
Sign In
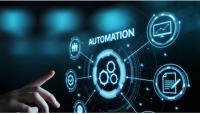
The challenges of automation for smart manufacturing
The implementation of smart manufacturing is a very worthwhile process. If done successfully, businesses will enjoy enhanced efficiency and flexibility in terms of production processes. It is also a good way to make your production enterprise future proof. A mindset of planning for the future is essential when you implement smart manufacturing projects that involve intelligent systems, machines and networks. These solutions can independently exchange and respond to information to automatically manage industrial production processes, and this is unlike anything that has existed before.
The big picture
A smart manufacturing project must be approached with a holistic view of an enterprise. This means everything from customer demand/order processing and control of ingredients and raw materials to flexible, efficient plant production. Waste, energy consumption and downtime should all be kept to an absolute minimum. To achieve all these goals, it may require a staged approach made up of small initial steps. Understanding the manufacturing plant’s goals and ‘pinch points’ is fundamental to the discovery of quick wins and boosting confidence in smart manufacturing processes.
Today, there is the technology to implement smart manufacturing, and entire production facilities could be designed around the concept. However, the reality is often not a new plant, but an existing one that requires upgrades to meet the necessary criteria and enjoy the benefits of smart manufacturing.
What is smart manufacturing?
The term ‘smart’, in its simplest form, is all about collecting data from the manufacturing process and converting it into information that can be acted upon. Intelligent data must be gathered from the plant so that all decisions can be made in an informed way, thereby improving overall efficiency and productivity with minimal waste. Intelligent data must come from the ‘sharp end’ of processes. Existing sensor and actuating technology enables devices to have self-determination and sophisticated error checking, in addition to the usual function of processing information for control, production analysis and maintenance.
A traditional production plant will have consisted of ‘automation islands’, but for the true potential of data gathering to be unlocked, infrastructures must create a holistic architecture for the collection and management of data. It is feasible to essentially overlay a data-gathering ‘layer’ over the existing automation control in order to extract data from disparate systems and make them communicate with one another. Thus, it is helpful to ensure all automation hardware is able to function as a component of a flexible, open network strategy, able to interface with multiple network protocols.
Upcycling existing technologies
When the assets in a plant are under the control of automation, for example, programmable logic controllers (PLCs), much of the critical data that is needed for the smart manufacturing concept is already present. All that is missing is the capability to transfer that data to the higher-level systems. By implementing the aforementioned ‘data gathering layer’, all the vital production and maintenance data can be collated and passed on to those higher-level systems to be analysed and utilised for decision making. The improvements in productivity and efficiency come from knowing precisely how the plant is currently performing, in real-time, and delivering intelligent plant data through a robust infrastructure.
The data gathering layer would be referred to as the ‘edge computing’ layer. Technological advancements in this area will provide facilities with all they need to perform complex, detailed data analysis and deploy sophisticated Artificial Intelligence (AI) to rationalise the vast amounts of data the systems are collecting from the entire plant. This will keep the data that needs to be transferred to higher-level systems to a minimum, which is good because processing it at that level can be a costly exercise.
Making it happen
The investment it takes to deliver a true smart manufacturing plant will depend mainly on the existing infrastructure. Another key factor will be the age of the automation equipment that is currently being used. If production plants have a survey done of what is already being used, they may discover some ‘low hanging fruit’ that will help make it easier to reach that goal of achieving smart manufacturing.
Once it has been achieved, there are many benefits associated with smart manufacturing. These benefits include:
Increased flexibility to respond to changes in customer demand.
Efficient scheduling of tasks to make the best use of time and maximise productivity.
Keeping downtime to a bare minimum through preventative maintenance processes that enable systems to change from one product to another quickly.
Minimising waste and energy consumption by getting the most out of what’s available.
The result of all these benefits will be greater overall profitability, and this is the ultimate objective of any manufacturing business. Overcoming the challenges of automation to achieve true smart manufacturing may not be an easy process, but it is a worthwhile one.
For more information on The challenges of automation for smart manufacturing talk to Subcon Laser Cutting Ltd
Enquire Now
List your company on FindTheNeedle.