
Sign In
5 Steps for Controlling Workplace Noise
15-10-2021
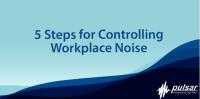
Noise-Induced Hearing Loss (NIHL) is one of the most prevalent, but often ignored, risks in the workplace. Throughout all industries, industrial hearing loss remains the occupational disease with the highest number of civil claims accounting for about 75% of all occupational disease claims (according to the HSE).
It’s important that companies comply with their legal duties as detailed in the Control of Noise at Work Regulations 2005. These regulations reduced the previous action levels and introduced legal limits for daily noise exposure.
This blog provides a simple 5-step process for those companies who are making efforts to control the noise within their workplace.
Step 1
The first thing you need to do is establish whether there are any noise hazards within your workplace. This can be achieved through a combination of your knowledge of work practices, making straightforward observations and taking some simple noise measurements in areas that you may suspect may present a risk.
Even at this stage of the process, we recommend that you use an acoustic calibrator to calibrate your sound level meter before and after each measurement session and keep a record of your measurements.
Step 2
Once you’ve found out which areas within your workplace may be a noise hazard, you need to identify which employees could be at risk of noise-induced hearing loss.
You should evaluate how harm may occur, for instance, damage to hearing, deafness, tinnitus, impaired communication and an inability to hear audible alarms.
We recommend that you also take into consideration susceptible employees or those that already have an existing hearing condition.
Step 3
A more detailed series of individual noise measurements are required to determine the typical exposures of those at risk, so you should talk with your employees to fully understand their typical work routine. You then have a choice of measurement methods.
Option 1: Integrating Averaging Sound Level Meter
The person carrying out your workplace measurements should be competent and should use a suitable sound level meter. Ideally, this meter should be compliant to BS EN 61672-1:2003 Class 1 or Class 2 and be from a reputable manufacturer.
Representative ‘A’ weighted average noise level readings (LAeq) are to be taken for each ‘task’ undertaken by an employee and then you should determine an individual’s exposure level by using software, mathematical formulae or the HSE exposure calculator.
The ‘A’ frequency filter is applied by sound measurement instruments in an attempt to replicate the response of the human ear to noise so that we can accurately determine the level of risk rather than the actual true noise level itself.
Option 2: Personal Noise Dosemeter
Alternatively, a noise dosemeter can be worn by a worker during their entire shift, which will monitor and measure the noise levels they’re exposed to throughout their specific working day.
Noise Dosimetry is particularly effective for workers with unpredictable shift patterns, those constantly on the move, or people working in confined or difficult to access areas.
Having made and evaluated your measurements, a Noise Control Action Plan is required. This plan is the most important part of the whole survey process and should demonstrate that you’re taking the necessary steps to control the identified risks.
Often forgotten is the necessity to assess the risk from any impulsive noise. The action levels for impulsive noise are 135dB(C) and 136dB(C) with the legal limit being 140dB(C).
Any plan you make should include a list of prioritised actions to solve immediate risks and to give consideration to your general duty to reduce noise levels in the workplace. Where noise can’t be reduced at source, suitable hearing protection is required which must be made available to all workers at risk.
Employees should be provided with information, instruction and training with respect to the risks and how to minimise and control them.
Step 4
All of the findings from the above should be used to create a clear report which should be in a style and format that could be easily referenced in future. This will provide permanent evidence of the decisions you have taken have to comply with the law.
Step 5
You should regularly review the effectiveness of your programme for controlling workplace noise. This will be especially necessary if new equipment has been introduced or there have been changes to the layout of your factory or working hours for your employees.
Find out more about the Noise at Work Regulations or speak to a member of the Pulsar team to find out more about how we can help you.
For more information on 5 Steps for Controlling Workplace Noise talk to Pulsar Instruments Plc
Enquire Now
List your company on FindTheNeedle.