Metal rupture disks are made from thin foils and have no corrosion allowance built into the design. When exposed to corrosive environments the metal components can be quickly compromised. Users should always try to select a base disk material that is compatible with the process medium and does not require additional protection. When additional protection is required Fluoropolymer liners and coatings have been used for decades as a means of protecting a disk from chemical attack.

A Guide To Liners For Metal Rupture Disks
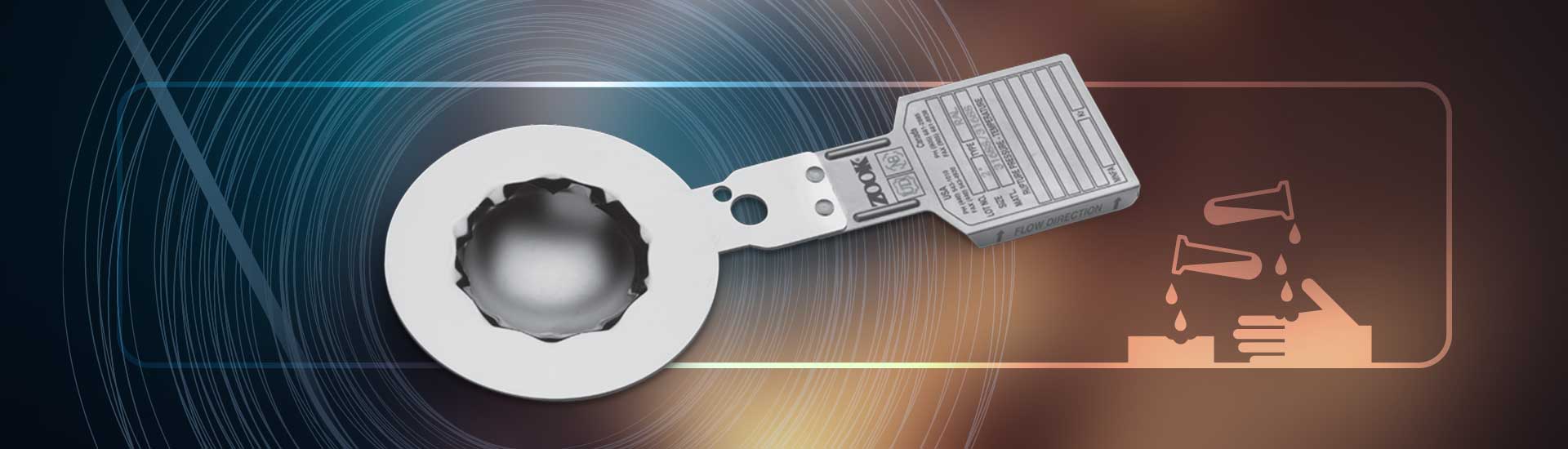
CORROSIVE ATTACK OF A RUPTURE DISK IS AN UNSAFE UNDESIRABLE SITUATION THAT CAN LEAD TO UNPLANNED BURSTS, DANGEROUS EMISSIONS AND COSTLY DOWNTIME.
WHAT IS THE DIFFERENCE BETWEEN A LINER AND A COATING?
A liner in the context of rupture disks is a protective layer, typically a thin sheet of material, placed on the process side or vent side of the disk. Liners are used to provide an additional barrier between the rupture disk and the process media, offering protection against corrosion, chemical attack, or other forms of degradation that could compromise the disk’s integrity and performance.
A coating on the other hand refers to a thin layer of protective material applied to the surface of the disk. Coatings are typically applied to enhance the chemical resistance, reduce friction, or prevent adhesion of process media to the disk surface. The coating is usually bonded to the disk’s substrate, providing an additional protective barrier.
Both liners and coatings serve to protect the rupture disk but do so in different manners and are chosen based on specific application requirements and media characteristics.
In general, liners offer superior performance, reliability, and longevity than coatings for several reasons:
1.
Performance of a coating is inversely proportional to the applied thickness. A liner’s thickness makes it more desirable for corrosion protection.
2.
Coatings rely on adhesion for attachment to the substrate. Many unplanned factors including substrate defects, mechanical damage, impact etc. may be survived by a thicker liner, whereas a thinner coating may be breached, allowing chemical attack of the substrate.
3.
Coatings are manually applied and consistency is not guaranteed. A thicker liner will be less susceptible to failure over time as a result of any given workmanship error.
WHAT TYPE OF LINERS ARE AVAILABLE?
ZOOK offers a full range of liner materials to handle almost any service condition. Liner selection should be based on the corrosion resistance of the liner to the flowing media at service temperature and pressure. Using the correct liner will insure the productivity and life of the rupture disk.
PTFE
PTFE polymer is the choice for the process industry, serving as linings for vessels, piping, pumps, valves, and gaskets at temperatures up to 500°F (260°C). It is easily identifiable by its milky white color. PTFE is subject to creep while under load and is permeable to certain types of molecules making it undesirable for use as a rupture disk liner. ZOOK recommends PTFE be used only as a gasket material.
PFA
These qualities make it an ideal liner for a rupture disks.
FEP
FEP retains most of PTFE’s attributes but has a maximum service temperature of 400°F (204°C).
PVDF
PVDF has attractive properties, like a 250°F (121°C) maximum service temperature, but in all except the rarest circumstances cannot match the performance of PTFE/PFA film. PVDF film should only be used on flat disks due to its poor formability.
CONCLUSION
In conclusion, selecting the appropriate liner for metal rupture disks is crucial to ensure their longevity and reliable performance in corrosive environments. Each liner material—PTFE, PFA, FEP, and PVDF—offers unique properties that cater to specific chemical resistances and temperature tolerances. Understanding these differences and aligning them with your process requirements will help in optimizing the protection of your rupture disks, thereby minimizing downtime and enhancing safety. For further assistance in choosing the right liner for your application, consult with our experts at ZOOK.
For more information on A Guide To Liners For Metal Rupture Disks talk to ZOOK