
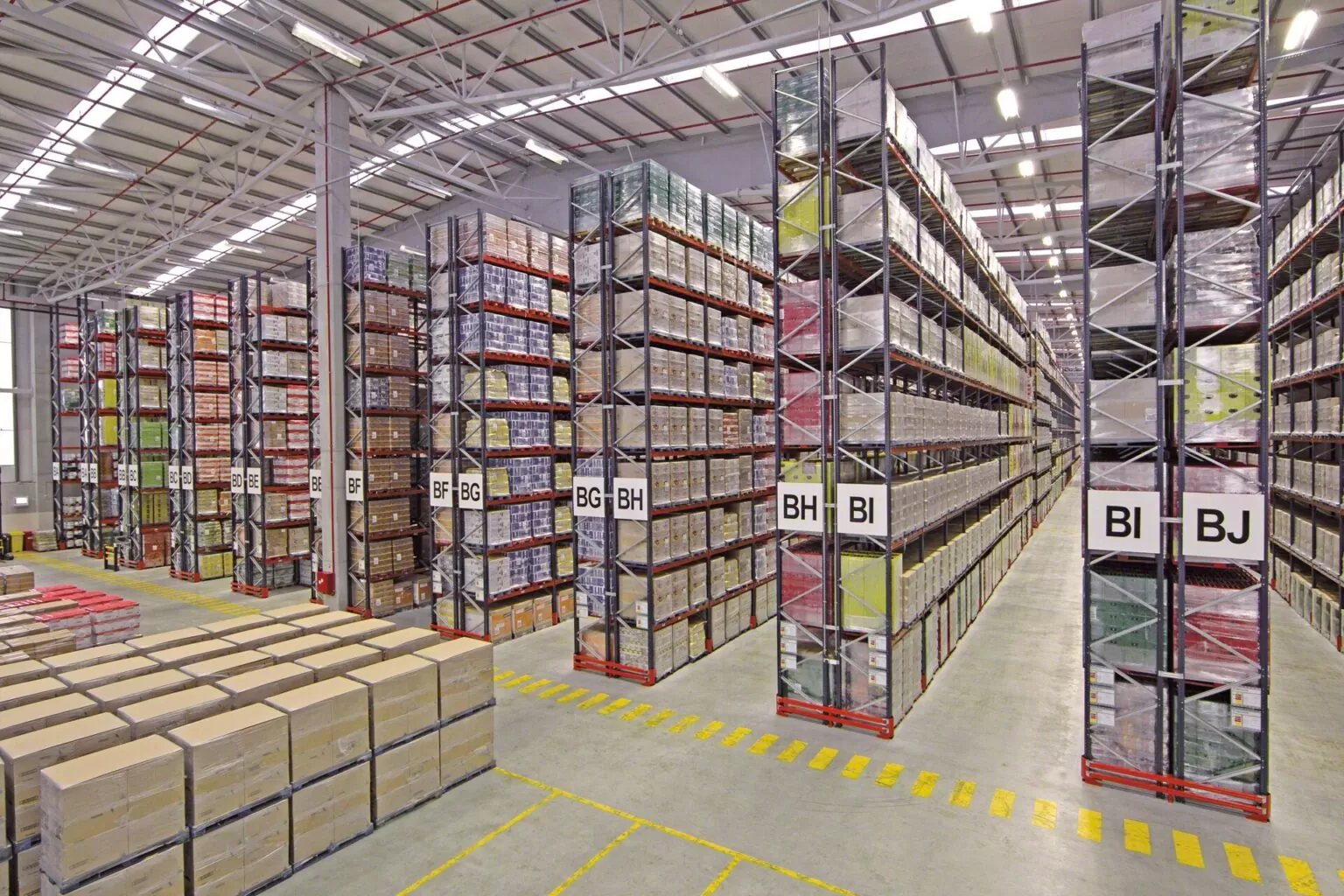
The transformation of warehouses from simple storage facilities into highly efficient fulfilment and inventory management centres has been driven by advancements in forklifts, pallets, and racking systems.
The introduction of narrow-aisle forklifts in the 1950s allowed warehouses to optimise their storage capacity, enabling more inventory to fit within the same footprint. At the same time, stronger racking systems meant shelves could be stacked higher, further increasing storage efficiency.
While these innovations were significant in the early days of modern supply chains, they are even more crucial today, as industries require greater storage capacity and faster inventory management to meet growing consumer demands.
However, every warehouse has a threshold for efficient storage. Once that limit is exceeded, both productivity and safety can be compromised. Striking the right balance between maximising space and maintaining operational efficiency is essential to ensure a safe and profitable warehouse environment.
Key Considerations for Space Between Shelving Units
Forklift Operating Space
Aisle widths must be sufficient for forklifts to safely manoeuvre, lift, and retrieve pallets without increasing the risk of accidents. The required operating distances will depend on the technical specifications of the warehouse’s forklift fleet.
A general rule is that the aisle width must exceed the turning radius of the largest forklift in operation. The figures provided in forklift specifications represent absolute minimums, and allowing extra space where possible is recommended.
As a guideline, aisle space should typically range between 11 and 15 feet between racking units, though this can vary depending on the equipment used in the warehouse.
Proximity to Warehouse Walls
Unlike retail shelving, which is often placed against walls to maximise shop floor space, warehouse racking should be positioned at a safe distance from walls, beams, and upright end frames.
One of the primary reasons for this is stability and safety. Warehouses often use heavy machinery, which can generate vibrations capable of destabilising nearby racking systems. Sudden impacts, seismic activity, or even minor earthquakes can increase this risk.
To minimise the potential for collapses or structural damage, racking should be positioned:
- At least 2% of its height away from the wall in the cross-aisle direction
- More than 5% of its height away from the wall in the down-aisle direction
Beyond safety, maintaining a clear gap between racking and walls offers additional advantages:
- Improved warehouse cleanliness – Easier access for cleaning teams to remove dust and debris
- Safe and convenient maintenance – Ensures quick and unobstructed access to racking for inspections and repairs
- Better airflow and ventilation – Reduces the risk of moisture damage to products, racking structures, and the building itself
While general standards and best practices provide guidance, the ideal space between racking units and warehouse walls ultimately depends on the specific requirements and risk factors of each business. By carefully assessing operational needs and safety considerations, warehouses can optimise storage efficiency without compromising workplace safety.
For more information on How Much Space Do You Need Between Pallet Racking Units? talk to UK Shelving Ltd