
Sign In
Indoor Air Quality and Production Uptime
23-08-2016
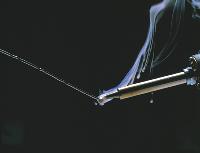
23/08/06 - Scott Snell, Purex Inc. Illinois - For most of us, long gone are the days of working outdoors in the fresh air with sunshine and a satisfying breeze to keep us moving along when we become fatigued. These days, most of us work inside. Although being out of the rain, heat and cold is nice; most of us also now breathe the air that comes from the workplace and those operations that take place within that workplace. This is not always the best.
Given that we were made to breathe clean and fresh air; it is no surprise that the level of indoor air quality is directly relative to our productivity levels.
Most manufacturing operations would be pretty hard pressed to find an approximate ten percent increase in productivity by doing what is: morally responsible to an employer, required by law and neither hard nor expensive to achieve.
Indoor air temperature and humidity has a well paved road that is easy to find solutions for on those matters. Often forgotten in correcting is the topic of airborne particulate and volatile organic compounds (VOC’s).
In manufacturing, essentially any operation where a material is cut, marked, heated, burned or physically altered in any way has the potential to produce harmful materials. These are a detriment to IAQ. Common areas of production that cause IAQ issues for both equipment and employees are laser coding, marking, cutting, decorating, soldering, cleaning, coating, sealing, laboratory processes and printing. All of these generate unacceptable amounts of particulate or VOC’s or both.Hazardous solder fume generated by a soldering iron
Almost all laser operations generate respirable dust in the form of Laser Generated Airborne Contaminants (LGACs) to one level or another. Most laser process also generate VOC’s from the laser interaction with the target substrate.
In laser marking, coding, cutting and decorating processes; at the point of contact (P.O.C.) with laser beam on a substrate there is complete oxidation resulting in carbon plus H20. A short distance from the P.O.C there is vaporization. Further away there is ablation, the removal of solid, semi solid or liquid particles/droplets. The effect of the laser on the air close to the material being laser processed is that the beam raises the temperature of the air at the P.O.C to 1500-2000 Deg. C causing rapid expansion and the projection of particles/droplets away in all directions, including back towards the laser lens. Everything that went into making that laser substrate can be loosened in the laser process.
Uncaptured laser particulate will cause damage to optics, poor codes, beam divergence, sensor failure, handling equipment problems, fire hazards, respiratory hazards, and other problems.
Additionally, particulate, VOCs and gasses are largely worker respiratory concerns. Occupational asthma is a rising concern among those that use lasers in their work.
Electronic manufacturing process like soldering (both by hand and machine) and cleaning, coating or sealing have by-products, both particulate as well as VOCs and gases. When heated, rosin-based solder fluxes form fumes containing a range of resin acid particulates and other components as gases. When inhaled, rosin based solder flux fume can lead to occupational asthma or make existing asthmatic conditions worse. Rosin-based solder flux fume is now regarded as one of the most important causes of occupational asthma and the effects can be irreversible. HSE statistics (2004/2005) showing incidence rates of occupational asthma reported by chest physicians put rosin based solder flux fume in the top ten. The fume, like most, can also cause irritation to the eyes and upper respiratory tract and can also cause dermatitis. Continued exposure, even to very small amounts of fume, may cause asthma attacks and the person affected may be unable to do any soldering with rosin-based fluxes again. Solder fume is classed as a hazardous substance and should be controlled as per international legislation. Cleaning, coating and sealing in electronics are largely classed as VOC or hazardous gas.
While the VOC’s present respiratory and worker health concerns, the particulate can cause real problems with finished products in electronic manufacturing like rejected parts, colophony, poor joints and connections poor wave and reflow profiles. This results in a poor performance product and the need for rework or worse scrap.
Laboratory concerns can include all of the above concerns of laser or electronics plus the additional concern of biological contaminants and pharmaceutical drug inhalation or contamination.
So when extracting all of these contaminants in our workplaces what does one do and where do they go?
One option is to vent to the atmosphere and hope for the best. This is not the most effective means of evacuation because it is not always practical to cut a hole in the roof, mount a big fan in the celling and blow fumes and dust outside. This is not viewed admirably by green councils, neighbours, sustainability groups and in some cases the EPA.
Venting to the atmosphere is expensive and time consuming to install. This method of extraction usually creates a fixed point rooftop extraction system that reduces the flexibility and possibilities of reconfiguration of existing production lines when production needs change. Most rooftop fan sets are relatively low pressure and allow for inconsistent air flow to process that are dependent on outside pressure levels, wind conditions, and weather conditions. If atmospheric ventilation is done incorrectly, the same air vented outside is often brought back inside as when you vent outside, a vacuum is created.
Add to all of this that you are effectively sending you heated/cooled climate controlled air outside there are substantial continuing operational costs involved with this solution as well as the initial set up. Creating inflexibility and inconsistency in a process or production environment are usually terms that are incongruous with increasing production.
Another option is to move the air in the workplace around and dilute it using benchtop fan sets. The problem with this method is that the contaminants dealt with in this regard are generally accumulative, and no clean air is introduced. This creates a dirty workplace with poor IAQ. This eventually will reduce worker comfort, cause worker downtime and create employee health concerns. Blowing dirty air from one worker to another is just moving the problem around and solves nothing.
It is becoming increasingly popular and affordable to capture contaminants at the source using localized exhaust ventilation devices (LEV) or “fume extraction devices”. These deal with problems where they are generated at the source.
Modern fume extraction devices are portable and can be easily moved when production lines need to be changed unlike roof sets used for venting outside. They also remove many of the questions of venting outside. Neighbours, sustainability and Green council groups like LEV solutions as they prevent external ventilation.
Outside weather conditions have no effect on LEVs and therefore no effect on processes such as reflow ovens or wave soldering units. Modern LEVs or fume extractors often reassure workers that return air quality is good as many have monitoring systems included in their displays. Good ones can produce better air quality than the rooms in which they are located. Modern systems also generally employ the use of both speed control and volume control. This allows for them to be set at the speed that they need to run and increase in speed as their filters become blocked. This uses less power than fan sets that run at a fixed speed, prevents inconsistency of air flow to processes, and allows for longer more predictable periods between maintenance.
These newer generations of LEVs generally allow for the use of a pre-filter and HEPA filtration combined with a chemical filter that will remove particulates and VOC’s or gasses. Because the capture generally recommended for use of LEV’s is recommended to be employed at the source of fumes and dust, they provide a solution for a clean and healthy work place. Fume extraction can be beneficial in all of the above operations as a means of safety and employee satisfaction. This leads to decreased sick time taken by employees. Fume extraction can also be directly linked to reduced maintenance in production lines, increased up time of equipment and hence increased production.
For more information on how fume extraction can help you increase productivity in your processes, please visit www.purex.co.uk | www.purexinc.com or phone: UK 44 (0)1405 746030 | USA 001 866 360 5675
For more information on Indoor Air Quality and Production Uptime talk to Purex International Ltd
Enquire Now
List your company on FindTheNeedle.