
Sign In
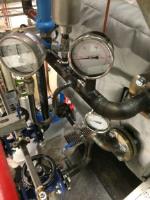
When a hospital on the Isle of Man was looking to reduce operating costs, it worked with boiler manufacturer and contractor McQuillan to seek methods of reducing energy costs. With a payback period of just three years, the installation of three steam boiler economisers will provide an annual energy saving of over £30,000.
Optimised design
The hospital is an old building with limited space for additional equipment and due to the location of the boilers and outlet flues, this posed a challenge for the economiser system design and installation. Structural modifications to the building and an increase of available space to optimise performance was required in order to provide the most effective heat recovery system possible within these constraints.
The client stipulated the need for a robust and proven solution. McQuillan turned to ThermTech who has installed many economiser systems and easily demonstrated the capabilities of their product and design by referring to several previous installations, for which customers were happy to share their positive experiences.
Luke Hall, Project Engineer at ThermTech explains: “We specialise in the design and manufacture of economisers that will provide optimum heat transfer for each application. Each system is custom-made to offer optimum performance and to maximise the re-use of energy. Every application is different so each economiser should be purpose built to achieve the best transfer efficiency for a specific boiler design.
“For example, designs using a standard solution approach are fundamentally based on the boiler running continuously at maximum flow rates. This does not occur in practice, so while this design is simpler than a purpose-built solution, efficiency losses occur in applications operating with a variable flow rate boiler. A modern economiser design suited to the application is therefore recommended.”
Delivering genuine energy saving
As part of the tender process, a budget quotation was initially submitted for three economisers, one for each of the existing boilers installed. When the potential savings in energy costs were fully appreciated, a meeting at the hospital site was arranged and included the completion of a site survey that enabled ThermTech to submit a detailed design proposal for a turnkey solution.
McQuillan undertook the structural and primary fitting work necessary to install the economisers, while ThermTech carried out the installation and commissioning of the new equipment. The highlighted constraints, such as the building layout and the location of the current boilers and their related equipment, were all overcome to ensure a faultless installation. At the same time, any disruption to the hospital heating services was kept to an absolute minimum by completing the installation on each boiler in turn while the remaining boilers continued normal operation.
How Economisers work
Installed between the boiler and chimney, economisers operate on the principle of heat exchange, salvaging the boiler flue gases to pre-heat the boiler feed water. This reduces the amount of energy that is required to heat the boiler feed water to operating temperature.
Usually constructed from carbon steel, the economiser design incorporates finned tubes, containing the boiler feed water, that run perpendicular to the flow of hot gas. These finned tubes transfer heat from the flue gases into the water flow. This process lowers the flue gas temperature while the feed water temperature is increased.
The extent to which the economiser pre-heats the feed water will depend on the specific economiser design and boiler parameters. The key to an efficient heat transfer rate is the design of the finned surface, which needs to be in complete thermal contact with the water tubes.
The result of innovation
A Site Services Engineer at the hospital, commented: “Our remit is to seek out and implement energy saving to reduce public spending on energy. Installing an economiser on each of our three boilers will provide around £15,000 per year per boiler in energy savings. With an economiser investment of £100,000, our payback will be within three years. This, combined with the long-life expectancy of the economisers of around twenty years, made this solution very attractive to us.”
Receiving an award for ‘Best Innovation’ by the Department of Economic Development for implementing this solution, the engineer went on to say: “It is a great feeling for the hospital to be recognised for the work that goes on in the public sector to reduce public spending.”
For more information on Hospital energy saving project wins government award talk to ThermTech Ltd
Enquire Now
List your company on FindTheNeedle.