
Sign In
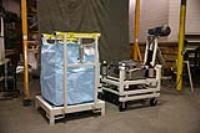
Our most challenging Bulk Bag Discharger yet!
Both Spiroflow Ltd and our US sister company Spiroflow Systems Inc of Monroe, North Carolina, offer 9 different types of Bulk Bag Discharger that have been introduced and developed over the past 25 years to cater for the majority of applications. Models range from simple bag hanging frames for the easiest free-flowing, dust-free plastic granules, through dischargers capable of promoting the flow of the most difficult products, to those able to ‘totally’ contain the most obnoxious chemicals or active pharmaceuticals.
However, there are always those extraordinary applications where a customized solution is the only answer. To meet these challenges, we apply our 35+ years of engineering and applications experience. An excellent example of this being the challenge posed at one of the US sites operated by one of the world’s leading chemical companies. Here they were looking to replace the labour intensive, manual tipping of 20 kg sacks of product into various process vessels. They elected to source their bulk materials and additives in 1,000 kg bulk bags instead. To accommodate this, they required a bulk bag un-loader complete with loss-in-weight metering feeder to ensure the correct weights of materials are dispensed into each of the process vessels. The un-loader needed to be fitted with flow aids to ensure the discharge of the more difficult materials. Operator protection and safety were paramount considerations and, to cap it all, the unit had to operate in some very tight spaces, be fully mobile to operate safely within a hazardous environment! It was our US operation that rose to this challenge.
Restricted Headroom
The restricted headroom part of the challenge was fairly straight forward: our model T5 Bulk Bag Discharger/Un-loader is designed specifically for restricted headroom applications. With this design, using a forklift truck, the upper section of the Discharger is removed and brought to floor level for the bag to be inserted. The bulk bag itself is suspended by its loops from a lifting frame. The lifting frame, with bag suspended, is installed into the de-mountable upper section, again by way of a forklift truck. The purpose of this de-mountable upper section is to make it possible to lift the frame, complete with bag, from underneath - thereby eliminating the height that the fork truck mast normally extends above the top of the bag. This reduces the headroom required considerably. The upper section with bag is then lifted and docked on the lower half of the Bulk Bag Discharger. This lower section has a docking seal that interfaces with a mating flange on the upper frame. This seal prevents dusting during the bag emptying process.
Loss-in-Weight Metering of Materials
The metering of bulk components and ingredients by weight is also straight forward for us. our model T3, loss-in-weight Bulk Bag Discharger, is designed just for such applications and is capable of accurately metering several bags and/or part bags whilst keeping track and a record of what has been dispensed.
The Application
In this application, the leading chemical company had some very specific requirements and site constraints. The overall dimensions of the machine and also of the 2 separate halves had to be suitable for use at multiple locations on site and, to add to the complications, the route between locations is via a service elevator. The manufacturing facility has limited headroom. It was specified that the ‘Spiroflow’ Bulk Bag Discharger should not exceed 2.75m in height when operational and be capable of collapsing down to within both a height and a width of 2.0m to facilitate movement around the plant. In operational mode, a height of 1.3m is required for the body of bulk bag whose suspension loops extended another 25cm above that! And, as stated previously, the unit also has to operate in a hazardous environment.
The Customised Solution
Every detail on the machine was defined by the total operating height available of 2.75m and, as mentioned above, this includes the 1.3m tall bag with 25cm long loops. The other design constraint being the restricted route between the process areas. A side tensioning frame is included, to keep the bag taught as it empties. However, pneumatic air cylinders were fitted in place of the usual coil springs. This enables the height of the side frame to be lowered when the unit is being moved around. The lifting frame to which the bag loops attach is only 5 cm tall and uses sections that allow the length of the loop to be shortened vertically by spreading them out horizontally.
The on-board controls include both intrinsically safe components and EXP rated motors for the 2 integral screw conveyors and the product agitator. The electrical enclosure, with digital weight indicator for batch feeding of a set point controlled weight, is fitted with an air purge system to allow it to be used in the hazardous environment. Static dissipating casters were provided in addition to the forklift access points. These allow the unit to be manoeuvred between some locations without a fork truck and without causing a spark due to any build-up of static-electricity.
The machine features a 4 corner dish mounted, 2 part, bag massage system. Here, the air cylinders are mounted on the lower frame and the massage paddles are hinged and attached to the de-mountable upper frame.
The collection hopper into which discharged material flows incorporates an integral agitator that prevents any bridging across the inlet of a horizontal ‘Spiroflow’ Flexible Screw Conveyor below. This short conveyor is fitted with a ‘Pro-screw’ type spiral that pushes material into a second 100 mm diameter conveyor, this time fitted with a flat section auger and mounted at 80° to the horizon. Both conveyors, plus the feed hopper with vibrator and agitator, are all mounted on the weigh frame such that the amount of material that exits the inclined screw, and therefore ‘lost’ to the system, is precisely regulated – thus ensuring highly accurate dosing, by weight, of materials into the various process vessels.
For more information on Our most challenging Bulk Bag Discharger yet! talk to Spiroflow Ltd
Enquire Now
List your company on FindTheNeedle.