
Sign In
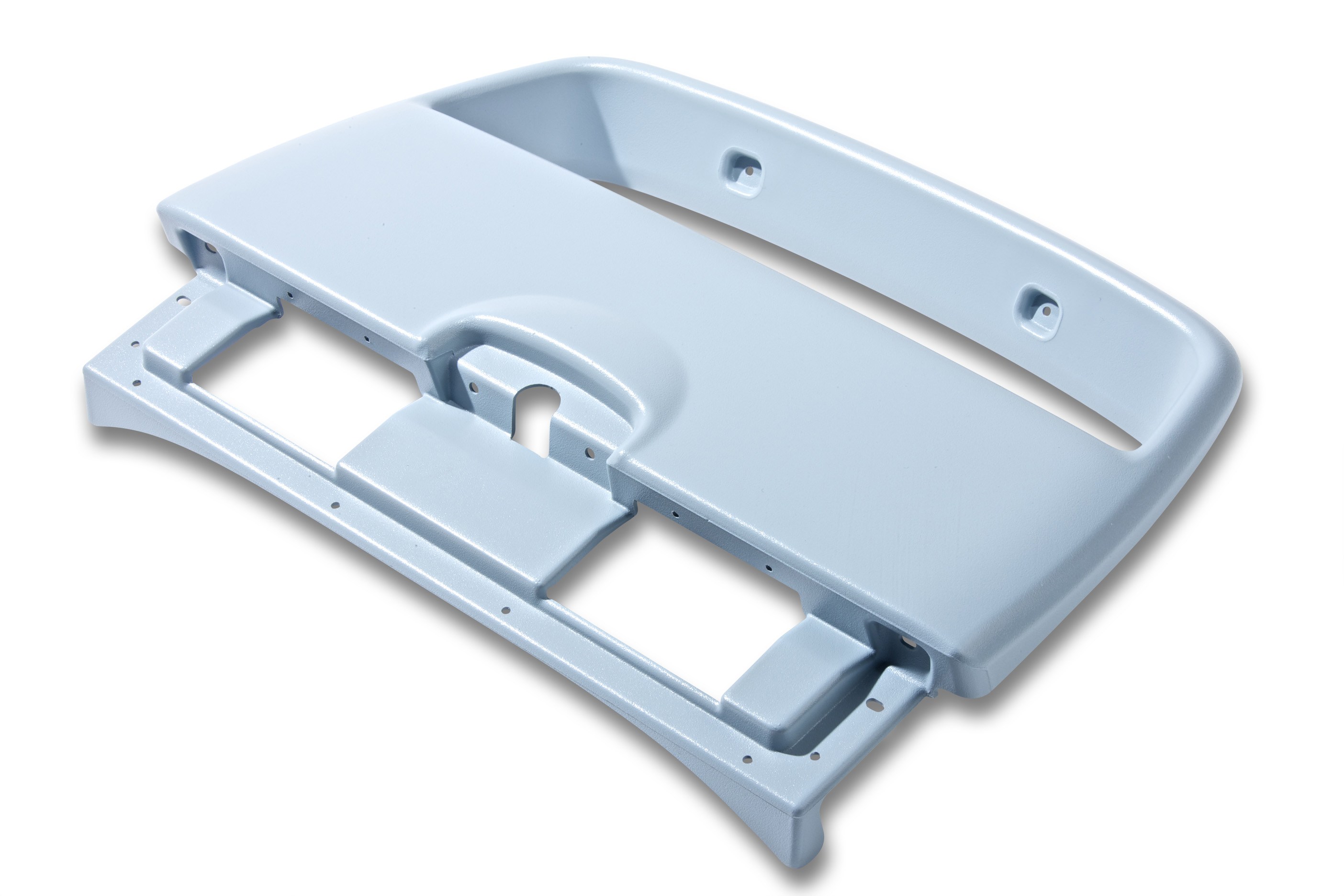
Plastic Pressure Forming Overview:
Plastic pressure forming is a versatile and economical technique that offers high-quality results akin to injection moulding while maintaining the benefits of low-cost tooling and shorter lead times. This method allows for greater accuracy, detail, and flexibility in product design, making it ideal for various applications.
Key benefits:
- High-Quality Image: Achieves an injection moulding-like finish with lower costs.
- Low-Cost Tooling: Significantly reduces the expenses associated with mould creation.
- Shorter Lead Times: Accelerates the product introduction process.
- Enhanced Detail: Allows for undercuts, grille work, crisp edges, and detailed surface decoration.
- Low Internal Stress: Results in parts with good physical properties and durability.
Manufacturing Flexibility:
- Rapid Product Introduction: Ideal for manufacturers dealing with accelerated product life cycles.
- Cost-Effective for Low to Medium Volumes: Particularly advantageous for short-run productions.
- Modification Flexibility: Easier and more cost-effective to modify compared to injection moulding.
Design and Simulation:
- Early Customer Involvement: Our experienced design team collaborates with customers from the outset to eliminate preconceived process limitations.
- Advanced Thermoforming Simulation: Utilizes advanced software to finalize basic design and material options.
- Detailed Considerations: Recommendations on fixing devices and cosmetic features to improve appearance, function, and reduce costs.
Production Capabilities:
- Moulding Dimensions: Capable of producing mouldings up to 2200mm x 1500mm x 800mm.
- Material Thickness: Handles materials up to 8mm thick. Material Options:
- A wide range of engineering thermoplastics, including:
- Polycarbonates
- ABS
- Polypropylene
- HDPE
- Acrylics
- PETS
- Fire-rated materials to British Standards
- Precision Finishing: All parts are finish machined to a high degree of accuracy.
- Additional Features: Optional EMI/RFI shielding for protection if required.
- Uniform Heating and Holes: Ensures effective vacuum pull, especially in less resilient sheet areas.
- Finalises basic design and material options.
- Detailed Considerations: Recommendations to improve appearance, function, and reduce costs.
Applications and Products:
- Component Parts: Suitable for creating various component parts with detailed and accurate designs.
- Protective Packaging
- Transit Trays
- Point of Sale Displays
- Custom and Specialized Products
For more information on how our plastic pressure forming services can meet your needs, contact us at Plastics By Design. Our team is ready to assist with your specific requirements and provide high-quality, cost-effective solutions.
Contact Information: Phone: 01380 827022
Email: info@vacforming.uk.com
By leveraging our expertise and advanced capabilities, we ensure optimal results for a wide range of vacuum and pressure-formed component parts.
For more information on Pressure Formed Component Parts at Plastics By Design Ltd talk to Plastics By Design Ltd
Enquire Now
List your company on FindTheNeedle.