
Sign In
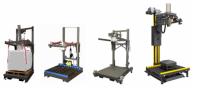
There’s more than one way to fill a bulk bag. What method makes the most sense? An operator can choose to either fill by weight or by volume, depending on the application.
Filling method isn’t the only decision to make. There are several types of bulk bag fillers to choose from. Finding the answers to these questions usually starts with a conversation between you and a supplier. This article for anyone that’s not ready to speak to an engineer and would rather do some research on their own.
I want to mention that our team at Spiroflow has been helping processors with bulk material handling solutions for more than four decades. We’re proud of the reputation we’ve built in that time. I hope this article answers any questions you have about the best filling method, volumetric or gravimetric.
FILLING A BULK BAG
How you plan on using bulk bags is a topic that will be discussed between you and the supplier. Bulk bags are used across several different industries. They can typically hold between 1,000 lb (450 kg) and 3,000 lb (1,350 kg). Bulk bags are utilized in all stages of the production process but most often at the beginning or end of a process. Of course, they’re used to store or transport raw materials. They’re also used to ship the finished product to customers.
The right bulk bag filler can quickly and safely fill a bag without dust escaping. The biggest factor in determining which filler will handle your application at the best price is if the equipment will fill by weight or volume.
HOW IS YOUR PRODUCT SOLD?
Generally, if your product will be sold by weight then you’ll need a bulk bag filler that fills by weight. Countries have different laws and regulations to protect consumers. I suggest consulting with your supplier about what additional equipment is required for your country.
For products that are sold by volume, you’ll need a bulk bag filler that fills by volume. These fillers are also useful in plants that fill bulk bags with raw or intermediate materials that are stored or moved to another plant. In this scenario, the bags are emptied into an external device such as a bulk bag discharger or a hopper with load cells that measures the material as it’s discharged.
HOW VOLUMETRIC FILLERS WORK
Volumetric bulk bag fillers consist of bulk bag support frame with a filling head at its top. The frame can either support the bag on a pallet or suspend the bag from its lifting loops over lifting arms on the filler. A supply vessel, process vessel, or conveyor located above the filler discharges material into the filling head for loading into the bulk bag. An inflatable neck seal, adjustable clamping strap, or large rubber band holds the bag’s inlet spout tightly around the filling head to prevent dust from escaping from the bag during filling. The filling head consists of an inner annulus, through which the material flows into the bag, and an outer annulus, which releases the air displaced by the incoming material. For dusty materials, the outer annulus ducts the displaced air to a dust collection system so it can be cleaned and safely exhausted to the atmosphere.
An optional operated blower on the bulk bag filler frame provides airflow for inflating the empty bulk bag before it’s filled. Inflating the bag ensures that it’s correctly formed to accept your material so the bag can be filled evenly and to its maximum capacity. Bag inflation also eliminates fabric creases that could hinder the bag’s complete filling. The filler frame can be designed to handle your plant’s headroom limitations and, depending on the model, can be adjusted manually or automatically to adjust to bulk bag height variations.
The filler can be operated manually or automatically once the bulk bag is loaded onto the filler and inflated. In manual operation, an operator typically opens the supply or process vessel’s outlet valve (or starts the conveyor) and closes the valve (or stops the conveyor) when the material reaches a certain level in the bag or completely fills it.
The level sensor is located in the supply or process vessel at the point where the material level equals the correct bulk bag volume. When the material loaded into the vessel reaches this volume, the level sensor signals the vessel’s outlet valve to open, discharging the vessel’s entire contents through the filling head into the bag. You can also use a level sensor to stop the material loading into the supply or process vessel and discharge the vessel’s contents to the bag.
The sensor is suspended from the filling head and positioned to detect the point in the bulk bag where the material will reach the required volume. This detects when the material filling the bag reaches this point and signals the supply or process vessel’s outlet valve to close or the conveyor to stop.
Depending on your material’s characteristics, the filler can be equipped with an electrically or pneumatically operated vibration device to de-aerate and compact the material as it fills the bulk bag and after filling is complete. This ensures that the bulk bag has a stable shape for safe handling, storage, and transportation. Materials that are easily fluidized, like flour and carbon black, require vibration for compaction, while non-fluidizable materials, such as coarse sand and plastic granules, do not.
For highly aerated materials users may opt for a more substantial bulk bag filler design that is specifically designed to provide more robust densification.
HOW GRAVIMETRIC FILLERS WORK
These fillers fill by weight. They consist of a bulk bag support frame, a filling head, and an electronic scale with load cells and a control panel. The filling head is the same as that for a volumetric filler and can be held tightly on the bag inlet spout by the same devices. As with the volumetric filler, a supply or process vessel or conveyor supplies material to the gravimetric filler, and a blower on the filler frame provides bag inflation. The filler can be equipped with a vibration device to de-aerate and compact the material as it fills the bulk bag, and the frame can be designed to handle your bulk bag height and headroom limitations.
The filler frame and scale can be configured in different ways. The filler can have a platform-weighing design in which the load cells are under a platform that supports the bag on its pallet. Alternatively, a filler can have a hang-weighing design, in which the load cells suspend the lifting arms holding the bulk bag. In a filler with a platform-weighing design, the weighing platform is usually load-cell mounted and an integral part of the filler. In some cases, the filler manufacturer incorporates a proprietary platform scale into the filler. The scale in any platform-weighing or hang-weighing filler requires appropriate weighing equipment to meet national standards.
After the operator loads the bulk bag on the gravimetric filler, inflates the bag, and uses the scale’s control panel to start the filling process, the scale senses the weight of material in the bulk bag as it fills and automatically sends output signals to the supply or process vessel’s outlet valve to close, or to the conveyor controls to stop the conveyor.
When selecting a platform-weighing or hang-weighing gravimetric filler, be aware that the hang-weighing filler offers two advantages. The major advantage has to do with how much weight the suspended scale must measure. Both platform-weighing and hang-weighing scales must be tared (zeroed out) between weighments to ensure that only the bulk bag’s contents are weighed. But when the bag and its contents, the pallet, and the platform support structure under the pallet rest on load cells, as in the platform-weighing filler, the scale must weigh all of these items, and the support structure is often particularly heavy. When the load cells suspend the lifting arms holding the bag’s lifting loops, as in the hang-weighing system, the scale weighs only the lifting arms, the bag, and its contents. This requires weighing and taring less metal in relation to the bag’s contents, so the suspended scale can provide greater accuracy.
The second advantage is that the suspended scale’s load cells are mounted high up in the filler frame, protecting them from potential forklift damage. When the platform in a platform-weighing filler is hit hard by a forklift, the resulting lateral forces can damage the load cells. While the load cells can be protected by installing a strong buffer that can stop the forklift before it hits the platform, a hang-weighing filler’s load cells are intrinsically protected from forklift damage.
CHOOSING THE RIGHT SUPPLIER
Choosing the right supplier is an important part of this process. A reputable supplier will make sure you’re getting the equipment that fits your needs at a reasonable price. Ask if the supplier can provide case studies or if they have patented designs that prove their expertise in the industry. You should also ask about a material test. A test is the best way to ensure your product will run in your application as expected.
For more information on Bulk Bag Fillers by Weight or Volume: Which Method is Best? talk to Spiroflow Ltd
Enquire Now
List your company on FindTheNeedle.