
Sign In
CLEANROOM DESIGN
15-05-2015
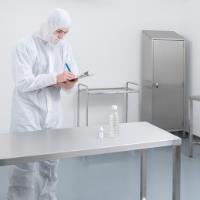
An emerging trend in lab and cleanroom design is moving businesses away from traditional approaches, and towards collaboration and flexibility. Ensuring that such spaces will continue to serve the purpose for which they were created for years to come is key to success.
Future-proofing, collaboration and flexibility have become the focus when it comes to the design of laboratories and cleanrooms. Over the last year, design and manufacturing of hygienic furniture has evolved to meet specific lab requirements. There has also been a clear shift in the way lab users want their cleanrooms to be designed: not just to meet current needs, but to future-proof them for years to come. Two distinct changes in approach have become clear. The first relates to how the project is managed, and the second looks at how aspirations for the end room are considered.
Forward Planning
As many projects entail capital expenditure sign-off, it means there is a fair degree of scrutiny when it comes to design, which requires a demonstration of robust project control, ongoing collaboration and forward planning.
Businesses tend to start the planning process as much as six months before a project commences. The starting point is often the room layout (to scale), documenting the must-have components and logging where there is scope for compromise. This helps to establish priorities when specifying the furniture. The next stage sees computer-aided design drawings supporting the traditional two-dimensional flat layout plan, to help all involved understand what the end room will look like, in a form that is easy to understand. If a lab can maintain close involvement with the contractors and subcontractors responsible for the installation, this will help to mitigate any potential confusion and save valuable time.
Filipe Oliviera, Process Engineer at Biomet, finds this to be true: “It is important to establish, reasonably early in the planning stage, where must-have components can be sourced to avoid complications further down the line. By bringing in the suppliers early on, you can then use their expertise to help define optimal products and the lead times required. We collaborated with designers for our new cleanroom and changing area, many months before it went live. It meant we had time for the specifications to evolve in partnership with them, while ensuring we maintained keen pricing and on-time delivery.”
Collective Experience
Not only are the planning stages of projects starting earlier, but project leads are collaborating with colleagues and users throughout the entire business. Questions are asked about first-hand usage, ongoing requirements and future adaptions. By accessing this collective experience, there is a user consensus on where improvements can be made with the current set-up and discussions into how to make it better. This is a distinct step away from just ‘putting up with it’, and a move towards making iterative improvements for that all-important return on investment.
It can prove extremely useful to meet with end-users so they can explain how each piece of furniture or equipment is being used within their business. This collaboration might include shift leaders, lab, operations and quality managers, and even managing directors. Interaction between all involved is critical to identify the overall goal of the design effort, look at current lab conditions and processes, and predict and allow for future staffing numbers: crucial information to help with the specification.
Oliviera agrees: “At our kick-off meeting, we captured everyone’s ideas and wishes, and used this to shape the final plan, knowing what was important and what was desirable from the very start. From then, it was more about what, when, where and how many.”
Before all the furniture is purchased, a partial set-up can prove useful to test the plan in a way that flat and three dimensional designs cannot. This allows for any changes or tweaks to room layouts, furniture and process flows to be implemented without compromising the whole investment. Taking lean engineering to its logical conclusion, these tests help make sure the room delivers the operational efficiencies that many businesses require.
Fixed versus Modular
Two distinct specification trends have emerged in cleanroom design: customers either opt for generic modules with a flexible placement, or for specific furniture that will be placed in a precise location.
‘Precise fitting’ requires workbenches, shelving and cupboards that are exactly designed for an area or function, with no compromise. Some cleanrooms even fix furniture into the space permanently – whether to the wall or floor – and often include access to plumbing or wiring for the lab or production equipment being used.
In contrast, there is an emerging demand for a more ‘modular’ approach, with the goal of future-proofing a lab – reducing the need for modification and, therefore, down-time. The traditional standard lab design has matured into a fully open and integrated area, seeing users becoming flexible with available space and where furniture is placed. Function inevitably evolves over time, as it accommodates different types of work within the same area.
The modular approach may well have been accelerated either by the need to adapt to new processes or equipment, or to fit in with how lab users work. Creating shared spaces fits into this trend of ‘hotelling’ – moving towards creating communal spaces that can accommodate teams as well as different functions. A preference towards freestanding furniture, rather than more traditional static formats, facilitates easy siting according to need.
Finish and Form
But it is not all about practicality – finish and form are becoming just as important as function. There is definitely a focus on achieving a ‘showroom’ finish in cleanrooms. Viewing windows enable labs and cleanrooms to clearly demonstrate to visitors that they are committed to quality and control, effectively becoming the business’s shop window. Beautifully finished stainless steel furniture, combined with white floors and walls and bright lights, definitely sets the scene of a pristine working environment.
This trend for a thorough design approach in the cleanroom has seen equal importance being placed on the changing room layout. Well-designed changing rooms can help reinforce the importance of maintaining cleanroom standards from the start of the shift. They encourage vital best practice from gowning to washing and drying, and further enforce the hygiene and quality standards required in the workplace. Just as detailed planning of a lab’s layout is becoming the norm, the changing room is also attracting attention. This includes considering how this space is managed to accommodate increased user numbers.
User Feedback
Looking across the whole spectrum of lab design – from initial collaboration, to planning, to finish – it is becoming increasingly important not to neglect the needs of those responsible for the hygienic upkeep of labs. Manufacturers have a responsibility to constantly review their products and furniture to ensure they are conforming to exacting cleanroom standards. Whether that means introducing bins made from non-shedding material, or the removal of weld marks to reduce dirt traps and crosscontamination, manufacturers need to consider if each product is fit for its ongoing purpose.
Direct feedback from people who use this clean furniture and equipment is invaluable. Listening to their insight and knowledge should continue, even after the design and build have been completed.
Open Dialogue
What these trends indicate is that businesses have to reflect a modular approach themselves. Keen to constantly adapt and grow to meet clients’ needs, companies should remain in constant dialogue with the industries they work with. Always listening and being flexible is as valuable as being knowledgeable and informed; continuing to learn about the demands of the industry and lab users – from those that are in charge, to those that keep the cleanrooms clean… is the only way forward.
Sue Springett. Commercial manager
This article is taken from Pharmaceutical Manufacturing and Packing Sourcer, May 2015 issue, pages 22-24
For more information on CLEANROOM DESIGN talk to Teknomek
Enquire Now
List your company on FindTheNeedle.