
Truly Understand your product reliability with an Holistic Model from Reliability Solutions
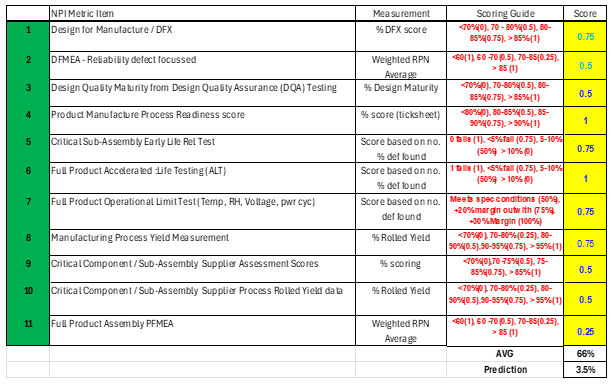
Unlocking World-Class Reliability: The Holistic Approach
Hey there, it's Martin Shaw from Reliability Solutions!
Wow, what a year 2024 has been! I've had the privilege of consulting with a variety of companies, helping them drive reliability improvements using the tools and methods I've developed within my Holistic Model. You might recall my blog from earlier this year on Holistic Reliability—let me take you through where this concept comes from and where we are now.
What’s Holistic Reliability, Anyway?
The term "Holistic" comes from the idea that the parts of something are deeply connected and can only truly be understood by considering the whole. This concept is vital when it comes to product reliability. Simply relying on tests like Accelerated Life Testing (HALT) won’t get you to the end goal. We need to take a deeper dive into the full suite of tests and proactive assessments necessary to prevent defects from ever happening.
Why is the Holistic Model Needed?
As technology advances, making realistic reliability predictions from limited testing becomes more challenging. The field failure rate targets for modern tech are incredibly low, which makes representative statistical testing difficult. Simulation models? They rarely give accurate predictions that match actual field data. Accelerated stress tests often can't simulate "real" defects. That’s why we need a new approach to drive a real change in reliability.
When and Who Can Benefit from This Model?
The earlier you apply the Holistic Model in the design cycle, the better. By measuring each factor as you go, you'll have a "running" or "fluid" score throughout the design phase and into pilot or initial production. This allows teams to quickly identify and address areas of weakness early on, improving the product later in the cycle. Project managers, in particular, will find this model useful to track how well each team (Design, Engineering, Quality, etc.) is performing, and see how their work impacts the product’s reliability. By the time you're ready to go into mass production, you’ll have a solid score that reflects how the product will perform both in manufacturing and the field.
A Brief History of the Holistic Model
Reliability has always been influenced by a range of factors, but the key challenge is bringing together these interconnected elements to affect the final product. Reliability Solutions is now in a great position to start sharing this model, offering a direct link between product reliability and quality. It’s an exciting time as we apply a solution companies have been waiting for, though they didn’t even know it—until now!
How to Build Your Own Holistic Model for World-Class Reliability
So, how can your company develop its own unique holistic model to achieve top-tier reliability? Here’s a roadmap:
-
Define Key Elements for Customer Satisfaction
What guarantees customer satisfaction for your product? Think long life, durability, appearance, ease of operation, and more. -
Set Methods to Achieve Your Goals
Your methods should support your goals. This might include:- Ensuring consistency in manufacturing with near-perfect tolerance matching
- High-volume production with minimal rework
- Improving process control to minimize early life defects
- Meeting field reliability targets (50% lower failure rates)
-
Define the Tools to Achieve Your Objectives
A range of tools can help achieve your goals within short life cycles:- A modified, effective DFMEA that actually gets engineers engaged
- Design for Manufacture (DFM) and DFx principles for better design
- Accelerated reliability testing at key levels to detect defects early
- Strong design quality testing to maximize defect detectability
-
Map Out the Product and Apply Tools in an Organized Way
- Review Design for Assembly with lessons learned
- Implement design quality testing and maturity measurement
- Conduct production readiness reviews for complex processes
- Create detailed accelerated stress test plans for each assembly level
-
Measure Each Factor
Define clear metrics for each factor. For example:- Design quality: Percentage of design maturity
- Early life reliability: Number of defects
- Accelerated life testing: MTTF predictions
- Production yield levels: Target vs. actual yield
-
Bring It All Together in a Matrix
Use a coordinated NPI (New Product Introduction) matrix that includes all the key elements impacting product failure and reliability. Assign targets and scoring mechanisms, then simulate previous products with the new metrics to calculate a "correlation factor." Once you have this, you can make a holistic prediction of your product’s reliability based on the full data suite.
The Next Step?
If you’re ready to dive deeper into the Holistic Model and learn how it can revolutionize your approach to product reliability, don’t hesitate to reach out!
You can contact me at reliabilitysolutions@yahoo.co.uk or connect with me on LinkedIn here.
Here’s to achieving world-class reliability together!
Best,
Martin Shaw
For more information on Truly Understand your product reliability with an Holistic Model from Reliability Solutions talk to Reliability Solutions