
Sign In
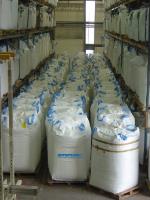
A bulk bag filler is an investment and is often a vital addition to a process that involves bulk ingredients. As with any capital expenditure, it is important to know what kinds of bulk bag filler problems you may encounter, and how you can avoid them. I assure you, the benefits of bulk bag fillers outweigh any possible drawbacks. If used properly, those drawbacks are non-existent.
Spiroflow has been around for more than four decades. We specialize in powder handling and dry solids processing. Safely and efficiently filling bulk bags is one of our best skill set, and we know how important that is to our customers.
WHAT TYPE OF BULK BAG FILLER?
There are several bulk bag filler models out there.
Because every process is different, there are many variables you’ll need to consider when choosing a bulk bag filler:
Available headroom
filling by weight or volume
how filled bags will be removed
the material they are being filled with
BULK BAG FILLER PROBLEMS
Bulk bag filler problems can be sorted in several different categories. Here’s how to fix and/or prevent them.
This article gives a general overview. Please be sure to consult your manufacturer and user manual for detailed instructions specific to your bulk bag filler.
STAYING SAFE WHILE FILLING BULK BAGS
First of all, only trained personnel should operate, clean, or maintain the bulk bag filler. A bulk bag filler can be dangerous if not used correctly.
Consult with your manufacturer on what materials and containers should and shouldn’t be used with your filler.
Working on a filler without guards, fixed flexible connectors or any other safety devices should only happen with the machine turned off. The unit feeding the filler must be safeguarded against unintentional start-up.
Compressed air is a potential hazard that should be mentioned. A lockout valve is supplied with air equipment to isolate the machine when it’s being serviced. Check with your manufacturer and/or manual about the maximum allowable operating pressures.
The condition of the bulk bag should be monitored too. If the bag’s body or lifting loops are damaged, the bag shouldn’t be used. Do not stand near the filled bag while it’s being lifted.
TROUBLESHOOTING A BULK BAG FILLER
Are you getting an incorrect weight reading (verified by weight of a known amount)?
Possible Cause: The weigh platform is resting on debris or other foreign objects.
Solution: Clear debris or objects from around weigh platform.
Possible Cause: The rigid connection is tied to the weigh platform.
Solution: Use only flexible connections to the weigh platform.
Possible Cause: Set points on the weigh platform are improperly set.
Solution: Set points should be reentered using the weigh control manual as a guide.
Possible Cause: The load cells may be damaged.
Solution: Check the signals from the load cells (qualified electrician required). Replace the damaged load cell(s) and send the original load cell out to be tested.
Possible Cause: The weigh display panel may need troubleshooting.
Solution: Refer to weigh display manual for troubleshooting information.
Does the neck seal fail to properly inflate?
Possible Cause: The air supply is shut off or disconnected.
Solution: Turn ON the air or reconnect the air supply. Readjust the air regulator if required.
Possible Cause: The inflatable sleeve is leaking so much that it is unable to seal on bag neck.
Solution: Repair or replace the sleeve.
Possible Cause: The Inflate / Deflate switch is faulty.
Solution: Repair or replace the switch.
Possible Cause: The neck seal is over inflating.
Solution: Decrease the air pressure on the precision regulator.
Possible Cause: There is possible blockage or leakage in the air lines.
Solution: Replace or repair the air lines.
Possible Cause: The inflate switch is faulty.
Solution: Repair or replace the inflate switch.
Does the bulk bag liner fail to inflate? (Only applies to optional bag inflation)
Possible Cause: The air supply is shut off or disconnected.
Solution: Turn ON air or reconnect air supply. Readjust air regulator if required.
Possible Cause: There is a blockage or leakage in the air lines.
Solution: Replace or repair the air lines.
Possible Cause: The inflate switch is faulty.
Solution: Repair or replace the inflate switch.
MAINTENANCE AND INSPECTION
Regularly monitoring your equipment might be the best way to avoid mechanical failure.
If you are filling by weight the weigh platform should be inspected on a monthly basis to ensure it is level.
If you are filling by weight any spillage buildup should be cleaned as soon as possible. Erroneous weight readings may occur if the weight platform has foreign debris.
If you are filling by weight use a test load of known weight to verify a weight readout on a bimonthly basis. This may give an early indication of future load cell problems. This may also be an indication that the weigh platform is out of calibration.
If you are using vibration in your filling operation the rubber vibration isolator mounting pads should be inspected after every 1,000 hours of use for signs of wear or deterioration.
The inflatable sleeve on the neck seal should be inspected monthly for pin holes, cracking, or other signs of deterioration. The loss of air pressure in a neck seal with a damaged sleeve can result in dusting and improper filling of the bulk bag during the filling cycle.
The air lines and air supply filtering devices should be inspected at least weekly for cracks, leakage, and moisture build up. Drain and repair as needed.
A complete bolt check monthly or more frequently when using vibration to compact product is recommended.
For more information on Bulk Bag Filler Problems: Staying Safe & Keeping It Operating talk to Spiroflow Ltd
Enquire Now
List your company on FindTheNeedle.