
Sign In
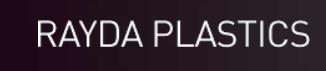
What are the Benefits of Custom Plastic Extrusion?
Custom plastic extrusion is the process of shaping materials via the extrusion process, into specific shapes using pre-made moulds.
It is used to produce new and existing products in a highly efficient and low-waste manner.
Below we look at what the benefits of this process are.
Adaptable Materials
Custom extrusion, as a process, is one that can be easily adapted to meet the needs of the manufacturer, due to the different options it is able to deliver via the pellets used.
The pellets that go in at the beginning of the process determine how the end product will look, and so manufacturers are able to work with a variety of different colours and finishes.
The extruded plastic emerges from the machine whilst hot and can therefore be further manipulated straight away, using rollers, dies and shoes, to meet requirements.
In addition, extrusion produces a product that is extremely durable, succumbing to little damage and boasting a long lifespan.
Low-Cost Production
The dies that are used with the plastic extrusion process are of a lower cost compared to those used in other processes. They are also a lot easier to modify.
As such, it is a simple process to either modify an existing die for a new job or even design a new one. This gives manufacturers a lot more control over the management of the process and quality of the product.
The overall manufacturing process itself is also low-cost as a result of being able to reuse waste, lowering the material and disposal costs. Machines can also run 24/7, significantly shortening production times.
Fast, Reliable Production
Production of custom extrusions is fast once the details have been decided and this means that production runs can be completed for manufacturers in good turnaround times.
It also means that trials of extrusions are easy to do and make adjustments to, without wasting time and money.
Shape and Length Options
When it comes to custom extrusions, the sky’s the limit! Sort of.
Using the dies, it is possible to create a variety of shapes as a cross-section. It is even possible to extrude shapes with a cavity, so long as the shape is able to support the central section.
In addition to this, the long lengths produced make it a viable process for applications in many industries, including medical, automotive, construction, retail and more.
For more information on the custom extrusion process and how it could benefit you, contact Rayda today.
For more information on What are the Benefits of Custom Plastic Extrusion? talk to Rayda Plastics Ltd
Enquire Now
List your company on FindTheNeedle.