
Sign In
Infolda Hole Punch
19-09-2012
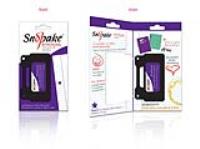
Brief
A client approached us with an idea he had successfully patented for a one piece plastic hole punch. He had been granted a patent due to several innovative design features, the most significant being that the base of the punch folded over to create a tray to catch the punched paper, as a conventional hole punch does. The product’s other unique features were its size, weight and a fold out tab which allowed it to be clipped on to the rings of a binder, hence the name Infolda.
To produce the product as a one piece moulding we were constrained to Polypropylene as a material. Polypropylene is the only suitable plastic for moulding live hinges on a component. Any other material will snap or crack under the repetitive stresses put on a hinge.
Concerns were raised about the suitability of polypropylene with regards to the punch heads, the concern being that the punches could become blunt and cease cutting the paper. We decided that if this did occur during testing, that the application of brass or steel punch heads to the moulding at the time of manufacture was a viable solution that would ensure the punch remained effective. We decided that we could work with this solution as a plan b if the plastic punches didn’t last, and began developing the prototype supplied by the client into a finished design capable of being injection moulded.
Design / Developmemnt
The client had built a crude prototype demonstrating the size and shape of the product. We took the model and from it created drawings and an evolved 3D CAD model – applying all the necessary considerations to make the product suitable for injection moulding. Once we had a design we were all happy with, a polypropylene prototype was machined in house using a CNC process. This method of prototyping in polypropylene enabled us to create the 3 live hinges which were to be present in the final design.
Many tests were applied to the prototype in order to refine the design, the bulk of which revolved around the suitability of Polypropylene for the punch heads. Eventually it was decided that plastic was not suitable for the punches, and so metal punch heads were designed to be applied at the time of manufacturing. It was decided that this was preferable to polypropylene punch heads although there were additional costs involved. The design was approved with by the client with metal punches, and so we went ahead and commissioned a mould.
Tooling
We advised our client that an Aluminum mould would be suitable, given that at this point, negotiations with buyers from major supermarkets and stationery companies were underway, but had not yielded any large orders. An aluminium tool saves time & money in the toolmaking phase, and would be adequate for manufacturing small to medium sized runs of hole punches as the project got moving. If demand suddenly increased, we could go ahead and commission a multi-impression tool made from fully hardened steel which would survive runs of millions of mouldings. Our toolmaker provided us with a tool GA drawing which we checked and approved. The tool was finished and up and running with us in about 6 weeks.
Manufacture
The initial runs of the infolda were manufactured at S.B.Weston’s plant in Sunbury. The idea was to run enough stock for promotional purposes and for the clients sales team to generate interest amongst the stationery buyers. At this stage a full production run has not occurred.
Conclusion?
The client was very happy with the final product, but unfortunately no large orders have been forthcoming… yet. S.B.Weston Ltd are ready to manufacture, and once we get the go ahead from the client and his sales team, we can go into full production. In the meantime we are happy to store and maintain the mould.
For more information on Infolda Hole Punch talk to S.B.Weston Ltd
Enquire Now
List your company on FindTheNeedle.