
Sign In
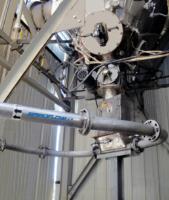
Structural drag chain conveyor problems happen, but they are avoidable. I understand why you’re wondering about these conveyors. They are an expensive addition to any process, and you want to make sure you’re getting your money’s worth. This article is about helping you keep the conveyor running.
Spiroflow has been around for more than 45 years. Our team members take pride in assisting customers with their dry bulk solids and powder processing needs. This ranges from providing a simple hopper to a complete bulk material handling system. Our work isn’t done when the equipment is shipped. We want to make sure everything works well and as expected. Here’s how.
DEFINING STRUCTURAL DRAG CHAIN CONVEYORS
I want to spend a short part of this article describing what these conveyors are and why they’re needed. Structural drag chains are constructed within schedule 40 pipe and move material with an ultra heavy-duty chain and disc assembly. The design of these machines makes them problem solvers for processors in search of the perfect conveyor for the most challenging conveying applications.
These should not be confused with tubular drag chain conveyors. Structural drag chains can handle material that tubular drag chains can’t.
STRUCTURAL DRAG CHAIN CONVEYOR PROBLEMS
ATTENTION TO MAINTENANCE
No conveyor is immune to the need of regular maintenance. Imagine having your chain conveyor malfunction while it’s conveying a sludge-like product. Your system is halted and you have to figure out how to get the material out of the conveyor without it working. The sprockets can be manually rotated to empty the conveyor and to make the proper repairs. That’s time you can’t have back and it’s something that can be prevented.
I suggest making it a point to check the conveyor’s housings for wear every month. This type of conveyor is built to last a long time and you should expect them to last considering their price.
CHOOSING THE BEST DESIGN
The fact that these conveyors can operate in up to three planes, such as a z-formation, is a plus. Keep in mind that with each added bend, an increase in horsepower is required. Usually, simple layouts are best.
Choosing the correct disc can also prevent issues in the future. There are plenty of options to choose from. Be sure to talk to your supplier about your product. The disc must be able to withstand possible chemical attack, abrasion, temperature, and more.
Ultra High Molecular Weight Polyethylene (UHMWPE) discs are among the most popular choices. This material has extremely high abrasion resistance, low coefficient of friction, high impact strength, and long service life. It can handle temperatures up to 176°F (80°C).
Cast iron discs are another popular option for drag chains. The material has a low cost and reasonable service life. This type of disc is a good option when corrosion, abrasion, chemical resistance, and product contamination are not factors. Mild steel can be used as an alternative. Both metals can handle temperatures up to 480˚F (250˚C).
You don’t have to sort these details out on your own. A trusted supplier can recommend the optimal layout as well as the best chain and disc assembly based on your application.
ARE STRUCTURAL DRAG CHAIN CONVEYORS A FIT?
SPEED, CAPACITY, AND LENGTH
Structural drag chain conveyors can run at speeds up to 50 ft/min (15 m/min) with a capacity up to 10 ft3/min (0.28 m3/min). A conveyor’s maximum total length is up to 400 ft (120 m) and multiple conveyors can be linked together.
CONVEYABLE MATERIAL
We consider these conveyors to be ultra heavy-duty pieces of equipment. With that label, it means the conveyor can handle almost any type of bulk material. The following types of materials are typically conveyed well:
Dry
Fragile
Abrasive
Hygroscopic
Moist
Cohesive
Hot up to (482˚F/250˚C)
Sludge
It’s worth mentioning that these conveyors leave behind a low amount of residual material.
DUST CONTROL
Structural drag chains are mechanically dust-tight and have an enclosed loop system. No systems filters are required.
REMEMBER TO USE A TEST LAB
A trustworthy supplier will suggest running a material test before your design is finalized. That’s the only way to know for sure that your material will run in your application. Spiroflow has test labs in the United States and the United Kingdom. I can tell you from experience that fine-tuning a conveying application is easiest in during the testing phase.
For more information on Structural Drag Chain Conveyor Problems: Keeping It Moving talk to Spiroflow Ltd
Enquire Now
List your company on FindTheNeedle.