in the main control room pace the panels with anticipation. The operators monitor the readings for any changes and immediately spring into action when a discrepancy is found. Fact or fiction?
Truth be told, while the licensed operators do walk the panels and do catch deviations displayed on instruments, screens of mimics and in process variables the primary system that warns operators of malfunctions and problems is the annunciator system.
What is an annunciator system?
An annunciator system comprises sensors connected to a computer or controller. When the parameter being monitored moves outside of the acceptable range an audible alarm sounds and a panel flashes to draw the operator's attention to the alarm. The operator then follows approved procedures to correct the abnormal condition and restore the plant to a normal status.
The purpose of the annunciator is to provide the plant operator with early warning of a problem, which allows time to take action before a situation degrades to the point where the process can no longer be controlled. Avoiding unnecessary challenges and trips is good for the plant's bottom line, as well as for safety.
Monitor-based systems
The annunciator brings together the results of the monitored parameters alerting abnormal conditions and indicating which parts have shut down. Dedicated annunciators have been converged into monitor-based systems such as control systems, supervisory system, data acquisition systems and shut down systems. All these systems suffer the same weakness - overload on the operator with too much to look at and handle.
The advent of PC-based systems has created information overload and this in turn has led to many accidents in plants where critical alarms have been missed. The alarm annunciator is not monitor-based and has dedicated panels representing various critical alarm conditions. When these illuminate the operator has procedures to follow to ensure corrective action or the plant will be shut down. The annunciator relies on visual and audible cues to attract attention and an alarm sequence to force operator interaction in returning the alarm status to normal status.
Critical alarms
The annunciator is most often used for critical alarm display and the trapping of alarm conditions, since many alarms are transient in nature and are difficult to diagnose after the fact. Critical alarms displayed on annunciators are consistent and easy for operators to recognise and deal with. They are also arranged in prominent locations within a control room so that they provide the best possible warning to the plant operators and offer the best performance in terms of plant safety.
Are annunciators still relevant?
In the computerised world of automation, the need for an effective interface between man and process remains quintessential to safe and efficient plant operation. The complexity of this interface has increased exponentially over the years as processes have become more sophisticated and the demands for quality, efficiency, safety and productivity have become more intense. Many technologies are exploited to achieve these ends. Computerised alarm lists have revolutionised abnormal event handling on the modern plant, although it has been proven time and again, that when the chips are down, a dedicated alarm display for critical alarms is an essential tool needed for timeous reaction to modern plant upsets. This reaction time is crucial to plant productivity where downtime is revenue lost and speed of response can even mean the difference between life and death.
The annunciator performs an important and complementary role to scada, DCS and emergency shutdown systems
For more information on Panel Mount Annunciator Crucial to Plant Safety & talk to Omniflex UK Limited
Enquire Now
List your company on FindTheNeedle.