
Sign In
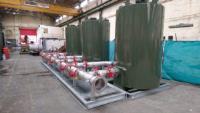
When a UK water utility company was looking for a system to remove impurities from anaerobic digester gases, it needed a system that would meet the stringent clean up requirements and achieve zero plant shut down when carrying out routine vessel maintenance. The solution came in the form of a bespoke Activated Carbon Vessel System that was designed and supplied by Thermtech.
Providing the population with clean drinking water is a dirty job with many processes being needed to remove the impurities from waste water. These processes need to meet stringent compliance regulations to guarantee the production of safe drinking water. One of these processes uses anaerobic digestion, the by-product of which is biogas, which can be used as a valuable source of fuel, provided it is “sweetened” by the removal of the trace amount of contaminants it contains.
Delivering modern filtration
Activated carbon granules or pellets are used for the removal of hydrogen sulphide (H2S) in biogas streams generated from various sources such as landfills, anaerobic digesters or, as in this application, municipal wastewater treatment plants. A granular form of activated carbon, a material containing highly porous carbon particles, is stored in specially designed vessels. When a biogas stream is passed through the vessel, H2S and other impurities such as siloxanes are removed.
With over 15 years’ experience in designing and manufacturing carbon filtration systems, ThermTech was approached by a major project management contractor to the water industry. The outline information centred on the gas flow rate, the percentage of impurities, the maximum pressure drop across the system and the maintenance interval.
The design of the vessels and all of the associated pipework was based on this information to ensure that the gas remains in contact with the carbon for the correct period of time, known as the residence time. Furthermore, it was essential that the final design did not exceed the maximum pressure drop to ensure process efficiency.
The water utility company specified a need to select any combination of gas flow routes to any, or all, of the filtration vessels and for each vessel to have the facility to be independently disconnected and taken off-line for purging and maintenance while the plant continues operation. In this way, routine maintenance could be completed without affecting plant efficiency.
This additional complication to the project affected the overall design, especially in respect of the pressure drop calculations. Depending on the combination of vessels in use at any one time, the residence time and the pressure drop could be affected. The ThermTech designers took all of the project specifications into account before delivering the final design to the fabrication section.
The Solution
Close liaison was established with the large project management contractor and the initial system concept agreed based on providing a modular design to simplify both site installation and planned maintenance when the plant is operational. Each design stage was discussed and agreed to provide the smoothest transition from concept to final design.
The system would comprise three activated carbon vessels including all pipe work and control valves manufactured in stainless steel. The supporting structure, including a complete skid unit, was supplied, enabling easy assembly and mounting of the equipment on site during the installation process.
Each of the carbon vessels has been designed with a volume of 4 m3 to meet the requirements set out by the client and provide a maintenance interval of between three and six months.
For more information on Custom purification system minimises downtime for water utility talk to ThermTech Ltd
Enquire Now
List your company on FindTheNeedle.