
Sign In
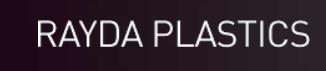
It is certainly no secret that while huge gains have been made in the area of recycling, the world is at a critical point when it comes to plastic waste.
Plastic has been used for decades because it has so many beneficial characteristics, a main one being its durability. However, it is this exact trait which makes it such a difficult material to dispose of. While major efforts have been made, it is still a fact that some part of nearly all plastic will still be present somewhere in the environment. Causing major issues for the planet as a whole.
In fact, of all plastic ever manufactured, only 9% has ever been recycled.
There are advancements in the field of plastic recycling being made every day, however. A big focus within the industry at the moment is the area of chemical recycling and Mura Technology, UK leader in plastic recycling, are leading the way.
Mura Technology are set to build the words first commercial scale recycling facility which processes all types of plastic using the chemical recycling method. It is also set to make a profit.
Chemical recycling works by turning waste plastic back into oil and, compared to traditional methods, reduces the amount of wasted materials and energy needed. But it has also traditionally been a much more expensive. The plant at Teesside is overcoming this by using Mura Technology’s hydrothermal chemical recycling technique which they claim reduces costs enough to make the process financially viable. If this is the case, the plant will be a real game changer in the plastic recycling industry.
Why Choose Chemical Over Traditional?
The current recycling processes which are used work by separating different kinds of plastic so it can be cleaned, shredded, melted down and moulded. And while this does work in a way, there are a lot of drawbacks.
Firstly, this process produces a lot of waste as some plastics either cannot be processed or are left due to uncertainty.
It is also extremely labour intensive and the final product that is produced is considerably inferior compared to virgin plastic. This is because the melting process breaks down the polymer chains, affecting strength and viscosity. As a result, the food and medical industry often have to manufacture using virgin products.
And the more you recycle a product in this way, the more the quality decreases.
In comparison, the recycling plant at Teesside is able to process all plastics, significantly reducing the need to sort plastics and reducing labour costs.
Additionally, rather than melting the plastic down, it instead produced an oil which still retains the good quality polymer chains and so is suitable for high end applications.
Mura Technology’s plant is set to open in 2022 and, if successful, will pave the way for the future of plastic recycling.
For more information on Worlds First All Plastic Recycling Plant for UK talk to Rayda Plastics Ltd
Enquire Now
List your company on FindTheNeedle.