
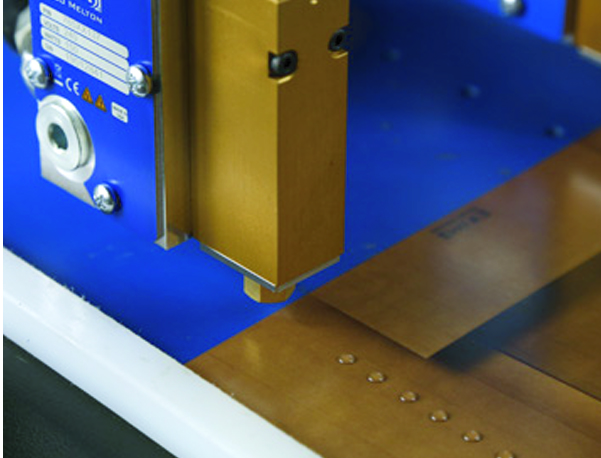
In the fast-paced world of packaging, efficiency and reliability are paramount. Valco Melton's EcoStitch technology is transforming the industry with its innovative all-electric adhesive dispensing solution. This cutting-edge system offers significant advantages over traditional pneumatic units, providing manufacturers with a more efficient, cost-effective, and environmentally friendly option.
The Power of All-Electric Technology
EcoStitch applicators represent a leap forward in adhesive dispensing technology. Unlike their pneumatic counterparts, these all-electric units eliminate the need for compressed air, a significant source of energy consumption in many industrial settings. This shift not only reduces operating costs but also simplifies the production environment by removing the complexities associated with air compressor systems.
Precision and Performance
The heart of the EcoStitch system lies in its high-performance applicators. Capable of cycling up to 15,000 times per minute in short bursts, these units offer unparalleled speed and precision. With a service life of up to 2 billion cycles, EcoStitch applicators ensure long-term reliability and consistent performance.
Substantial Adhesive Savings
One of the most compelling benefits of EcoStitch technology is its ability to reduce adhesive consumption by up to 70%. This dramatic reduction is achieved through precise control and efficient application methods, allowing manufacturers to significantly cut material costs without sacrificing product quality.
Enhanced Operational Efficiency
EcoStitch systems contribute to improved Overall Equipment Effectiveness (OEE) and minimize Total Cost of Ownership (TCO). The VD2 Valve Drivers, a key component of the EcoStitch lineup, offer electronic adhesive volume control and multiple operating modes, including Dot/Gap, Dot Count, Bead, and Stitch Percentage. This versatility allows for fine-tuned control over adhesive application, adapting to various product requirements with ease.
Reduced Maintenance and Increased Safety
Traditional pneumatic systems often require frequent maintenance due to their complex nature and numerous moving parts. EcoStitch valves, in contrast, contain fewer moving parts and no dynamic seals. This simplified design translates to less downtime for repairs and a significant reduction in spare part consumption. As a result, operators spend less time in contact with hot equipment, enhancing workplace safety.
Environmental Impact
By eliminating the need for compressed air and reducing adhesive consumption, EcoStitch technology contributes to a smaller environmental footprint. This aligns with the growing emphasis on sustainable manufacturing practices, helping companies meet their environmental goals while also cutting costs.
Integration and Control
EcoStitch systems offer seamless integration with existing production lines. The VD2 Valve Drivers provide direct Ethernet/IP integration with parent PLCs, allowing for easy incorporation into modern, connected manufacturing environments. Additionally, the all-electric hot melt units feature on-screen adhesive tracking and digital pressure control, giving operators real-time insights into system performance.
In conclusion, Valco Melton's EcoStitch technology represents a significant advancement in adhesive dispensing for the packaging industry. By offering reduced maintenance, lower adhesive consumption, eliminated compressed air usage, and enhanced safety, EcoStitch provides a compelling solution for manufacturers looking to optimize their operations. As industries continue to seek more efficient and sustainable production methods, EcoStitch stands out as a technology that delivers both economic and environmental benefits.
For more information on EcoStitch: Revolutionizing Adhesive Dispensing in Packaging talk to Valco Melton UK