
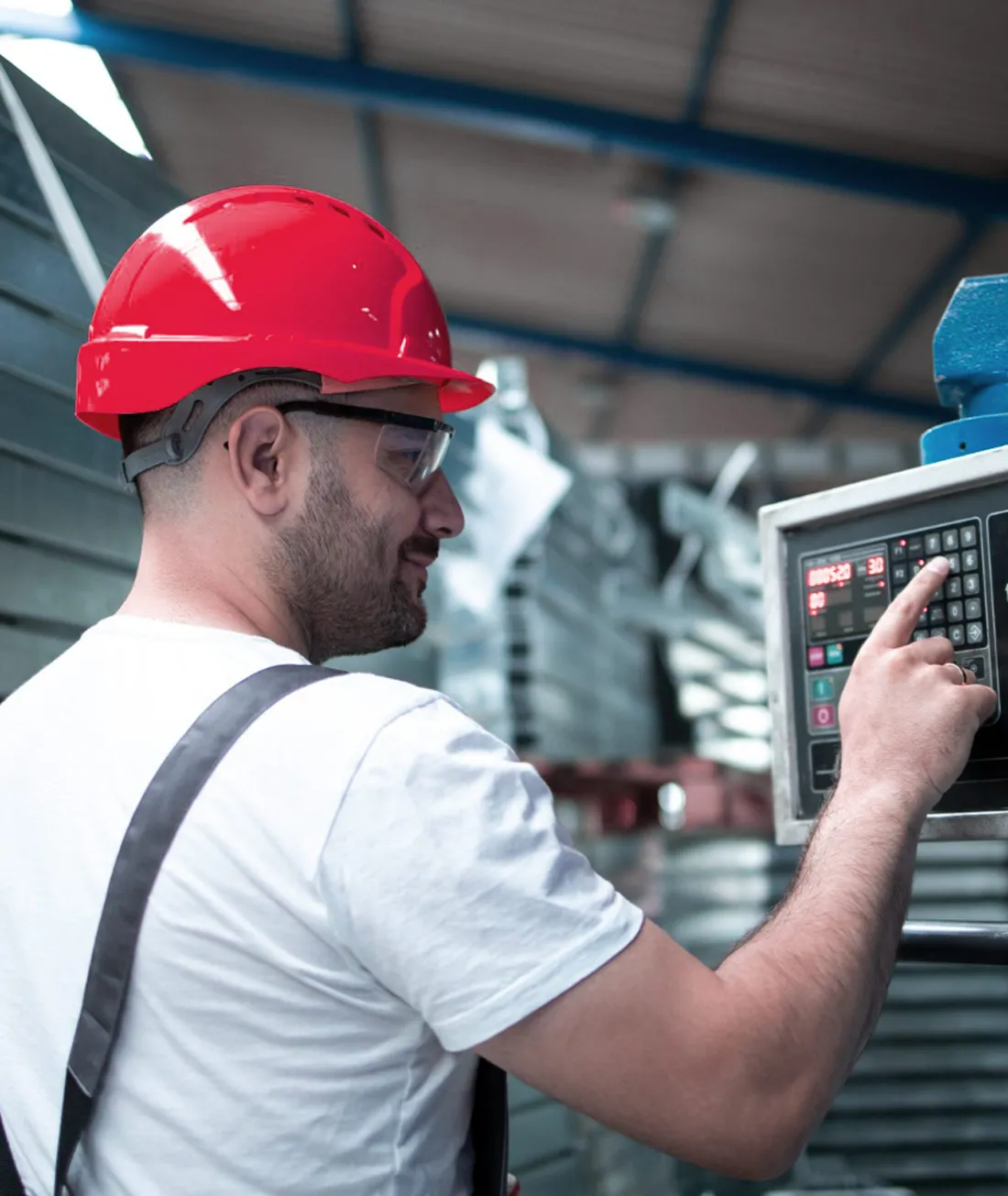
Tolerances in Precision Engineering
Introduction to Tolerances in Precision Engineering
Tolerances in precision engineering are the allowable limits of variation in a physical dimension or measured value. In manufacturing, even the smallest deviations can impact the fit, function, and performance of components. Tolerances ensure that despite slight differences in production, parts can consistently meet design requirements. They play a critical role in high-accuracy sectors like aerospace, medical devices, and automotive manufacturing.
Types of Tolerances in Precision Engineering
Dimensional Tolerances
Dimensional tolerances define the acceptable range of measurement for a part’s length, width, height, or diameter. For example, a shaft might be designed with a diameter of 10mm ± 0.02mm, meaning the actual diameter can vary between 9.98mm and 10.02mm.
Geometric Tolerances
Geometric Dimensioning and Tolerancing (GD&T) controls the shape, orientation, and location of features. It includes tolerances like flatness, perpendicularity, and concentricity, which ensure consistent function across parts.
Surface Finish Tolerances
These define the texture or roughness of a part’s surface, which can influence wear resistance, lubrication retention, and aesthetics.
Importance of Tolerances in Precision Engineering
Fit and Functionality: Proper tolerances ensure that mating parts fit together as intended, avoiding issues like excessive play or jamming.
Cost Efficiency: Overly tight tolerances increase manufacturing costs. Optimising tolerances helps balance cost and quality.
Reliability and Performance: Tolerances ensure products function reliably under expected loads and conditions.
Compliance and Standards: Adhering to tolerancing standards ensures consistency across global supply chains.
Factors Influencing Tolerances in Precision Engineering
Material Properties: Metals, plastics, and composites behave differently under machining and stress, influencing tolerance selection.
Manufacturing Processes: Each process (e.g., CNC machining, injection moulding, 3D printing) has its own tolerance capabilities.
Measurement Methods: The accuracy of inspection tools like CMMs and micrometers affects how tolerances are verified.
Environmental Conditions: Temperature and humidity can cause material expansion or contraction, impacting tolerance control.
Standards and Guidelines for Tolerances in Precision Engineering
ISO 286
This international standard defines a system of limits and fits based on tolerance grades and fundamental deviations. It’s commonly used for defining dimensional tolerances in mechanical engineering.
ASME Y14.5
The ASME Y14.5 standard is the authoritative guideline for GD&T. It standardises symbols and practices used across engineering drawings in North America and beyond.
Tolerance Stack-Up Analysis in Precision Engineering
Tolerance stack-up refers to the cumulative effect of allowable variations across multiple dimensions in an assembly.
Worst-Case Analysis: Assumes all tolerances are at their extreme limits, offering high reliability but often resulting in overly conservative designs.
Statistical Analysis: Uses standard deviation to predict likely outcomes, allowing more efficient designs.
Understanding and managing stack-up is essential in complex assemblies where small variations can have a large impact.
Best Practices for Managing Tolerances in Precision Engineering
Design Collaboration: Involving designers, engineers, and manufacturers early in the design phase leads to better tolerance decisions.
Simulation Tools: Software like SolidWorks and AutoDesk Inventor offers tolerance analysis features to predict stack-ups and functional issues.
In-Process Monitoring: Real-time data from smart manufacturing systems help maintain tighter control over production tolerances.
Training and Development: Upskilling staff in GD&T and modern metrology tools ensures consistent interpretation and application of tolerances.
Conclusion: The Future of Tolerances in Precision Engineering
The future of tolerances in precision engineering is being shaped by automation, AI, and Industry 4.0. Real-time sensors, AI-driven quality control systems, and advanced simulations are enhancing how tolerances are defined and managed. As manufacturing becomes more complex, the importance of precise tolerancing will only grow, ensuring products remain reliable, cost-effective, and high-performing.
By understanding and applying tolerances effectively, engineers can design and manufacture products that meet ever-increasing demands for quality and precision.
For more information on Mastering Tolerances in Precision Engineering for Flawless Manufacturing talk to ABRA Engineering - Precision Engineering Nottingham