
Sign In
Spiroflow™ conveyors cap them all!
13-07-2012
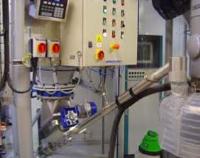
Spiroflow™ conveyors cap them all!
It’s not often that customers take the trouble to send suppliers unsolicited testimonials but that’s exactly what Bernard Partridge, Technical Advisor for the United Kingdom Atomic Energy Authority (UKAEA) at Harwell did to us! We supplied a Flexible Screw Conveyor to transfer the cement which UKAEA use to encapsulate radioactive waste within their Liquid Effluent Treatment Plant (LETP). UKAEA are so pleased with the performance of the conveyor that their testimonial reads, “The feeder system that you supplied to us has been running routinely for several months now and has performed excellently, giving very consistent feed rates and no problems. So thank you all for a very good job”.
UKAEA was incorporated as a statutory corporation in 1954 and pioneered the development of nuclear energy in the UK. Today they are responsible for the decommissioning of the nuclear reactors and other radioactive facilities used for the UK’s nuclear research and development programme, in a safe and environmentally sensitive manner. Harwell, Oxfordshire is the headquarters of UKAEA. The three research reactors there were closed in 1990 and since then significant progress has been made in removing the nuclear facilities and the site is now being progressively developed for commercial use.
At Harwell they have 100m3 of intermediate and low level radioactive waste in liquid and sludge form safely stored in tanks housed within concrete lined secondary containment. Over a three-year campaign, this mobile waste is being immobilised by encapsulation in a cementitious matrix capped off with a cement grout, all within 500 litre stainless steel drums. The majority of the drums are then stored on site at Harwell pending disposal to the NIREX national repository, with a small proportion of the low level waste being sent to British Nuclear Fuels for disposal at Drigg.
Liquid waste is pumped from the storage tanks to a stock vessel and a batch of waste is then charged to a drum. A premix of Blast Furnace Slag and Ordinary Portland Cement (BFS/OPC) is then added to the drum up to a capacity of 390 litres when combined with the liquid. Each drum is equipped with an internal paddle which, when driven through an external drive, ensures a homogeneous, monolithic matrix of waste and cement. The paddle is sacrificed and becomes encapsulated within the matrix, which takes about 24 hours to cure.
Once the matrix has cured, 50 litres of cement grout, a mix of Pulverised Fuel Ash and Ordinary Portland Cement (PFA/OPC), is charged to the drum to cap the matrix and to reduce the residual space at the top of the drum to less than 15 litres. The drum is then fitted with a stainless steel lid, after which it is checked for external radioactive contamination, and transferred from the shielded tunnel, in which the encapsulation and capping processes take place, to a shielded store.
A bowl mixer, with a 136 litre maximum capacity, is used to prepare the required batch of capping grout. The mixer is located on a weighing platform supplied to UKAEA by others. The Spiroflow conveyor is used to transfer a precise weight of PFA/OPC premix from a storage silo to the mixer bowl - which is pre-charged with water. The precise weight is achieved by a control signal from the weighing platform. So precise is the conveyor and so consistent is the powder feed rate from batch to batch (+/-1.5%) that UKAEA do not use the trickle feed facility at the end of each batch. They have set an optimum conveying speed via the frequency inverter that controls the drive motor such that there is a small and reproducible carry-over of product when the motor stops. Overall the batch system and the precise performance of the conveyor permit close control of the volume of capping grout prepared and the ratio of PFA/OPC to water in the mix. This, in turn, enables the volume of grout produced to be such that overfilling of the drum is impossible, thereby avoiding any risk of the major clean-up problem that might otherwise arise if spillage occurred within the process tunnel.
The ‘Spiroflow’ Conveyor has been in operation since July 2004 and was purchased as part of a plant improvement exercise. UKAEA became aware of ‘Spiroflow’ Flexible Screw Conveyors, and chose to use one for their LETP improvements, because they were delighted with the performance of a similar conveyor supplied by a third party as part of an inactive unit used to demonstrate the waste encapsulation process.
The conveyor was installed and commissioned by UKAEA’s own engineers. According to Bernard Partridge, installation could not have been easier. As it had been impossible to anticipate the final radial position of the conveyor, the ‘round to square’ transition piece, supplied by Spiroflow, which connects the conveyor to the silo incorporates a slip ring trapped between flanges to accommodate this. The conveyor inlet hopper houses an agitator to ensure no bridging of the cement over the inlet to the rotating spiral. Although this hopper is furnished with a removable access panel, no cleaning out has been necessary since installation.
UKAEA’s conveyor is unusual on two counts: firstly it is driven from the bottom rather than the top and secondly the conveying tube is of stainless steel, not our traditional flexible UHMWPE plastic. The majority of ‘Spiroflow’ conveyors are top driven but the layout and modus operandi made it impossible on this occasion. The stainless steel tube was used instead of UHMWPE because no support could be provided at the top otherwise the weight of the conveyor would have affected the mixer weigh platform.
For more information on Spiroflow™ conveyors cap them all! talk to Spiroflow Ltd
Enquire Now
List your company on FindTheNeedle.