
Dry Coolers
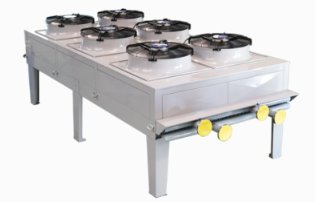
The need for sustainable and efficient cooling solutions is becoming increasingly important. One such solution gaining popularity is the dry cooler. In this article, we will explore the concept of dry cooling, its benefits, and its differences compared to chiller systems.
What is Dry Cooling?
Dry cooling is a method of removing heat from a system using sensible heat rejection without the need for water. Unlike traditional cooling methods that rely on water, dry coolers utilize air as a secondary fluid. They are commonly used in applications where water is scarce or restricted due to environmental regulations. Dry coolers are particularly effective in refrigeration applications, air-conditioning, and industrial processes.
How Do Dry Coolers Work?
Dry coolers operate based on the principles of sensible heat rejection. These cooling devices consist of fans that pull air from the cooler's exterior and circulate it over tubes containing a cooling fluid, typically water or a water-glycol mixture. The heat from the fluid is transferred to the air, and the cooled fluid is then circulated through a heat exchanger attached to the associated process. This heat exchange process enables efficient cooling without the need for water.
Advantages of Dry Coolers
1. Sustainability and Water Conservation
One of the major advantages of dry coolers is their contribution to sustainability and water conservation efforts. Unlike cooling towers, which require a continuous supply of water, dry coolers operate without water consumption. This makes them an ideal choice in regions where water scarcity is a concern or in areas where strict environmental regulations limit water usage.
2. Reduced Maintenance
Dry coolers offer reduced maintenance requirements compared to traditional cooling systems. Since they do not rely on water, there is no need for water treatment or the associated maintenance tasks. This not only saves time and effort but also reduces the overall maintenance costs of the cooling equipment.
3. Energy Efficiency
Dry coolers are designed to maximize energy efficiency. By constantly drawing large quantities of air through highly conductive aluminium fins, heat is quickly removed from the system and discharged into the atmosphere. This efficient heat transfer process ensures optimal cooling performance while minimizing energy consumption.
4. Versatility in Design
Dry coolers are available in various configurations to suit different cooling needs. Two common designs include the flat configuration and the V-configuration. The flat configuration offers a low-profile solution that requires minimal clearance, making it suitable for applications where space is limited. Moreover, the flat configuration has different variants enabling the flat unit to be installed either horizontally (with vertical airflow) or vertically (with horizontal airflow). The V-configuration provides maximum surface area per footprint, enhancing heat rejection capabilities.
5. Capacity
In addition to the configurations of the unit, the other variables are the quantity of fans, the size of those fans and the capacity of the coil which they are pulling the air through. It means there are many different models for a given overall size. In basic terms the greater the liquid capacity of the coil, the longer it takes for the liquid to pass through it, therefore the more heat can be transferred to the air being passed over the coil.
Dry Coolers vs. Air Cooled Chiller Systems
Although sometimes they are aesthetically alike, dry coolers and air cooled chiller systems are quite different. Both are used for cooling processes however there are notable differences between the two;
Dry Coolers
|
Air Cooled Chiller Systems
|
Dry coolers have a single heat transfer stage, from water to air; • The relatively warm water/glycol that flows into the dry cooler simply passes through the coil of the dry cooler. • Heat is transferred from the water/glycol to the air passing through the cool. • The water/glycol leaves the dry cooler at a lower temperature than it entered the cooler. They are particularly suitable for applications where water is scarce or restricted. Dry coolers are commonly used in refrigeration, air-conditioning, and industrial processes. They offer advantages such as sustainability, reduced maintenance, and energy efficiency. |
Air Cooled Chillers have two heat transfer stages; • The relatively warm water/glycol that flows into the chiller is cooled as it passes through a heat exchanger containing an evaporator. • The evaporator is part of a refrigerant circuit complete with expansion valve, condenser and compressor, which together act to transfer the heat removed from the water/glycol to the condenser. • The second heat transfer stage is when the heat moves from the finned condenser to the air passing through the outer surfaces of the condenser. They are commonly used in applications that require greater heat transfer, precise temperature control and are available in water-cooled and air-cooled variants. Chiller systems offer benefits such as precise temperature control, lower leaving temperature capabilities, and energy efficiency. |
Dry Cooler System Design
A typical dry cooling system consists of both outdoor and indoor components. The outdoor component is the dry cooler itself, while the indoor unit includes a compressor, heat exchanger, pipes for circulating cooling fluid, and an evaporator.
To ensure efficient operation, a suitable temperature difference between the cooling medium and the air within the dry cooling system must be maintained. Regular monitoring is necessary to ensure that the cooling fluid levels are adequate and to prevent any potential issues.
Applications of Dry Coolers
Dry coolers find application in various industries and processes that require efficient and sustainable cooling. Some common applications include:
-
Refrigeration: Dry coolers are used in refrigeration systems to maintain optimal temperatures for preserving food and other perishable items.
-
Air-conditioning: Dry coolers are employed in air-conditioning systems to regulate indoor temperatures and ensure comfort.
-
Industrial Processes: Dry coolers are used in industrial processes such as power generation and chemical processing to maintain optimal operating conditions.
-
Free Cooling: Dry coolers are also utilized in free cooling applications, where the ambient air temperature is low enough to cool the process fluid without the need for mechanical cooling.
Conclusion
Dry coolers offer a sustainable and efficient cooling solution for various industries and applications. Their ability to operate without water, reduced maintenance requirements, and energy efficiency make them an attractive choice for those seeking environmentally friendly cooling options. Whether in refrigeration, air-conditioning, or industrial processes, dry coolers provide reliable and effective heat rejection, ensuring optimal operating conditions while minimizing environmental impact.
Consider incorporating dry coolers into your cooling systems to enjoy the benefits of sustainability, reduced maintenance, and energy efficiency. Embrace the future of cooling with dry coolers!
The Puravent range of dry coolers is here
For more information on Dry Coolers talk to Puravent