
Sign In
Protecting hazardous areas from corrosion
24-02-2021
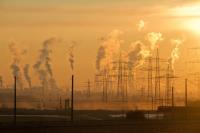
Omniflex certified to manufacture intrinsically safe systems for use in hazardous areas
Remote monitoring specialist Omniflex has gained IECEx certification to manufacture intrinsically safe electrical equipment for the global market, supplementing its existing hazardous area equipment approvals. Certification facilitated the delivery of an intrinsically safe cathodic protection (CP) system with remote monitoring and testing to help combat corrosion at NSW Port’s Bulk Liquid Berth 1 (BLB1) site in Sydney Harbour, where there is the potential for exposure to volatile, flammable substances.
In 2019, NSW Ports embarked on a two-year programme to rehabilitate concrete structures and combat corrosion levels at BLB1 using a CP system. This was a challenging endeavour because BLB1 plays an active role in loading and unloading hazardous liquids and gases, meaning any excess voltage or current could become an ignition source for a major explosion. To overcome this, the consultants engaged Omniflex, who assisted with designing an intrinsically safe, remotely monitored hybrid CP system that could protect critical infrastructure at the port from corrosion. The system allowed hybrid CP anodes to be charged during the impressed current phase and monitored during the galvanic phase, with loading and unloading of hazardous gases at the site continuing normally.
“Because this was the first project to use a hybrid CP system in a hazardous area on this scale anywhere in the world, some of the components required certification for the design to meet the necessary standards as an intrinsically safe certified system,” explained David Celine, managing director of Omniflex. “The system used a network of 35,000 hybrid anodes expressly for the purpose of creating current, which created a new use case that wasn’t covered in the existing documentation.”
The IECEx international standard governs the installation and use of electrical equipment in explosive atmospheres — all equipment located in hazardous areas must comply. However, getting approval can be complicated when working across different countries, as they each have their own interpretations of the testing and documentation required.
“Because the anodes were from a UK-based supplier, Omniflex’s technology is manufactured in South Africa and the project site is in Australia, navigating certifying bodies was challenging,” continued Celine. “Furthermore, IECEx certification requires all equipment made for use in the hazardous area to be manufactured at a facility that is itself certified as being IECEx compliant. This meant that Omniflex’s factory in Durban needed this approval too.
“Despite the hurdles, both Omniflex’s factory and the BLB1 system design was approved and certified as being intrinsically safe for use in areas classified as Zone 1 hazardous for gas group IIB. This enabled us to deliver the project as planned and put a system in place to protect structures at the port from corrosion for the next 50 years,” concluded Celine.
For more information on Protecting hazardous areas from corrosion talk to Omniflex UK Limited
Enquire Now
List your company on FindTheNeedle.