
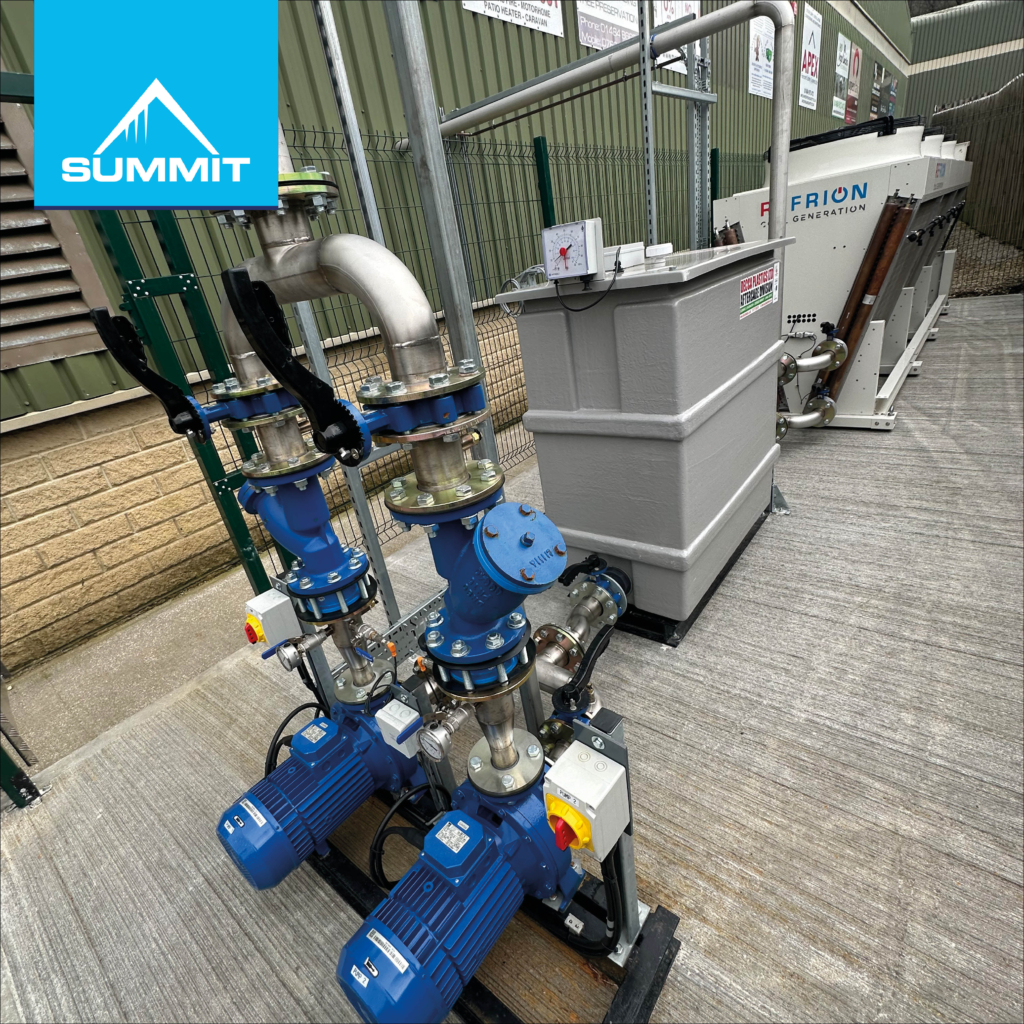
Fisher Plastics, based in Huddersfield, UK, is a leading toolmaker and moulder in the plastic injection moulding industry. Their extensive product range includes components for the automotive, medical, building services, education, and leisure sectors. A critical part of their manufacturing process is keeping hydraulic power packs and moulds cool to ensure efficiency and product quality.
The company faced significant challenges with their existing chiller system, which consumed large amounts of energy to cool both the moulds and hydraulic oil circuits. Rising energy costs were putting financial pressure on the business, and reliance on a single, large chiller created a risk of operational downtime. Failures in the system had already resulted in production losses, highlighting the need for a more efficient, reliable, and cost-effective solution.
Summit’s Energy-Efficient Cooling Upgrade
Summit Process Cooling proposed an innovative system upgrade to address these issues. Their solution involved replacing the outdated Bluebox chiller with an adiabatic cooler for hydraulic oil and throat cooling, while repurposing the Industrial Frigo chiller exclusively for mould cooling. This approach optimised existing equipment, minimising waste while maximising efficiency.
A key feature of the new system was the integration of an adiabatic cooler, which provided free cooling for the Industrial Frigo chiller during low ambient temperatures. This significantly reduced reliance on the chiller’s compressors, cutting energy costs and extending equipment lifespan. A plate heat exchanger (PHE) was installed to manage cooling circuits, with a 3-way temperature control valve automatically pre-cooling water from the moulds via the adiabatic cooling system in colder conditions.
To prevent freezing, glycol was used in the adiabatic cooling circuit, while the mould cooling circuit remained glycol-free to avoid slip hazards from potential spillages during frequent mould changes.
The upgraded system also featured stainless steel pipework, replacing outdated carbon steel to eliminate corrosion risks. A buffer tank and separate pipework circuits were installed for the hydraulic oil coolers, alongside a duplex filtration system to remove particulates and maintain water quality.
Advanced Automation & Control System
To enhance efficiency and ease of operation, the system was equipped with an HMI touchscreen control system featuring:
- Automated operations for seamless control.
- Rotating duty and standby pumps for even wear and extended lifespan.
- PLC software monitoring to track return water temperature, ambient conditions, and switch to free cooling when possible.
Results: Dramatic Energy Savings & Improved Performance
The installation was completed with minimal disruption, thanks to close collaboration between Fisher Plastics' management and Summit’s expert team. The benefits of the new system were immediate:
- Annual energy savings of 357,667 kWh, translating to £150,220 in cost reductions.
- 90% reduction in energy consumption compared to the previous system.
- Free cooling mode enabled the system to deliver 200kW of cooling while using just 6.5kW of energy, achieving a coefficient of performance (COP) of 30.7.
- Elimination of glycol in the mould cooling circuit, reducing environmental impact.
- Improved operational reliability with standby pumps and separate cooling circuits, reducing the risk of downtime.
- Extended chiller lifespan due to reduced compressor workload.
Customer Feedback: A Game-Changer for Fisher Plastics
Jonathan Hill, Group Technical Manager for Metalliform Group Limited, parent company of Fisher Plastics, shared his thoughts:
"The new system has been a game-changer in terms of efficiency and performance. It has drastically improved the chilled water supply to the machinery within our factory, ensuring optimal and consistent process temperatures while reducing our energy consumption. We’ve already noticed a significant decrease in our utility bills, thanks to the system’s energy-saving features."
"The installation was completed with minimal disruption, even though we undertook this project over the Christmas period when resources were low. Summit pulled out all the stops to ensure we were fully operational for our January startup. The technicians were extremely knowledgeable and worked closely with our site maintenance team to get the project delivered on time."
"The system has been designed to be user-friendly, and the training provided ensured all our staff know how to fully utilise it. Summit has continued to provide support after installation, checking in to make sure we are completely satisfied with the results. This has shown us that they truly care about their product and our satisfaction. We are extremely happy with our new cooling system and would highly recommend Summit to any business looking for a reliable, efficient, and energy-saving solution."
Future-Proofing with Scalable Cooling Solutions
Summit Process Cooling will continue to provide ongoing support and maintenance, including remote monitoring to ensure optimal system performance. The system has been designed for future scalability, with provisions for a 25% capacity increase and space allocated for an additional chiller if required.
By incorporating advanced energy-efficient technology and optimising existing resources, Summit Process Cooling has provided Fisher Plastics with a future-proof cooling system that delivers substantial cost savings, improved reliability, and a reduced environmental footprint.
For more information on Energy Efficiency and Cooling System Upgrade for Fisher Plastics talk to Summit Process Cooling